Businesses are always looking for ways to improve their practices. But is it possible to structure a process of continuous improvement at your company so that it aligns with your preferred management tools, team morale and overall objectives?
In other words, can that process of continuous improvement prove productive and worthwhile? Yes. There are many methods that have been developed to successfully seek out and act on opportunities to help improve your business and quash the competition.
When it comes to streamlining work and reducing waste in an organization, the continuous improvement business strategy is lauded for its effectiveness. But what is it and how can it be applied to your business? Good questions. Let’s take a look.
What Is Continuous Improvement?
Continuous improvement business strategy is also known as a continual or continuous improvement process. It’s an ongoing process to improve the products, services or processes of an organization. The improvements sought are incremental over time rather than achieved with a breakthrough moment.
Project management software can help you plan for continuous improvement in your projects. ProjectManager is award-winning project management software that has robust Gantt charts that organize tasks, link dependencies and can set a baseline to track project variance in real time. You can also filter for the critical path to identify essential tasks to improve your processes. Get started with ProjectManager today for free.
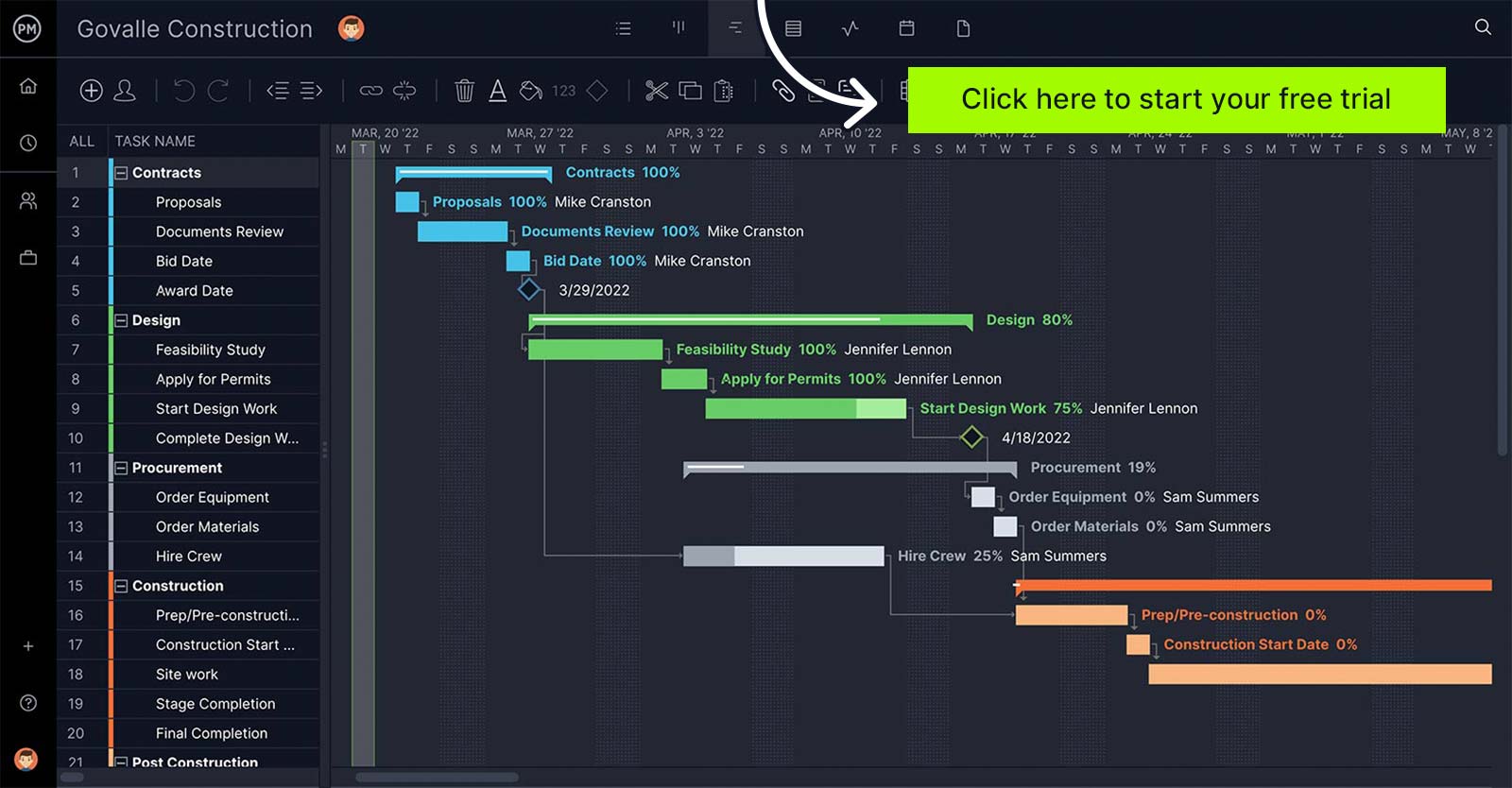
The delivery of those processes is in constant evaluation and change, so further improvements can be developed and applied. The ruler to measure these changes is the efficiency, effectiveness and flexibility of these processes.
