It’s been around for three decades, but Six Sigma can still be somewhat of an enigma. This methodology can mean different things within various organizations or circumstances, but there’s a way to broadly outline this business process improvement methodology and define its beginnings, rise, use and implementation.
There has been some backlash against Six Sigma in recent years, some of which is warranted and will be discussed, but the process as a whole proves a valuable tool in reducing defects in product manufacturing, especially when paired with agile thinking, lean manufacturing and capable project management tools.
What Is Six Sigma?
To start, let’s define the term Six Sigma. As noted, it’s a methodology used to improve the output quality in a process. It does this by first identifying, and then removing, the causes of defects. This is achieved via a set of quality management methods that feature both empirical and statistical approaches. A staff member with Six Sigma expertise is also usually hired to monitor the process.
Six Sigma was first introduced by Motorola engineer Bill Smith in 1986 when it was registered as a trademark. But it was 10 years later when Jack Welch made it central to his business strategy at General Electric that it became popular in the broader business world.
Project management software is used for approval and review of project performance in accordance with Six Sigma practices. ProjectManager is project management software that offers multiple project views with one view particularly ideal for Six Sigma; the board view. The kanban board allows managers to visualize the workflow of their teams and is ideal for workflow automation and task approvals. This allows teams to review and approve only those deliverables that meet their quality standards. Get started with ProjectManager today for free.
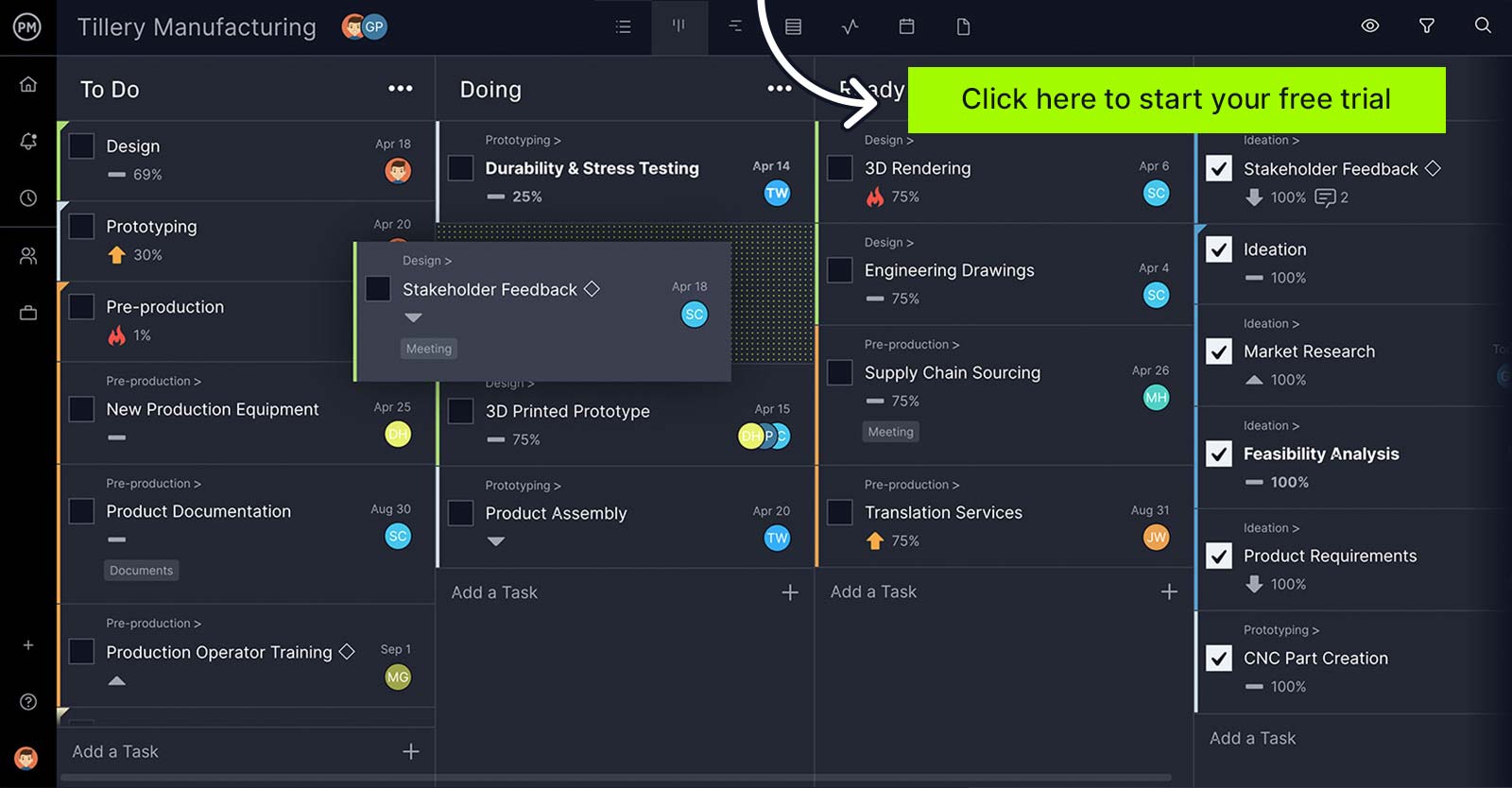
History
While Six Sigma might have been trademarked in the 1980s, its history stretches much farther back. The concept was introduced, though under another name, as the normal curve by Carl Friedrich Gauss (1777-1855). It further developed in product variation in the 1920s when Walter Shewhart showed that the three-sigma process needed correction. Engineer Bill Smith ultimately trademarked Six Sigma and it was this development that lead to Motorola documenting over $16 billion in savings.
Since the 1980s, the use of Six Sigma has been adopted by companies across the globe and it’s evolved into more than a quality system but a way of doing business. It has been described as a vision, philosophy, symbol, metric, goal, methodology and more.
Six Sigma Methodologies
