Total Quality Management (TQM) works to maintain success by doing what is necessary to improve customer satisfaction. Of course, that satisfaction is seeded in employees and business processes—long before any product or service reaches its customer.
How does a business or organization make sure that its processes and people are aligned with creating success and customer satisfaction? That’s where total quality management comes in.
What Is Total Quality Management (TQM)?
Total Quality Management is a management approach that focuses on delivering products and services with the highest quality to maximize customer satisfaction and meet regulatory standards. Total quality management is an organization-wide effort for continuous improvement. That improvement can be defined as an employee’s ability to provide on-demand products and services that are of value to their customers, even as their needs change.
That’s the “quality” in total quality management. The “total” indicates that the effort is one that touches every inch of every employee of an organization. As a methodology, however, total quality management has no widely agreed-upon approach. It does, though, draw from other tools and techniques, such as project quality control, quality assurance and testing, and others.
To make sure you’re delivering quality to your customers, you need to be able to monitor the processes you’re using to create the product or service you’re making for them. ProjectManager is online work and project management software that tracks real-time data with its live dashboards, which monitor six project metrics automatically. There’s no setup. It’s ready when you are. Get started with ProjectManager for free today.
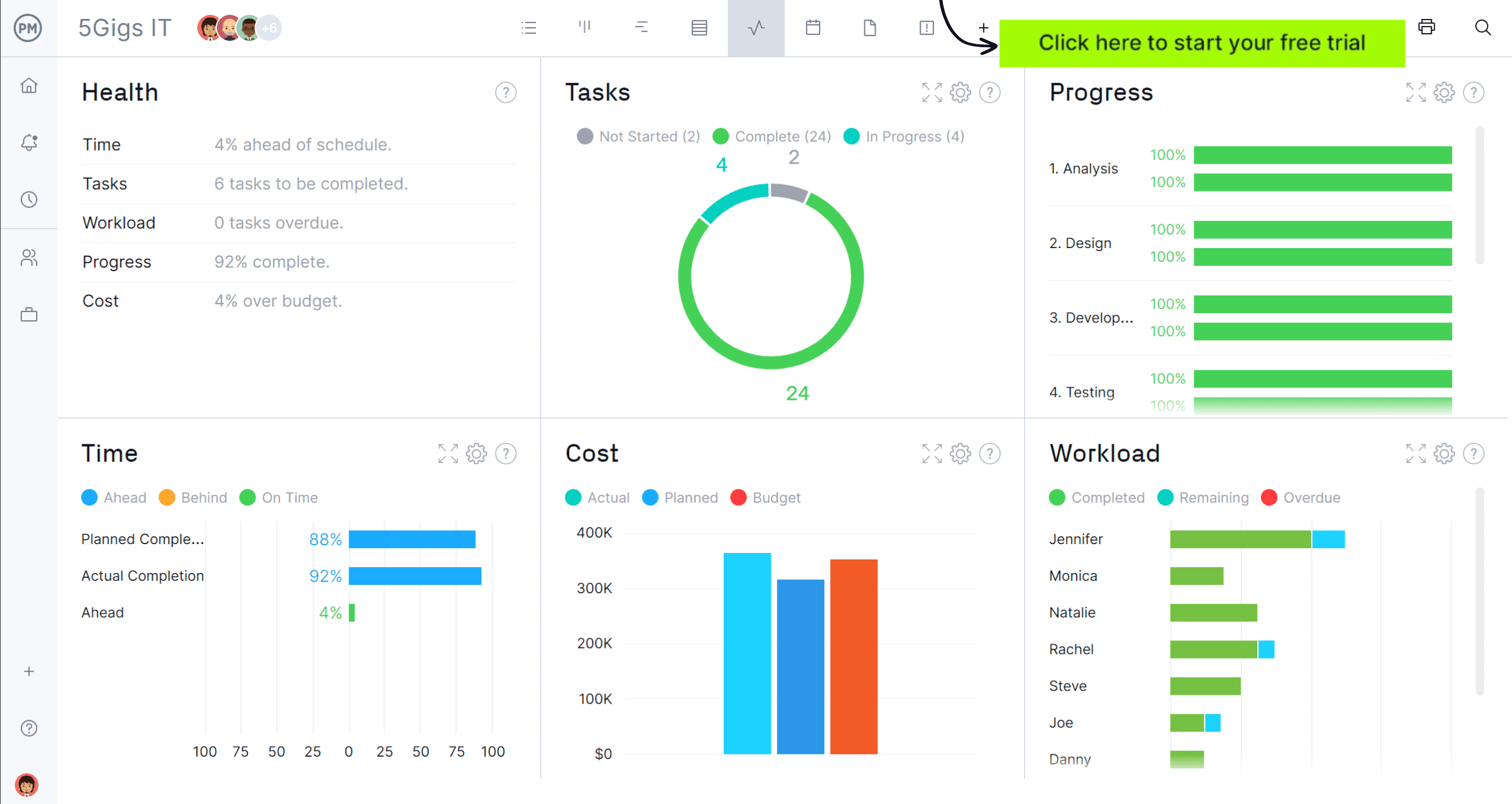
Why Is Total Quality Management Important?
