When you’re discussing business processes it’s often best to do it visually. There is something about a SIPOC diagram that shows the whole process in such a way that makes it easily understood by your team.
SIPOC helps focus the discussion with your team and helps them agree on what work is going to go forward. It can also help with improving processes. Let’s take a closer look at what SIPOC is, examples of its use in real life and how to make a SIPOC diagram.
What Is SIPOC?
SIPOC is an acronym that stands for Suppliers, Inputs, Process, Outputs and Customers. In practical terms, SIPOC is a process mapping and improvement method that summarizes the inputs and outputs of one or more processes using a SIPOC diagram. Some organizations use the opposite acronym COPIS, which puts the customer requirements first and illustrates the value of the customer to the organization.
The term SIPOC originates from the 1980s and is part of the total quality movement. Today you’ll find SIPOC as a part of the Six Sigma, lean manufacturing and business process management disciplines.
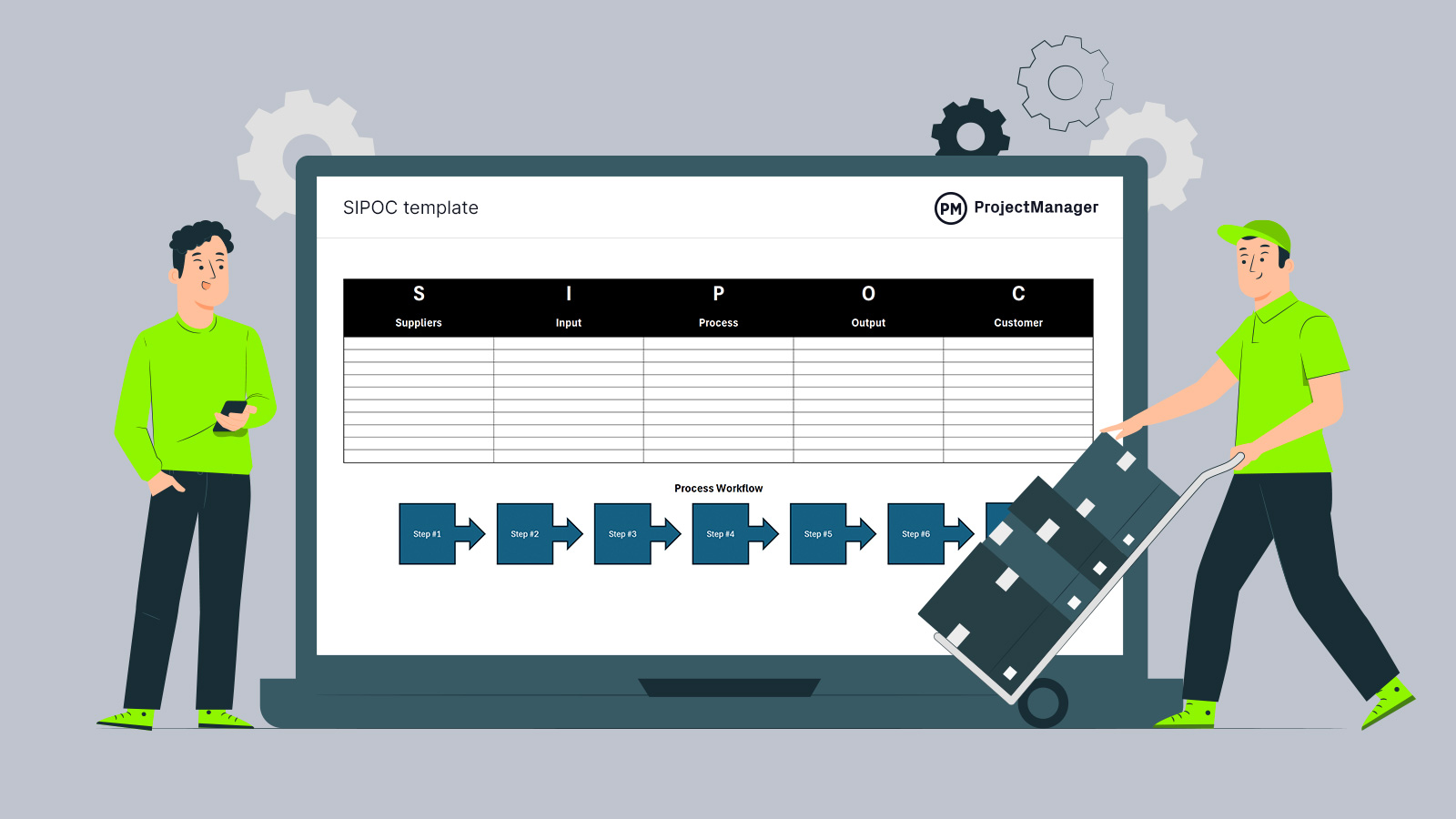
Get your free
SIPOC Template
Use this free SIPOC Template for Excel to manage your projects better.
What Is a SIPOC Diagram?
A SIPOC diagram is a visual business process management tool. It’s a process map that shows how the project goals will be accomplished. It’s a way to make sure that the team and leadership all are on the same page about the business process and customer requirements.
What Should Be Included In a SIPOC Diagram?
Following the acronym, let’s start with what is either the first or last letters: suppliers and customers. These might be internal or external to the organization. The inputs and outputs of the process might be materials, services or information.
The focus is on capturing the set of inputs or outputs rather than the individual steps of the process.
- Suppliers: Providers of inputs into a process.
- Inputs: Resources, such as materials, needed to complete the process.