For our purposes, let’s look at Six Sigma as a methodology. Six Sigma methodology is used to improve business practices with statistical data and analysis in order to make better decisions based on facts rather than best guesses. This is done by controlling variation and understanding what causes them.
Processes are then made more predictable and, therefore, profitable for businesses. The six sigma methodology is not just a training session but an approach that is founded on data and targeting projects with quantifiable business outcomes. This approach has shown itself to be valid as it has been implemented across many industries that have documented savings and customer satisfaction.
DMAIC Methodology
The core tool of the Six Sigma approach is the DMAIC roadmap, a more scientific method for project development. It’s a flexible, formalized problem-solving process that includes the following five steps:
- Define: This step is used to figure out the business problem, what the goal is, the potential resources, the project scope and the timeline for completion. This is often detailed in the project charter, where what you know about the project is collected and any facts related to the work are defined, objectives are set and the project team is established.
- Measure: You’ll now want to establish a baseline to have something to measure against when you’re improving processes. This is where you collect the data to put the work in context. The team will then make the determination on what will be measured and how. The better the data, the better this system performs.
- Analyze: Next comes identifying what’s preventing the progress of the process so it can be eliminated. Again, you’ll use a data collection plan until you discover the root causes of the problem. This process involves complex analytical tools, some of which include: listing and prioritizing potential causes of the problem, prioritizing root causes to improve steps, identifying how process inputs impact process outputs and creating detailed process maps.
- Improve: Test and implement solutions to the identified problems using creative solutions to eliminate root causes and prevent them from coming up again. This is done with various brainstorming techniques and other problem-solving methods. It’s suggested that focusing on the simplest and easiest solution is best. Test those solutions, and figure out what risks are inherent. Then create an implementation plan, and execute improvements. A SIPOC diagram is often used in Six Sigma in order to perform this step.
- Control: To ensure that these improvements are sustainable, monitor them by creating a control plan. Be sure to update that plan as needed. You can develop a control chart to assess the stability of the improvements as the project moves forward.