Total quality management is important for several reasons. First, it fosters a culture of continuous improvement and customer satisfaction, leading to higher-quality products and services. When customers are satisfied, they’re more likely to be loyal and can help spread positive messages about your company.
It also streamlines processes and eliminates waste, helping to reduce errors and increase productivity. Not only does this translate into cost savings, but it also contributes to the idea that preventing problems is usually less expensive than fixing them.
Finally, TQM helps organizations gain a competitive advantage in the marketplace. They can deliver high-quality products and services and are better positioned to attract and retain customers.
Total Quality Management Principles
Just as the definitions of total quality management (TQM) differ, so do its principles. However, we’ve gathered the most important TQM principles for you below.
- Customer Focused: The definition of quality lies with the customer, and all efforts to achieve success in the organization lead to customer satisfaction.
- Total Employee Involvement: The effort is not isolated to one department of an organization. To be successful in its objective of customer satisfaction, there must be a common goal for all aspects of business and for each employee.
- Process Oriented: Process thinking is fundamental to total quality management; the internal steps a company takes directly result in the external output delivered to the customers.
- Integrated System: Basically, regardless of the size or complexity of the organization, all its distinct parts must work together.
- Strategic and Systemic Approach: Using strategic planning to create a strategic plan that integrates quality as a core component of the company is a way to structure total quality management into an organization’s mission.
- Continual Improvement: The mantra for total quality improvement is customer satisfaction, but that is not a one-shot goal: the act of improving quality for the customer is a process without an end.
- Fact-Based Decision Making: In order to know if an organization is meeting its objectives, there must be data on performance, and those metrics must be collected and analyzed with accuracy and without prejudice. (For more on this, learn how to use data to be a better manager.)
- Communications: It’s impossible to maintain a successful TQM approach without an effective communication plan. Communication plans make sure that every department is aware of what they and others are responsible for, so they can coordinate operations to achieve their common goal.

Get your free
Quality Control Template
Use this free Quality Control Template for Excel to manage your projects better.
Total Quality Management Methodologies
Being able to deliver total quality management requires methodology. There isn’t just one way to manage quality in your project. There are several approaches you can take. A few of them are listed below.
Lean Manufacturing
Lean manufacturing is a type of lean projection that comes from Japan, specifically, the car manufacturer Toyota. It’s all about targeting and eliminating what it calls muda or waste, in order to add value and maintain quality.
Six Sigma
Six Sigma is another quality management methodology that is directed towards improving current processes, products or services. It does this by finding and removing any defects in order to streamline quality control.
ISO 9000
ISO 9000 is a set of international standards focused on quality management and quality assurance. It was created to help companies document quality system elements that they needed to maintain an efficient quality system.
How to Implement Total Quality Management in 4 Steps
Getting started with total quality management requires that the top management learns about the methodology, and then commits to it as one of the organization’s strategies. The organization writ large must then assess its customer satisfaction and quality management systems.
One of the easiest methods to implement TQM is called PDCA. PDCA stands for Plan, Do, Check and Act. It’s a four-step management method to control the continuous improvement of processes and products.