- Process: Steps that convert inputs to outputs.
- Outputs: Product or service created from the process.
- Customers: Recipients of outputs.
Those elements are then collected in a SIPOC diagram. Project management software can help you collect all the elements for your SIPOC and then organize them into a plan of action. ProjectManager is online work and project management software that helps you organize tasks to better execute them. Our multiple project views lets you work how you want. For example, you can gather all the data from your SIPOC in a task list and then assign tasks, set priorities and even see the status of the work once it begins.
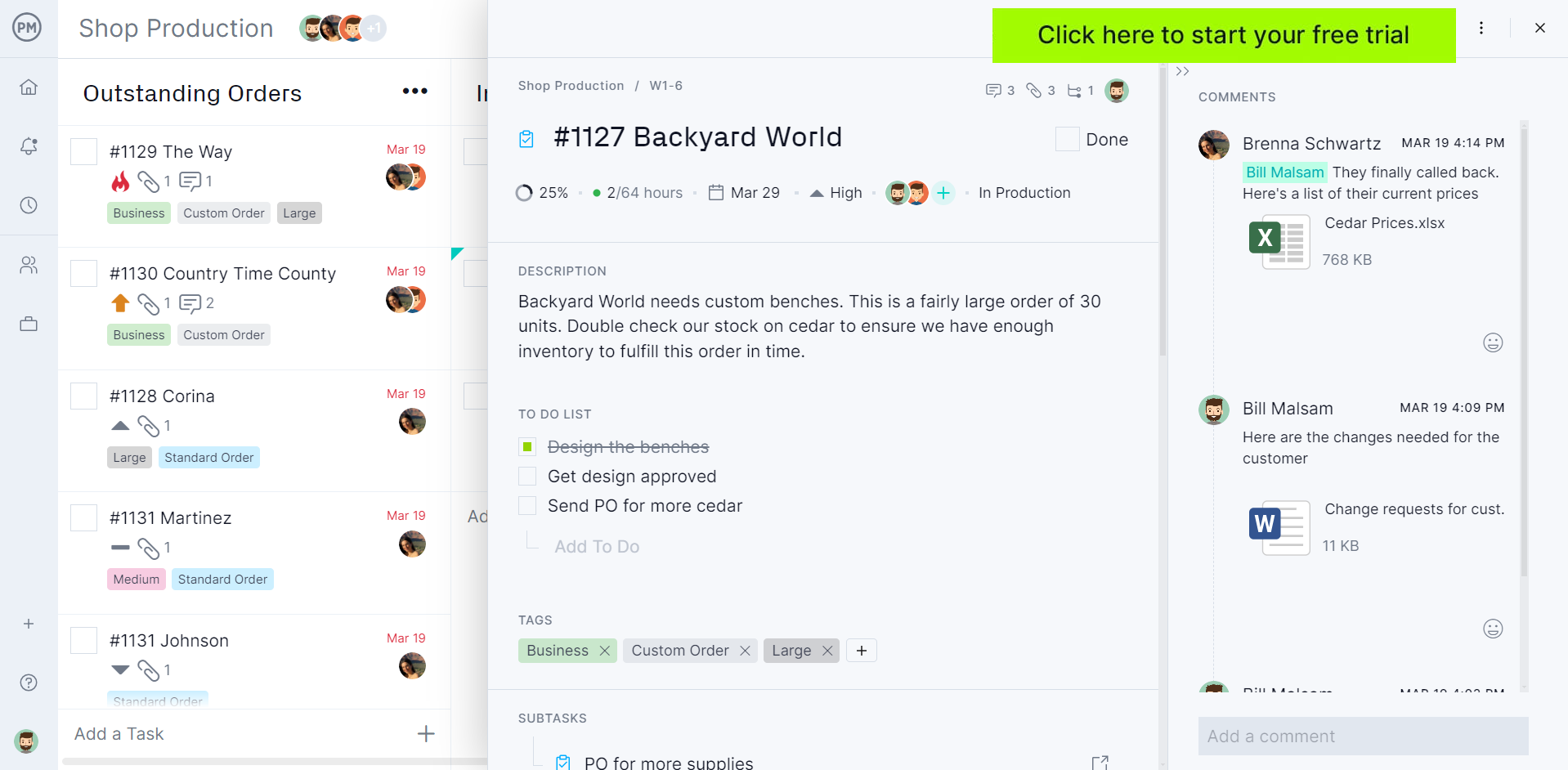
When to Use the SIPOC Model
The SIPOC model is a helpful tool for project management and process improvement. We’ve outlined some scenarios where using this model is especially useful.
Six Sigma Implementation
SIPOC and Six Sigma are closely related as SIPOC is the foundational tool within the Six Sigma methodology. SIPOC is primarily used in Six Sigma’s “define” phase to provide a high-level overview of a process to define the scope and boundaries. It also identifies key elements of a process that coincides with Six Sigma’s emphasis on stakeholder roles and accountability.
Manufacturing Projects
SIPOC diagrams are also highly popular in manufacturing projects as they offer a clear and high-level perspective on production processes. For example, they outline important components such as suppliers (raw material providers), inputs (instructions, tools, materials), processes (quality checks, packaging), outputs (finished goods) and customers (end users). It ensures alignment across departments as it offers a shared understanding of how inputs flow through processes to generate outputs.