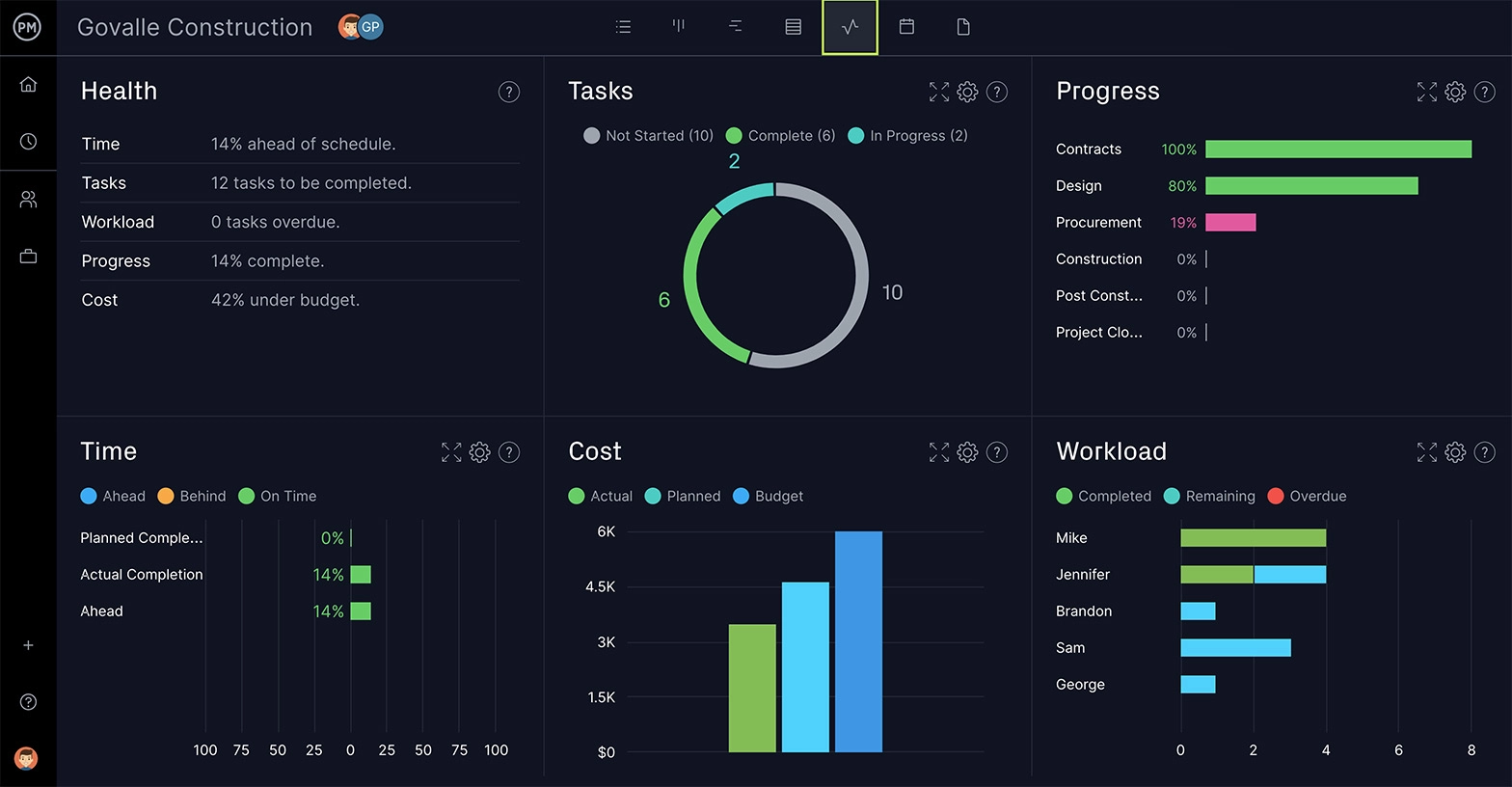
There’s a silent R that some organizations add to the DMAIC, which stands for Recognize. This is a matter of priority, meaning that the team recognizes the right problem to focus on at the right time.