1. Plan
Planning includes identifying and understanding the problem or opportunity as it relates to TQM. From the information you’ve gathered, come up with ideas and develop the best into an implementation plan.
2. Do
With a planned solution, you can now test it and build a pilot program to see if you achieve the quality improvements you expected. Document the results.
3. Check
Here you’ll analyze the results of your pilot program against what you expected to achieve. If you’ve met those criteria move on to the next step. However, if you’ve fallen short, then you need to return to step one.
4. Adjust
Once you’ve tested and are satisfied with the solution, you can implement it at full scale. This process is a loop, however, with no beginning or end. The success is only the new baseline of which you’ll again test to improve.
The need for active management participation is critical to the success of any total quality management plan. This is done by creating steering committees to make sure everyone is working together to improve quality.
There is also the formation of ad hoc cross-functional teams that are responsible for addressing the immediate process issues. There are also standing cross-functional teams that have similar responsibilities, only those are over the long term.
Total Quality Management Systems & Tools
When it comes to analyzing quality-related issues, the U.S. Navy employed the seven basic tools of quality. This is a fixed set of graphical techniques identified as being most helpful in troubleshooting quality-related issues. These tools are often used in Six Sigma as well.
The seven tools for TQM are:
- Check sheet used to collect data in real time
- Control chart to determine if a process is in a state of control
- Stratification (or flow or run) chart to sample a group
- Pareto chart, which is both a bar and line graph that assess the most frequently occurring defects by category
- Histogram to roughly assess the probability distribution of a given variable by depicting the frequencies of observations occurring in certain ranges of value
- Cause-and-effect diagram
- Scatter diagram to display the value for two in a set of data
How to Get Your Team to Buy Into Total Quality Management
To get your team excited about total quality management, it’s ideal to take a strategic and consistent approach. Rather than solely implementing a set of procedures, aim to foster an underlying culture shift in the organization. For example, senior management needs to lead by example and embrace TQM principles. Actions speak louder than words, so participating in training and recognizing quality efforts can go a long way in getting team buy-in.
Education on TQM principles, tools and techniques is another important aspect. Customize training to address the specific needs and roles of team members and offer continuous learning opportunities to reinforce key concepts.
History of Total Quality Management
The roots of total quality management can be traced back to the economic instability of the late 1970s and into the early 1980s. It was at this time that the dominance of North America and Western Europe was challenged by competition from the East, specifically Japan’s skill at making high-quality inexpensive products.
While the origin of the term is not clear, many think it was inspired by the book Total Quality Control by quality control expert and businessman Armand V. Feigenbaum and What Is Total Quality Country? The Japanese Way by the organizational theorist Kaoru Ishikawa.
The Role of the U.S. Navy
It was the United States Navy that promoted the idea in 1984 when it asked its civilian researchers to offer recommendations on improving its operational effectiveness. The recommendation was to use the teachings of engineer and statistician W. Edwards Deming, which the U.S. Navy called total quality management in 1985.
The methodology was employed by the U.S. Environmental Protection Agency’s underground storage tanks program in 1985. The private section soon followed as a way to remain competitive against the growing influence of the Japanese.
Key Concepts in Total Quality Management
The key concepts of total quality management developed by the U.S. Navy include:
- Quality is defined by what the customers’ requirements are
- Top-tier management is directly responsible for the improvement in quality
- It is by systemic analysis and using that data to improve work processes, that an increase in quality occurs
- The improvement of quality is a continuous effort and is conducted throughout the entire organization
The U.S. Navy employed certain techniques and tools to achieve those concepts. For example, there’s the Plan Do Check Act or PDCA cycle, which is a four-step management method to control the continuous improvement of processes and products.
Related: How to Implement Business Process Improvement
Quality Control Template
This quality control template is ideal to document any issues that are found when evaluating the quality of your products or project deliverables. It allows you to describe the quality management issue, who’s responsible for fixing it, its status and the expected date of completion.

Free Templates to Help with TQM
Total quality management is best achieved through the use of project management software, which streamlines processes and helps you capture issues fast and resolve them. However, if you’re not using software or are not ready to upgrade to software, ProjectManager has dozens of free project management templates that can help you maintain the quality your customers expect. Here are a few.