Service Design
SIPOC diagrams are also used in service design as they map the end-to-end process to deliver services. It’s a structured approach that guarantees services are designed while thinking of customer needs so expectations align with outcomes. For example, when creating a customer support workflow, SIPOC demonstrates how inquiries are received, processed and resolved, identifying touch points and pain points in the customer journey.
Process Mapping and Improvement
In process mapping and improvement, SIPOC diagrams offer a structured approach to optimizing workflows. It’s a high-level view that makes complex processes simple, making it easier to see critical areas for improvement. It helps project managers identify gaps, inefficiencies or redundancies in processes. SIPOC also identifies areas where customer expectations aren’t being met and acts as a communication tool to align stakeholders on process components.
How to Create a SIPOC Diagram
The SIPOC diagram is an important visual tool that is easy to create. It helps to define who supplies the input to the process, what raw materials are placed in the inputs, the customer requirements of the process and more. First, you have to choose a business process that will benefit from creating a SIPOC. Then to create a SIPOC diagram, follow these steps.
- Identify Suppliers: Who are the suppliers that will provide you with the materials you need for your inputs? They should be listed here. There might be a different supplier for each input. If that’s the case, list them all. By supplier, we mean anyone who has a direct impact on the outputs.
- Identify Inputs: Now you want to identify the raw materials and other resources needed for your business process to work. You don’t have to list every single one, only those that are important, overarching inputs.
- Outline the Process: This is an overview of the business process. Only list the four or five high-level steps that consist of actions and subjects. This is like the starting and ending points in the process or it could be a simple flowchart.
Free flowchart template Download now - Define Outputs: Use nouns to describe the outputs. These can be materials, products, services or information.
- Identify Customers: Define who will want or who you are targeting with the outputs in your business process. A customer doesn’t have to be external, they can be coworkers, board members, etc.
- Analyze Customer Requirements: What are the process measurements or requirements for the product, service or information? These are usually determined by the customer or a regulatory body.
Free SIPOC Diagram Template
Ready to make your own SIPOC diagram? Use this free SIPOC diagram template for Excel. It has a table and diagram all set up for you to identify your suppliers, inputs, processes, outputs and customers. Just input your values and you’re ready to go.
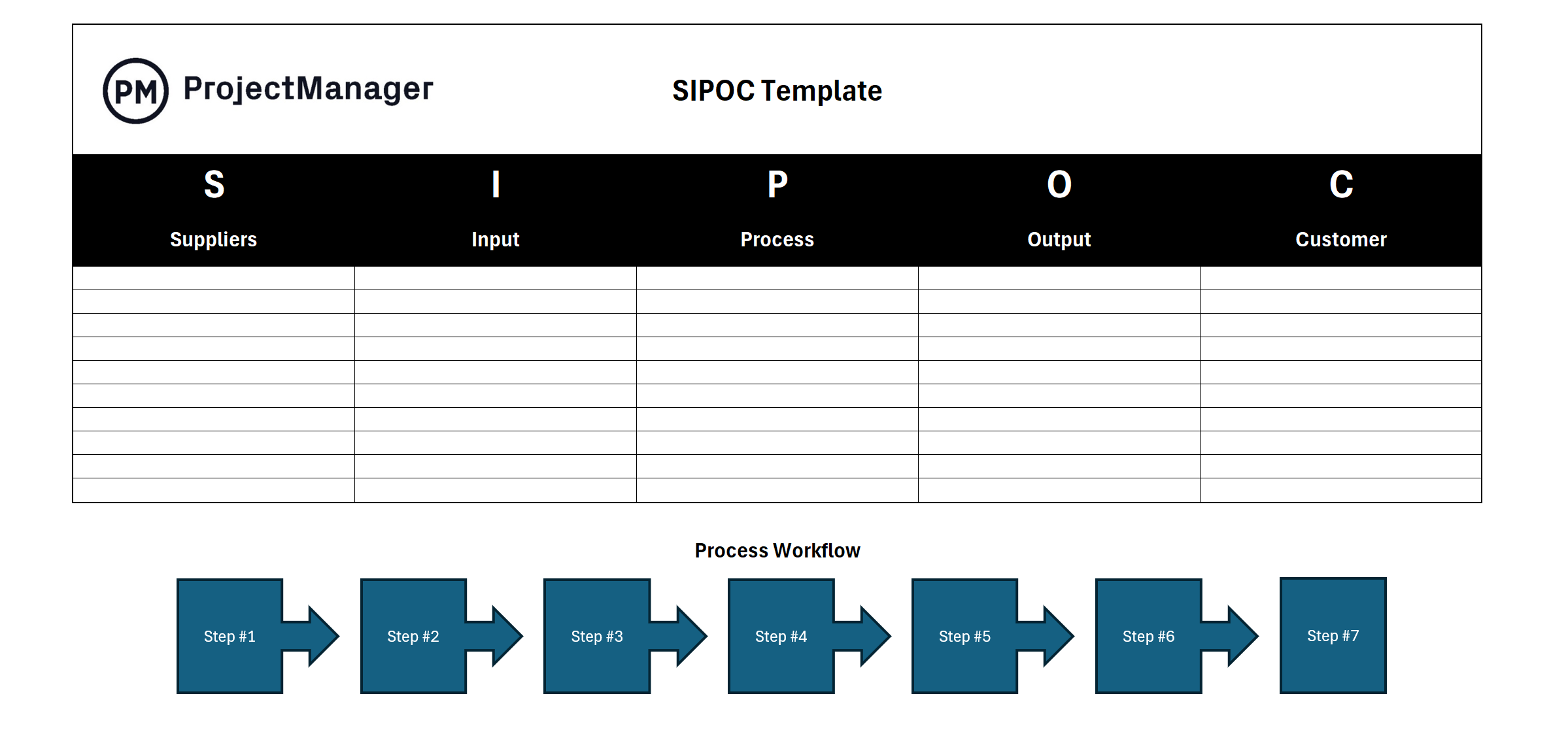
SIPOC Examples
SIPOC examples are an ideal way to visualize a real-world scenario that illustrates the SIPOC model. It shows how the framework operates in a practical setting and helps map the key elements in a process. As a result, teams can identify potential problems or areas of improvement in their own processes.