These DMAIC steps should act as a loop in that you need to repeat them and apply the changes to other processes in the project. Share the results with everyone on the project and even outside the organization to develop a network of support. It’s also smart to thank participants to maintain good morale regarding thorough and difficult work.
DMADV Methodology
A variation on DMAIC is the DMADV methodology. Though lesser-known, it’s an ideal methodology for the new product design process. Like the DMAIC, it shares the first three steps, though defines them in slightly different terms.
- Define: Define the process and design goals of your project.
- Measure: Next, identify and measure the critical-to-quality characteristics of the product, service or process. Be sure you’re not neglecting risk and production capabilities.
- Analyze: Here’s where you choose the best design after analyzing the data you collected in the first two steps.
- Design: Once you have a design, start building and testing the product, service or process.
- Verify: You need verification and validation to ensure your design output meets the design input requirements and that your product is performing as designed in a real-world environment or simulated conditions meant to mimic that environment.
Just as with DMAIC, you want to look at the methodology not as an end but as a continuous loop of revising and improving. Following this methodology from start to finish will help you develop the highest standards of quality. This leads to improved customer satisfaction and higher profits for the company.
Why Six Sigma?
The creed for Six Sigma can be broken down into three assertions:
- The continuous effort to achieve stability and a predictable result from a process is what makes a business successful.
- There are characteristics to manufacturing and business processes that are definable and measurable. These characteristics can be analyzed to control and improve processes.
- From the top-down, the entire organization must be committed to sustaining quality improvements for them to be achieved.
What Are the Features of Six Sigma?
Six Sigma isn’t the first technique developed to improve processes, but it differs from others in three significant ways:
- It’s focused on measurable and quantifiable financial returns.
- Leadership is critical.
- Data and statistics are the basis of decision-making instead of assumptions or guesses.
Related: 20 Free Project & Work Templates for Excel
Lean Six Sigma
Six Sigma has proven itself adept at working with collaborative teams since the year 2000 when it developed into Lean Six Sigma. This was first codified in the book Leaning into Six Sigma: The Path to Integration of Lean Enterprise and Six Sigma by Barbara Wheat, Chuck Mills and Mike Carnell. Since then, Lean Six Sigma has been used in a variety of economic sectors, such as healthcare, finance and supply chain.
Lean Six Sigma finds synergy between these two managerial styles. Lean project management focuses on eliminating eight areas of waste: defects, overproduction, waiting, non-utilized talent, transportation, inventory, motion and extra-processing. Six Sigma, on the other hand, seeks improvements to the quality of process outputs by identifying and removing the cause of errors to minimize the variability in production.
Together, the two styles complement one another by having Lean expose where the problem in a process is emanating from, while Six Sigma is working to reduce that issue. This produces a positive cycle of improvements and continuous flow.
Lean Six Sigma then works together to cut production costs while improving the quality and speed of production, keeping the organization competitive. Six Sigma reduces variations and Lean has its sights on where there is waste and how to reduce it, both of which help save money. The two work well at efficiency, productivity and sound financial control.
Six Sigma and Agile
As agile methods continue to grow from the software development egg in which they were hatched, the style has found itself saddling up with Six Sigma.
The Agile Manifesto states as its 12th principle that “at regular intervals, the team reflects on how to become more effective, then tunes and adjusts its behavior accordingly.” Agile teams are focusing on continuous improvements, which fits hand-in-glove with the creed of Six Sigma.
Agile teams can use Six Sigma to solve problems through empirical data as the methodology provides a set of tools to do exactly that. Rest assured that agile and Six Sigma mix well.
Six Sigma Certifications
Like other methodologies, you can get a Six Sigma certification. It verifies your command of the method of professional skills and is awarded according to a tier of knowledge that follows a belt classification similar to that used in martial arts.