Some see continuous improvement as a meta-process, such as W. Edwards Deming, an early proponent, who saw it as part of a larger system of organizational goals. But a bigger definition considers continuous improvement as a gradual and never-ending process that tries to increase effectiveness and efficiency to fulfill a company’s objectives.
The Continuous Improvement Process
The continuous improvement process is sometimes referred to as the PDCA cycle. That’s the initials for each of the four steps in that process: plan, do, check and act. Let’s take a look at each of those stages and how they work.
Plan
To begin, brainstorm with your team and identify areas for improvement. Then, from these sessions, build an action plan to implement the ideas that were developed to improve on the opportunities you identified.
Do
This is the stage where you implement that plan. It’s best to make the change on a small scale so that you can measure its effectiveness before going all in.
Check
Monitor and test the results of the plan to prove that it is in fact improving whatever was targeted for improvement.
Act
With the data collected in the last step, you can now make a decision as to whether to implement the change full-scale or abandon it and try again.
Continuous Improvement History
While the title of inventor might be harder to pin on a specific person, W. Edwards Deming is considered one of the pioneers of continuous improvement methodology.
Some even refer to continuous improvement methodology as the Deming Cycle, though he credits Walter A. Shewhart, an American physicist, engineer and statistician, for the idea.
Deming went to Japan after World War II as part of an American initiative that sought to help Japanese manufacturers rebuild their factories and improve their efficiency. His work would inspire methodologies such as just-in-time manufacturing (JIT), lean manufacturing and kaizen.
Continuous Improvement Methodologies
The idea of evaluating a process to come up with a plan to improve it has been applied in many ways. There are many types of continuous improvement methodologies. Here are just a few.
Continuous Improvement and Kanban Project Management
Kanban boards, the visual workflow tool, is a great fit for continuous improvement. It is by design evolutionary, encourages an experimental approach and fosters team collaboration. Kanban provides visibility, metrics and the focus necessary for continuous improvement. You can identify problems on the board and then plan to resolve them.
Continuous Improvement and Lean Manufacturing
Lean manufacturing focuses on identifying value, value stream mapping, creating flow, establishing pull and continuous improvement. It uses just-in-time production to ensure that you have what you need when you need it without having extra materials in your inventory that will cost extra to the warehouse.
Continuous Improvement and Six Sigma
Six Sigma is a process improvement methodology that minimizes the amount of variations in an end product. It uses statistical data to benchmark the process, which is considered optimized if it produces less than 3.4 defects per one million cycles. This reduces defects but also inconsistencies.
Benefits of Continuous Improvement
The idea of continuous improvement is to gain benefits that will make a company more profitable or competitive in the marketplace. But it’s also instrumental in improving product quality. It’s given that continuous improvement will lead to an increase in efficiency and productivity.
That in turn creates decreased costs and reduced waste. Not only will companies discover that their customers are more satisfied, but the teamwork employed by workers will add to their satisfaction and retainment.