Manufacturing SIPOC Example
Below is a simplified example of a manufacturing SIPOC diagram. Keep in mind that a real-world production planning process typically involves more details when it comes to steps, suppliers and considerations.
A manufacturing company is using a SIPOC model to assemble new office desks so they are ready for use. To start, make a table that has five columns, each representing one of the five words that make up the SIPOC example. In this case, there are various suppliers including timber wood suppliers, hardware suppliers for screws and brackets, paint and/or finish suppliers and tools and machinery suppliers.
Next comes inputs that represent anything used or consumed during the process to create the desired outputs. In this manufacturing SIPOC example, the inputs include wood planks or sheets such as MDF or plywood, hardware such as screws, nails or brackets, paint, varnish or laminate, cutting and assembly tools as well as design specifications or blueprints.
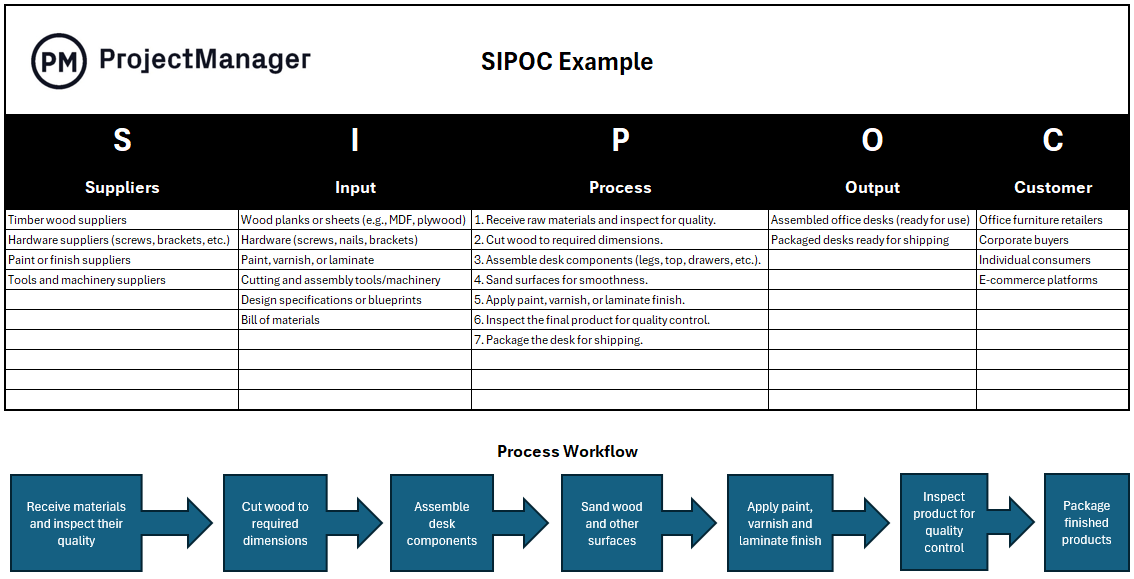
The process column comes next. Once the raw materials are received, they’re inspected for quality. The wood is then cut to the needed dimensions so the desk components such as the legs, drawers and top can be assembled following the bill of materials instructions. Next, sand surfaces for smoothness and apply paint, varnish or laminate finish. The product should be inspected for quality assurance before the desk is packaged for shipping.
The outputs are the end products that are ready for use. In this case, it is the assembled office desks and the packaged desks ready to be shipped. The customers in this example may include office furniture suppliers, corporate buyers, individual consumers and e-commerce platforms.
Process Management SIPOC Example
To keep things simple, imagine a food and beverage business that’s mapping one of its daily operational processes, making healthy smoothies.
To begin, create a table with five columns for the five words that make up the SIPOC acronym. First, there are the suppliers of inputs, which in this case are the ingredients, equipment and other supplies such as cups, straws and napkins needed to make and serve the smoothies.