- Certified Master Black Belt (CMBB)
The highest level of Six Sigma certification is the certified master black belt. This person can shape strategy, develop key metrics, act as a consultant and coach those with black and green belts. You must have at least five years of being a Six Sigma black belt.
- Certified Six Sigma Black Belt (CSSBB)
Going down a level brings us to the certified Six Sigma black belt. These are experts in the methodology and are capable of leading or training teams with belts below theirs. For those with this belt, managing Six Sigma projects is their full-time job and they have a full understanding of statistical analysis and process improvement.
- Certified Six Sigma Green Belt (CSSGB)
Those who have a Six Sigma Green belt create, identify and execute processes. They know Lean Six Sigma principles but also DMAIC. They can lead teams on smaller projects and assist those who hold the black belt status. Their focus is on quality improvement, reducing waste and errors while collecting and analyzing data.
- Certified Six Sigma Yellow Belt (CSSYB)
A Six Sigma yellow belt means you understand how to use Six Sigma in the workplace. You’ve started improving processes and creating process maps to outline the steps in a process. You know the principles of information collection. You can’t lead a team but can support a higher belt.
- Certified Six Sigma White Belt (CSSWB)
The Six Sigma white belt focuses on the fundamentals. They understand the roles of those on the team and how these members can improve efficiency. They learn about DMAIC and tend to concentrate on waste reduction.
Criticism of Six Sigma
Not everyone is sold on Six Sigma. Quality expert Joseph M. Juran says that Six Sigma is nothing new. For him, only the terms have changed, but the basic approach to quality improvement remains the same.
The Harvard Business Review notes what it sees as shortcomings of the technique. For one, it doesn’t incorporate information technology. They also feel it’s elitist because it designates people called “black belts” who are experts to analyze and design versus including the whole team.
There’s also an issue with its process of incremental improvements, which some feel stands in the way of radical improvements. It also doesn’t fit well with work that is oriented towards finding innovative new methods and processes.
Since its creation, even a stalwart practitioner such as Jack Welsh has come around to admit that it’s not a holistic approach for everywhere in the company. But in product manufacturing, its ability to reduce defects to one in six standard deviations remains standard and provides results. The decision to apply it to your project is, of course, up to you.
How ProjectManager Helps With Six Sigma
When you get down to it, Six Sigma is simply another way to manage a project. It measures data to find more efficient routes to reach your final deliverable. ProjectManager is award-winning work and project management software that gives you real-time data to make more insightful decisions. It has multiple project views for cross-functional teams to collaborate and keeps everyone on the same page with a single source of truth.
Set Baselines on Gantt Charts
In order to take advantage of that real-time data you have to create a plan. One of our project views, the Gantt chart, is an ideal tool that shows you the entire project on a timeline. You can set dependencies, milestones and a baseline to capture the schedule and cost in order to compare them to your actual effort once executing the project. Now you have real-time data to track everything from resources to workload.