Project Dashboard Template
Being able to monitor and track activities in your project is how you make sure you’re meeting your quality expectations. While our real-time dashboard will capture live data, the free project dashboard template for Excel is the next best thing. You have to input the data but then you get the charts and graphs you need to see how your project is performing.
Gap Analysis Template
In order to improve the quality of your product or service, you need to know where you are and where you want to be in the future. This is what a free gap analysis template for Excel can do for you. It captures the current and future stats and then shows the gap percentage you have to close, plus the actions and resources you’ll need to do it.
Issue Tracking Template
When you find issues that are negatively impacting the quality of your project or service our free issue tracking template for Excel can help you monitor your progress in resolving it. The free template has space for you to describe the issue and its impact, add a priority, date and owner and track its status.
Use ProjectManager for Total Quality Management
ProjectManager is cloud-based work and project management software that delivers real-time data to help you make more insightful decisions when monitoring the quality of your work. Then you have features to plan, track and report on your quality management to implement total quality management.
Control Quality With Task Automation
One way to make sure you deliver quality is by removing as much human error as possible. Our workflow automation allows you to create custom workflows that trigger actions to change status, priority, assignee and much more. You can also add task approval settings so only those authorized to close a task can do so, further ensuring you deliver to your quality expectations.
Plan TQM With Interactive Gantt charts
Once you have a total quality management plan, you need to organize all the tasks and get your team assigned. Our online Gantt chart allows you to link task dependencies to avoid delays, set milestones to help with tracking and even filter for the critical path. Then set a baseline so you can measure project variance between what you planned and where you actually are in the schedule to stay on track.
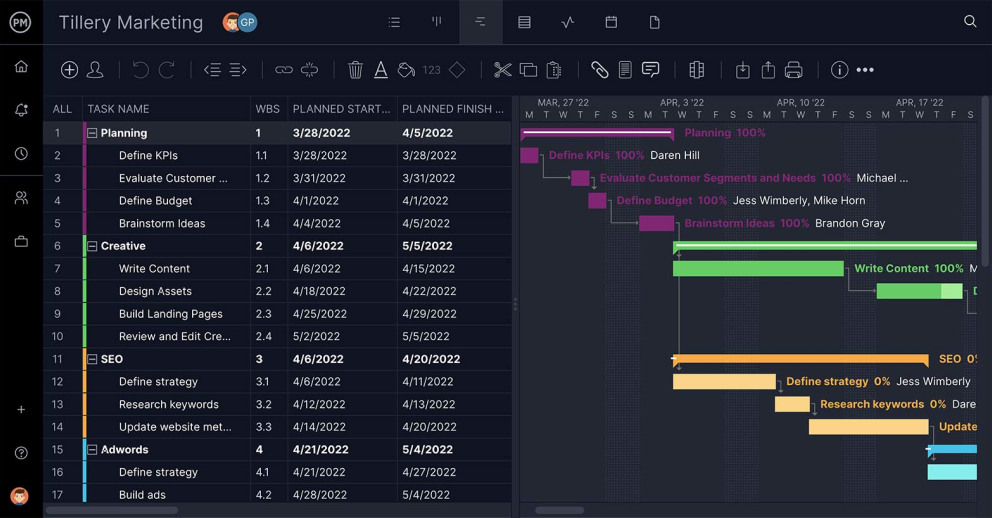
Track Progress and More With One-Click Reports
To help you make sure you’re meeting deadlines and not overspending on your QTM plan, we have everything from status reports to reports on workload, time, cost and more. Generate them with a keystroke, and each report can be filtered to show only the data you want to see. They can also be easily shared to help keep stakeholders updated.