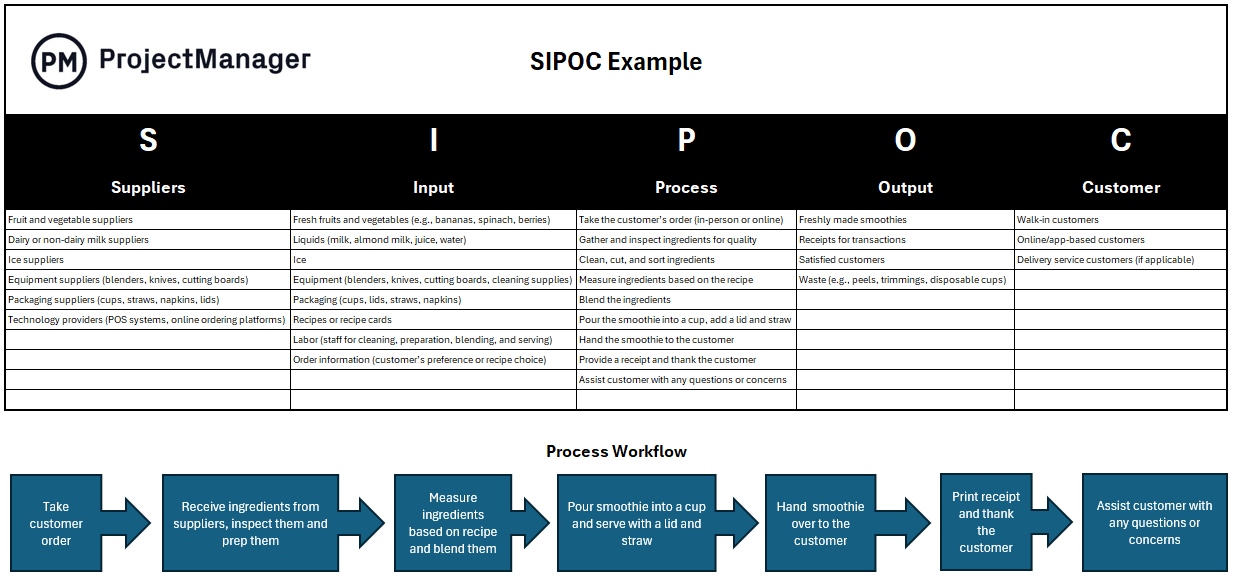
Now we’re getting to the process. It starts by taking the order from the customer, then the ingredients are cleaned, cut and sorted. Once the ingredients are ready, they’re blended as required by the recipe. Then the smoothie is served and handed over to the customer.
The output of this process is a delicious smoothie and hopefully a happy customer. You provide the receipt, and they might give you a tip for good service. This finally leads us to the customer, who might be a walk-in customer or someone who orders through the website or app.
Pro-Tip: To improve the quality of your process, consider creating automation for your task statuses, and designate specific people to approve tasks and products. Workflow automation software can help.
In this video, Jennifer Bridges, PMP, explains what SIPOC is and the SIPOC example above.
Here’s a screenshot of the whiteboard for your reference!
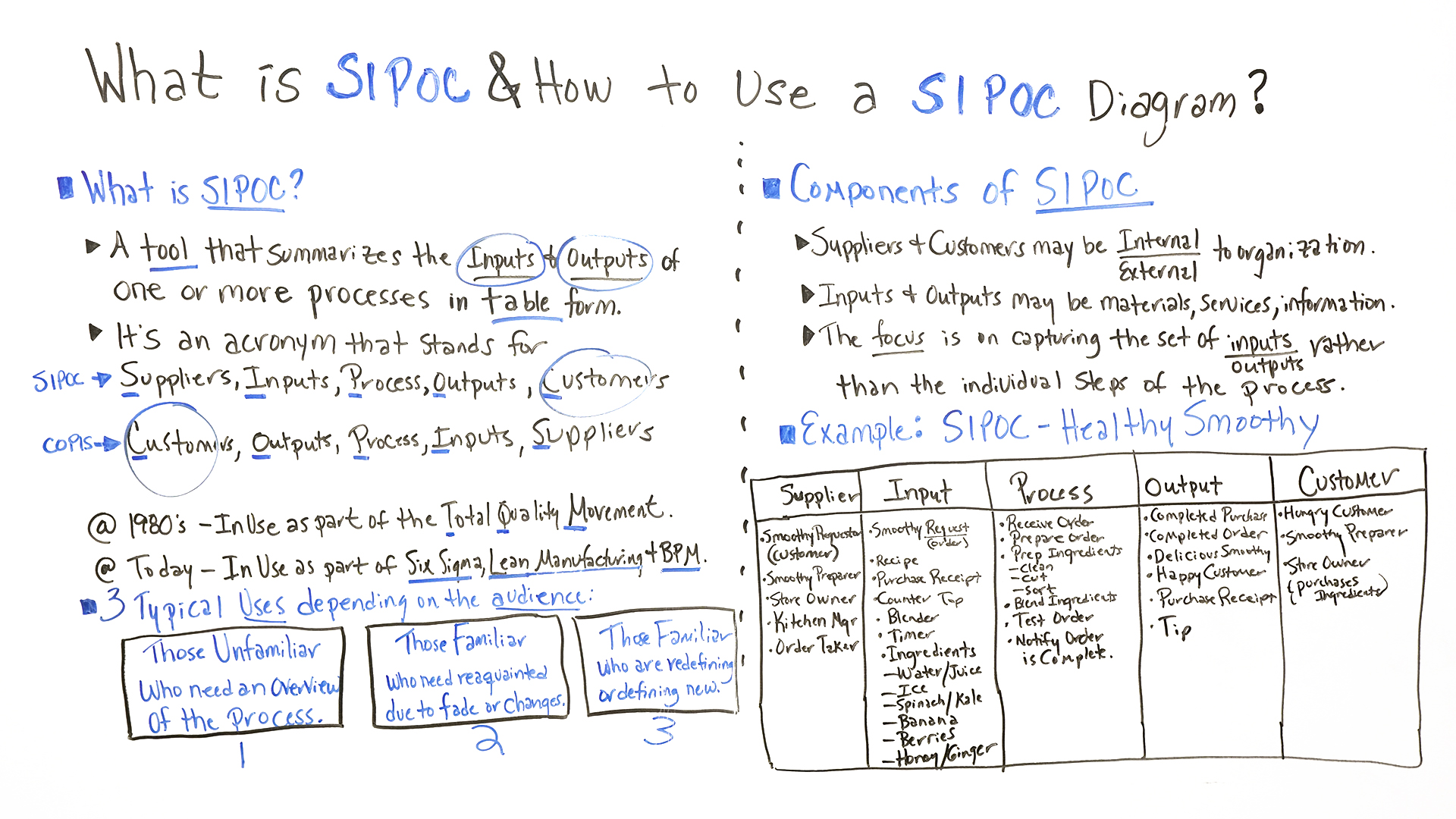
Benefits of the SIPOC Model
The SIPOC model offers businesses several key benefits. Let’s look at only some of the benefits below.