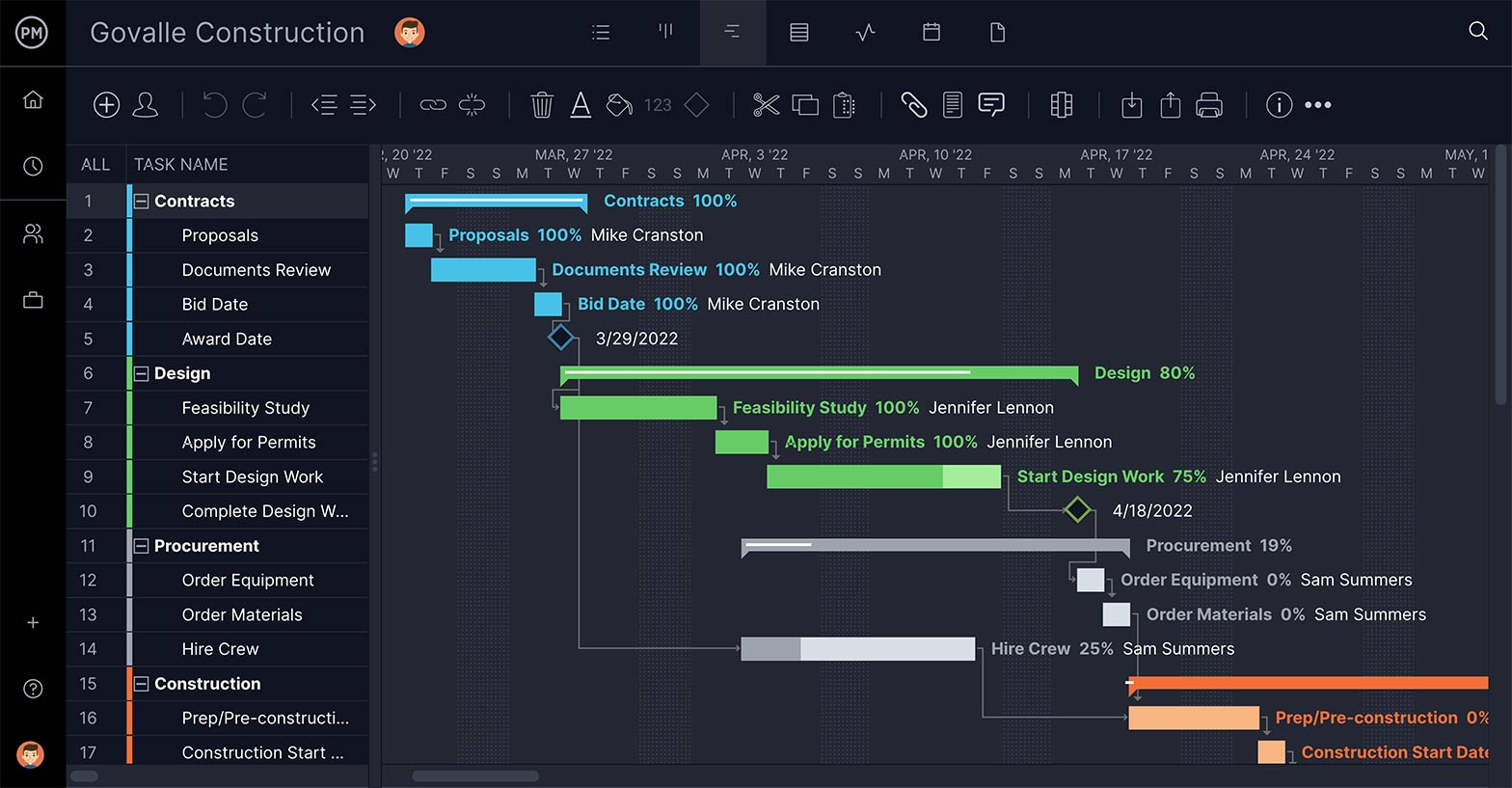
Monitor Six Project Metrics With Real-Time Dashboards
Data runs Six Sigma and once you’ve set the baseline in your Gantt, you can view real-time data across the software. Get a high-level view of the live dashboard and no setup is required. We automate the collection and calculation of data, which is then displayed in colorful charts and graphs that can be read at a glance. See real-time data on the health of your project, tasks, progress, time, cost and workload all in one place.