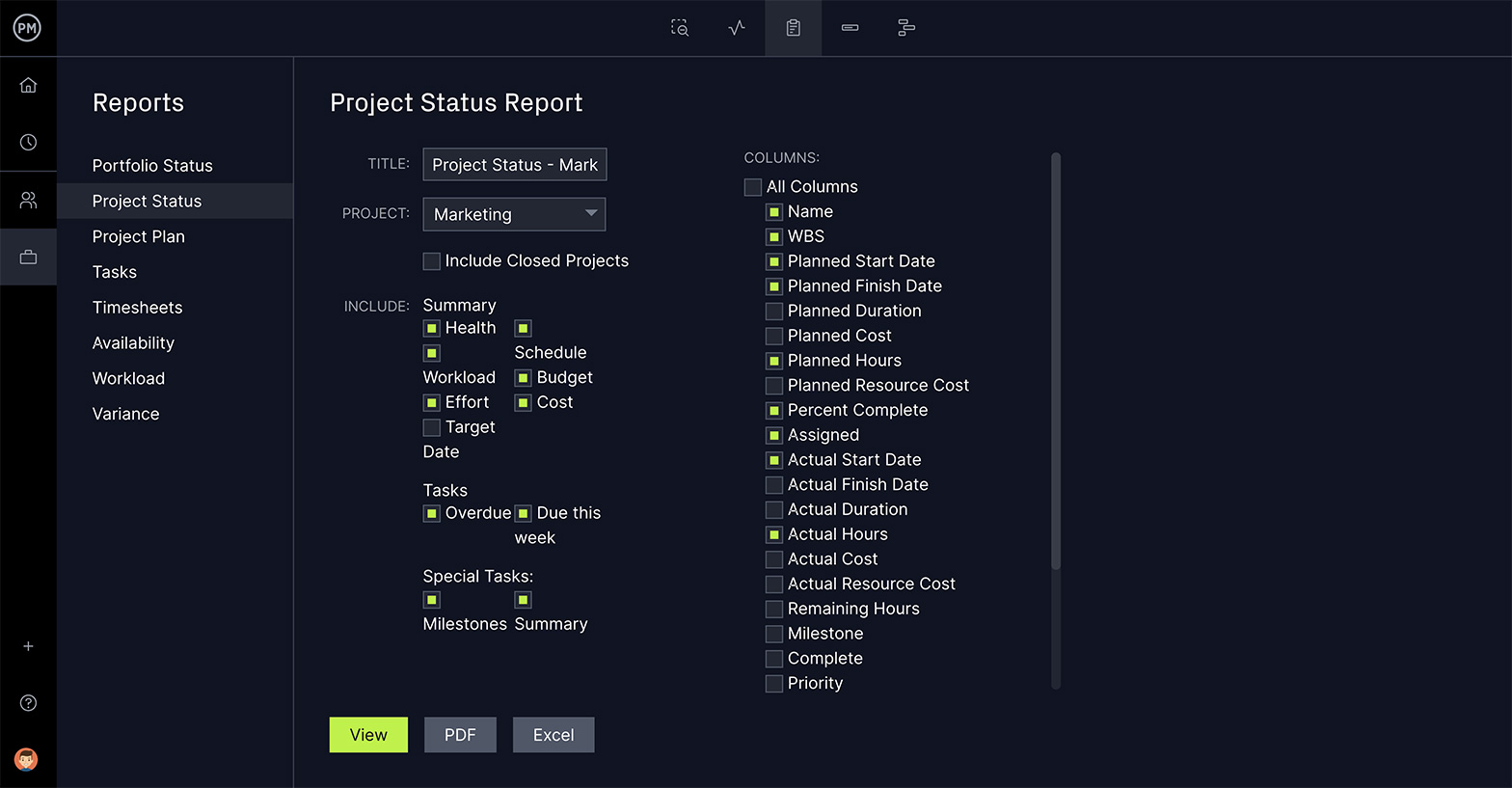
Our multiple project views allow your team to work how they want, on kanban boards, task lists and more. All data is updated together across the tool so you have a single source of truth to keep everyone working on the same page. Our collaborative platform allows team members to share files, comment and get notified of any updates to let them work more productively—all of which leads to more quality work.
As the name says, total quality management is a systemic change to the strategic goals of an organization. It impacts everyone and every department. Therefore, having the right tools to manage and communicate this process throughout an organization is critical. ProjectManager is a cloud-based project management software that gives managers and teams the control to plan, track and report on the progress of this or any methodology. See for yourself by taking this free 30-day trial.