Facilitates Continuous Improvement (Kaizen)
For one, SIPOC models allow for continuous improvement, also referred to as Kaizen. This is a Japanese business philosophy revolving around continuous improvement. As data is collected and analyzed in the SIPOC diagram, it allows project managers to make data-driven decisions.
Helps with Quality Assurance and Quality Control
SIPOC also helps with quality assurance and quality control by offering a structured framework. It defines the desired outputs from the customer’s point of view and identifies the critical inputs needed to produce these outputs. The SIPOC model also facilitates communication and collaboration among stakeholders so everyone is on the same page in terms of quality expectations.
Provides Insights for Value Engineering
Another benefit of the SIPOC diagram is that it allows value engineering teams to concentrate on activities that contribute to creating customer value. The entire process is mapped to help see potential areas of waste such as unnecessary activities, overproduction or defects. Once areas of improvement are identified, the SIPOC model makes it easier to prioritize these efforts.
Can Help Increase Customer Satisfaction Levels
The SIPOC model can also play a large role in contributing to increased customer satisfaction and loyalty. For example, it focuses on customer needs by explicitly defining outputs and understanding customer expectations. It also revolves around enhancing communication and collaboration among stakeholders.
Disadvantages of the SIPOC Model
While the SIPOC model has its value, there are some limitations to keep in mind. In some cases, the high-level view can oversimplify complex business processes. It doesn’t do a good job of capturing the details of intricate processes. The focus on key elements also may not offer the right level of detail for an in-depth analysis or to reveal the relationship between different activities.