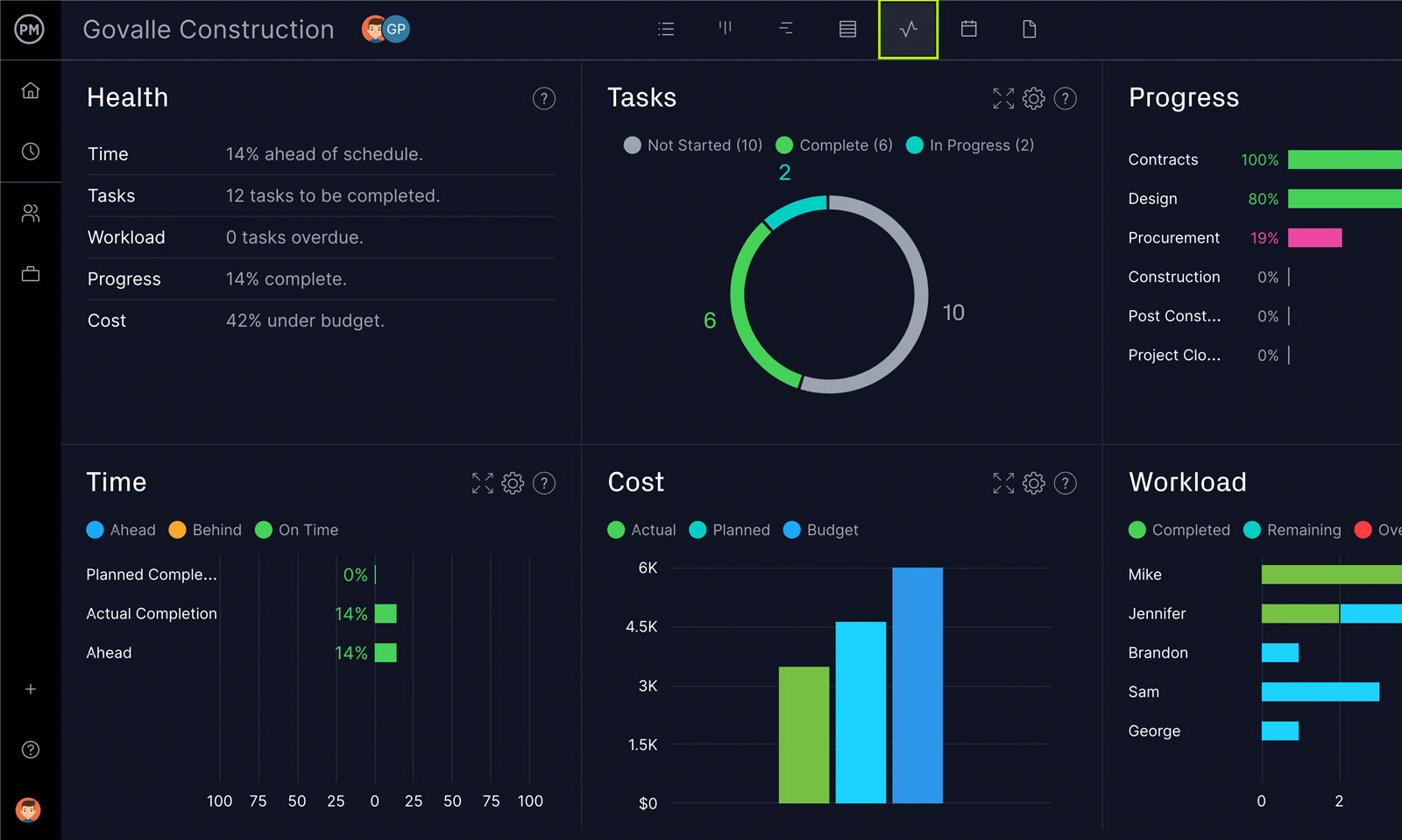
Dive deeper into the data with one-click reports that allow you to filter to see only what you want to see. All our project views track the percentage completed on individual tasks. We offer Six Sigma users a wealth of data to improve the quality of their outputs in a process, using automation to add efficiency and task approvals to maintain quality deliverables throughout the project.
Because of Six Sigma’s use of metrics to measure against a baseline to see where there are issues that can be resolved to make processes more efficient, the need for dynamic project management software is essential. ProjectManager is a cloud-based tool that monitors progress with its real-time dashboard, making it easier to discover issues and quicker to implement solutions to them. Try it free for 30-days, and see for yourself with this trial.