SIPOC models are also static in nature, so they might not be suitable when process requirements evolve. If the team isn’t well versed in what a SIPOC diagram is, they may not fully understand its purpose or limitations.
ProjectManager Turns SIPOC Diagrams into Interactive Plans
SIPOC is a great tool to diagram the inputs and outputs in your business process. But once everyone is on the same page you’re going to need to plan, execute and monitor that project. ProjectManager is award-winning work and project management software that has multiple project views that allow everyone to work how they want, no matter where they are, how they work or even if they’re in a different department.
Make Plans That Meet Customer Requirements
Organize all the tasks that you need to create the product or service your customers want with our online Gantt charts. They put your project on a visual timeline so you can see the whole schedule in one place, link dependencies and set milestones. You can also filter for the critical path and create a baseline to measure actual progress against your plan to keep on track.
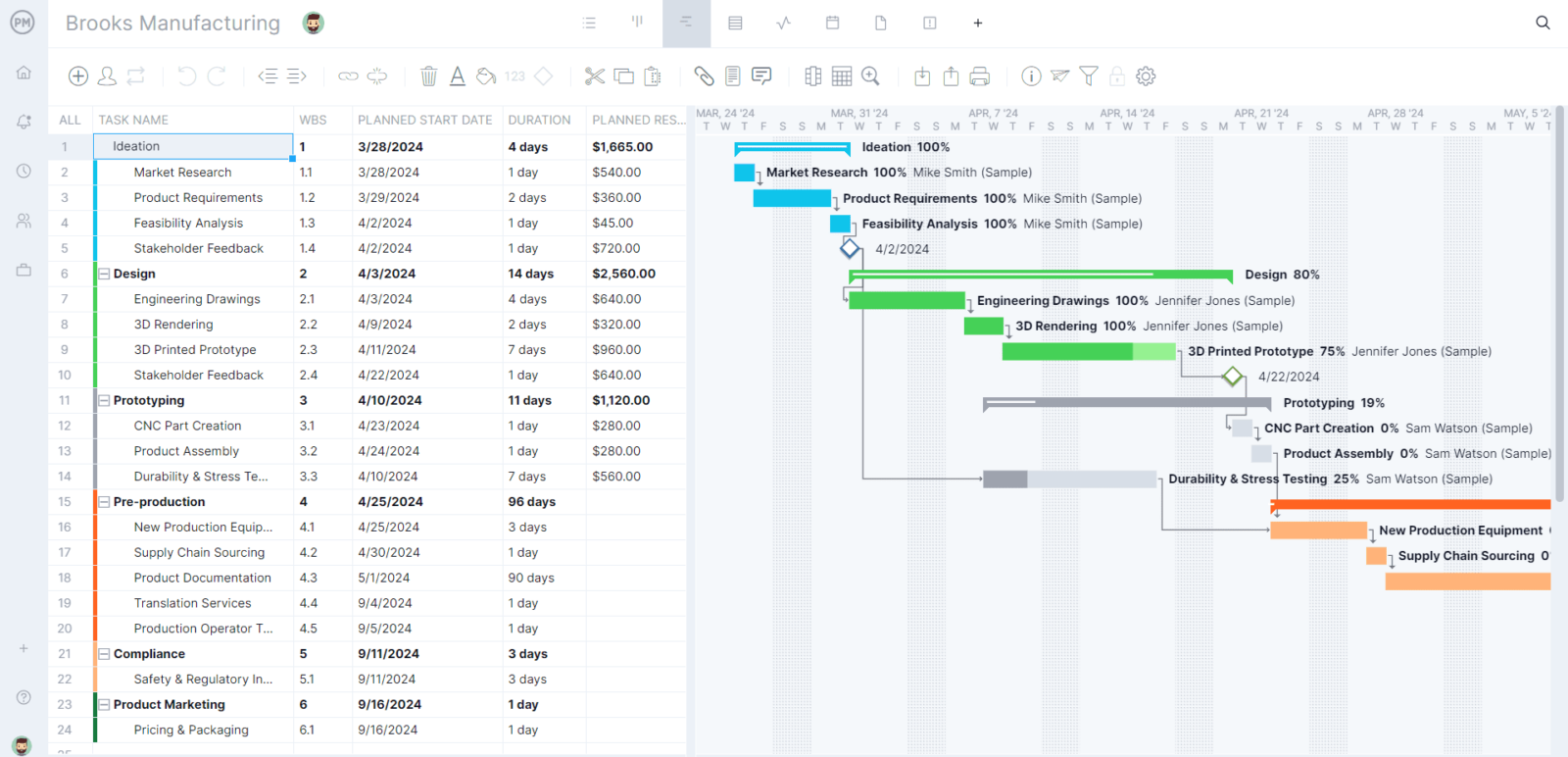
Monitor Business Processes With Kanban Boards
Once the team starts to execute their tasks managers get visibility into their process with our kanban boards. If there’s a potential bottleneck, managers can easily reallocate resources and keep their teams working. Teams get the autonomy to manage their backlog and plan sprints together with our collaborative platform.
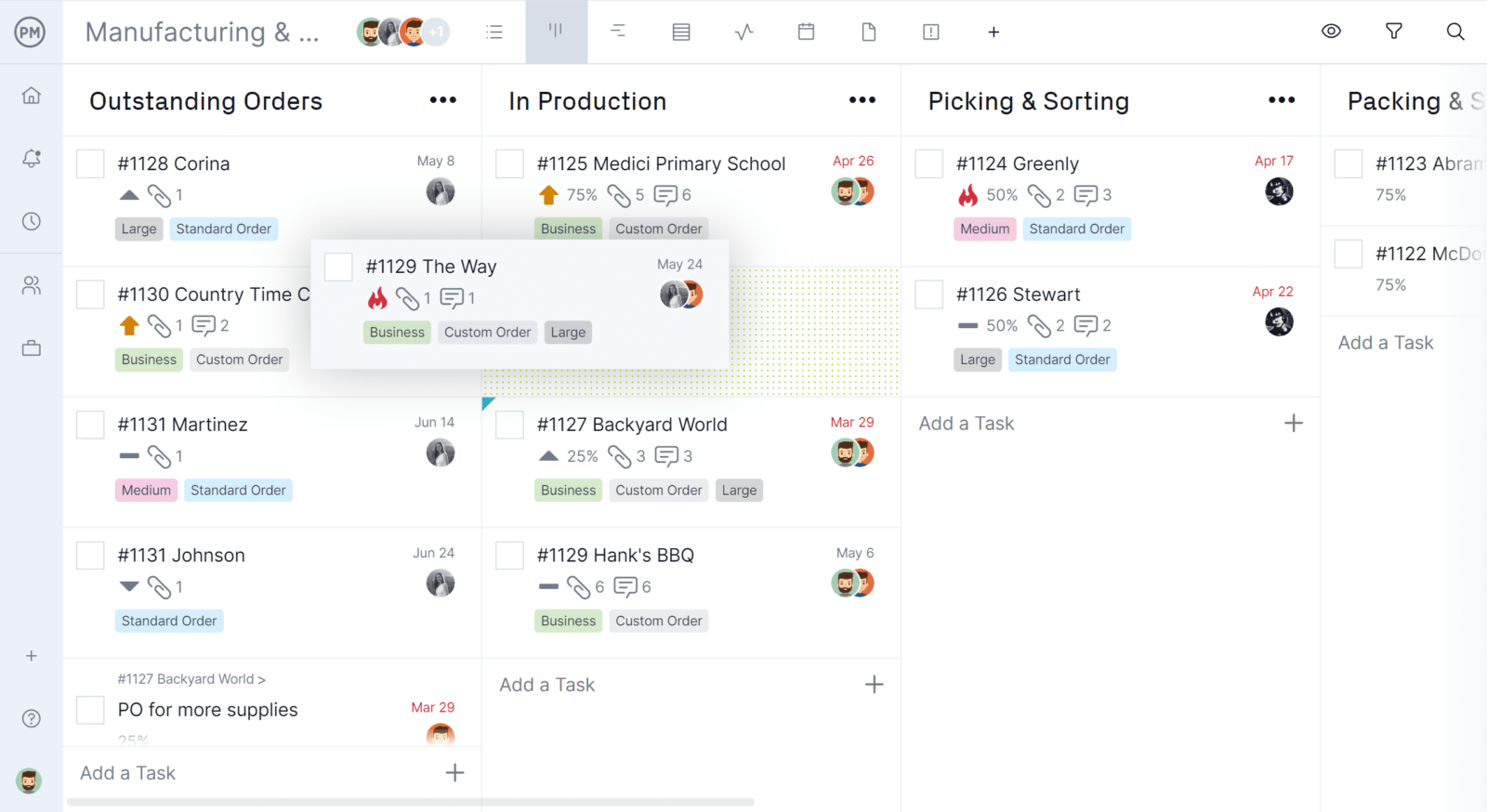
Get Real-Time Updates on Progress and Performance
Keep updated on progress with real-time dashboards that collect live data and automatically display it in colorful graphs that monitor six project metrics. It’s like an instant status report at your fingertips. Better yet, there’s no setup required as with inferior software.
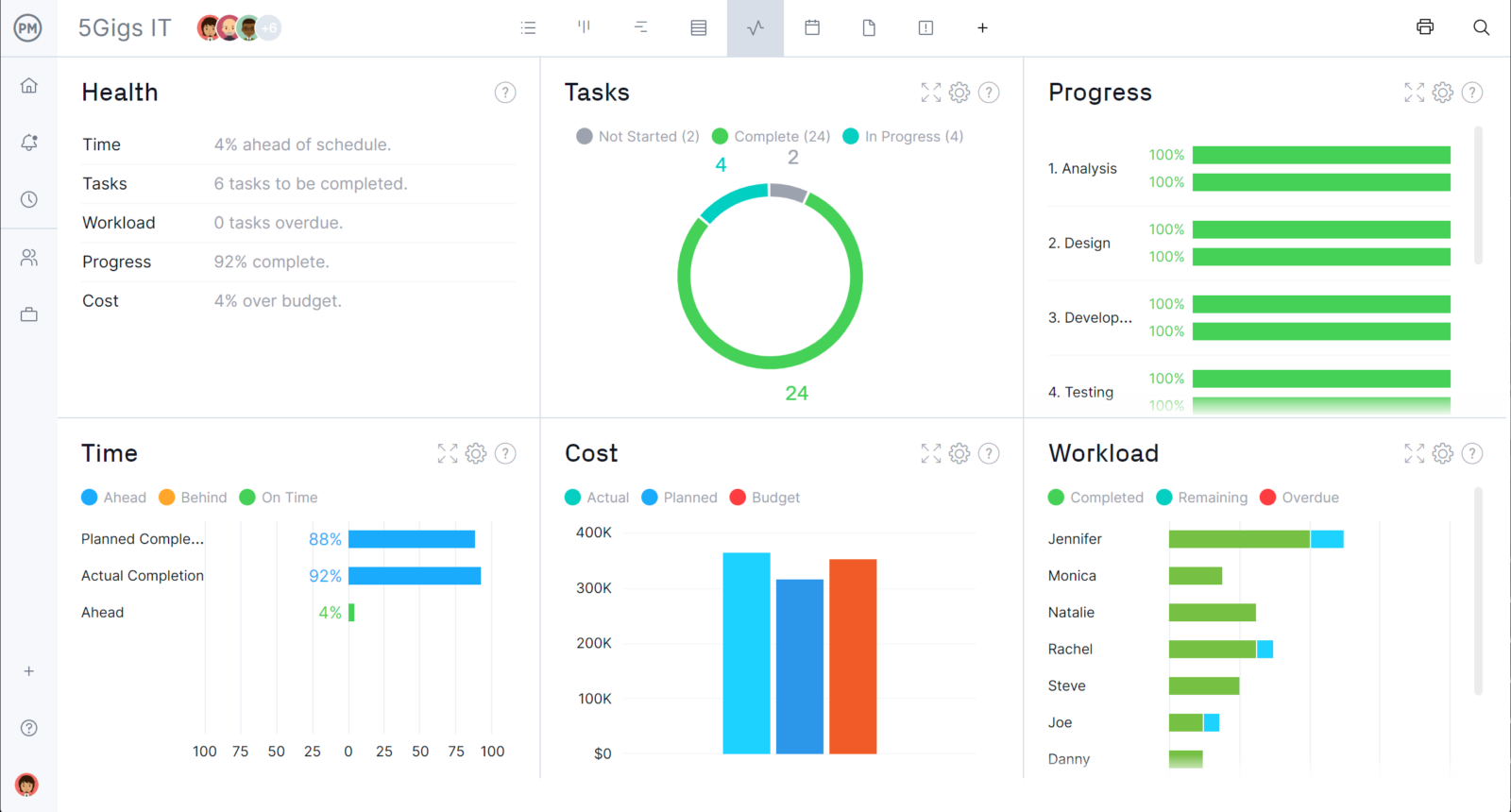
Our software also has one-click reports that can be filtered and easily shared with stakeholders. Custom workflows and task automation help you control the business process. While email notifications and in-app alerts update you on any comments, shared files or updates to the tasks. Fulfill your SIPOC with ProjectManager.
SIPOC FAQ
Here are some of the most frequently asked questions about SIPOC, we hope they’re helpful for you.
What Is the Difference Between SIPOC and COPIS?
The main difference between SIPOC and COPIS is in their starting points. SIPOC starts with suppliers and inputs and is ideal for understanding an existing process. COPIS, on the other hand, is more customer-centric and focuses on meeting customer needs and designing processes accordingly.
What Are the SIPOC Requirements?
The term SIPOC requirements reference the constraints, measurements and customer requirements of a SIPOC model.
What Is a SIPOC Map?
A SIPOC map or SIPOC diagram documents the suppliers, inputs, processes, outputs and customers of a business process.
ProjectManager is online work and project management software that connects hybrid teams and helps them collaborate to work more productively. No matter where you work or when you work we keep you connected. Join the teams at NASA, Siemens and Nestle that have used our tool to deliver success. Get started with ProjectManager today for free!