Continuous Improvement vs. Kaizen
Some use “kaizen” as a synonym for continuous improvement. Kaizen is a compound word made up of two Japanese works, kai meaning change and zen meaning good. As a method, it can be traced back to the book by Japanese organizational theorist and management consultant Masaaki Imai, Kaizen: The Key to Japan’s Competitive Success.
Imai wrote on three main points of kaizen:
- Feedback: A core principle of the process that involves self-reflection.
- Efficiency: Identify, reduce or eliminate anything that gets in the way of the process.
- Evolution: Kaizen depends on incremental, continuous development instead of a great leap forward.
There are several other key features of kaizen as defined by Imai. He believes improvements should be based on building from many small changes as opposed to major changes. Also, if those changes and ideas are coming from the bottom and rising to the top, as in, from the workers, then those ideas are more aligned with the objectives of the organization and can be implemented easier.
Furthermore, Imai believes that ideas from the people working on the frontlines of the company’s efforts are more attuned to how to improve processes than an outside consultant. Consequently, employees should always be looking for ways to improve performance.
Imai suggests that making workers take ownership of their efforts will improve their ability to offer realistic ideas to improve the overall business. Strategically, he believes in figuring out how to increase the effective delivery for the customer and how flexibility helps achieve that goal.
The Principles of Continuous Improvement
While the principles are outlined in Imai’s book, they’re worth repeating.
- Incremental change: Not a paradigm shift or invention, but slow and steady progress is the most innovative. It helps apply change more easily, as well as giving the reins to the organization rather than having to respond to external forces.
- Employees provide ideas: Rather than management, the ideas for change should come from the workers, who are closest to whatever problems the organization might be experiencing and have the knowledge to resolve them.
- Incremental change is cheap: Small changes are likely not as costly and won’t impact the budget severely. The emphasis is on eliminating, not adding to the process, which is less expensive.
- Workers take ownership and accountability: By giving employees ownership of the process, they’re more invested and motivated.
- Improvement is reflective: The strategy of continuous improvement only works if there’s dialogue, feedback and open communication between workers and management.
- Improvements can be measured and repeated: Once a change is made, it’s not left alone but monitored and measured, so determinations can be made as to its effectiveness. Therefore, if that change does work, it can be repeated or applied to other aspects of the organization.
Benefits of Using a Continuous Improvement Business Strategy
The overall benefit is in the name, continuous improvement. That’s a no-brainer. But it’s never good to take a concept at its word. What are the details, and how can it improve the business?
For one, it streamlines workflows. By constantly looking for ways to improve things, what happens is a reduction in operating overhead. That’s a good thing. It saves time and money.
It can also reduce the cost of projects and help to prevent overages. When constantly seeking improvement and evaluating processes, a greater knowledge of the overall costs of completing a project comes into sharper focus. If you can determine whether a project’s constraints are likely to break, you can plan better to avoid those mishaps.
Then there’s the flexibility inherent in the strategy. If you’re always on the lookout for ways to improve, you’re flexible. You’re changing to take advantage of opportunities. This constant movement, if it’s tethered to a well-thought-out process, will reduce complacency and threats from the competition.
When Should You Implement the Continuous Improvement Model?
If you’re looking to save time and cost but keep up the quality of the product, then a continuous improvement business strategy is a good way to manage that difficult balancing act. By looking for opportunities to improve business and then evaluating those changes, an effective strategy is formed.
Some organizations aren’t set up to have their teams constantly practicing continuous improvement, but that doesn’t mean that they can’t take advantage of this useful strategy. For example, companies can schedule regular meetings to discuss ways to improve processes. These can be one-day events or last a week to dive deeper into ideas.
Whether you choose to adopt these techniques at every level of the operation of your business, or you simply make continuous improvement business strategy one more tool in your toolbox, there are still opportunities to reduce inefficiencies and cut waste.
Using ProjectManager for Continuous Improvement
ProjectManager, award-winning project management software, gives you all the tools you need to implement continuous improvement strategies. First of all, our software enables collaboration from everyone in the organization from the top down. This empowers workers to generate ideas on how to eliminate waste, and formally document them as a task to be addressed. From there, they can add comments and files as evidence, creating a culture of action around that task.
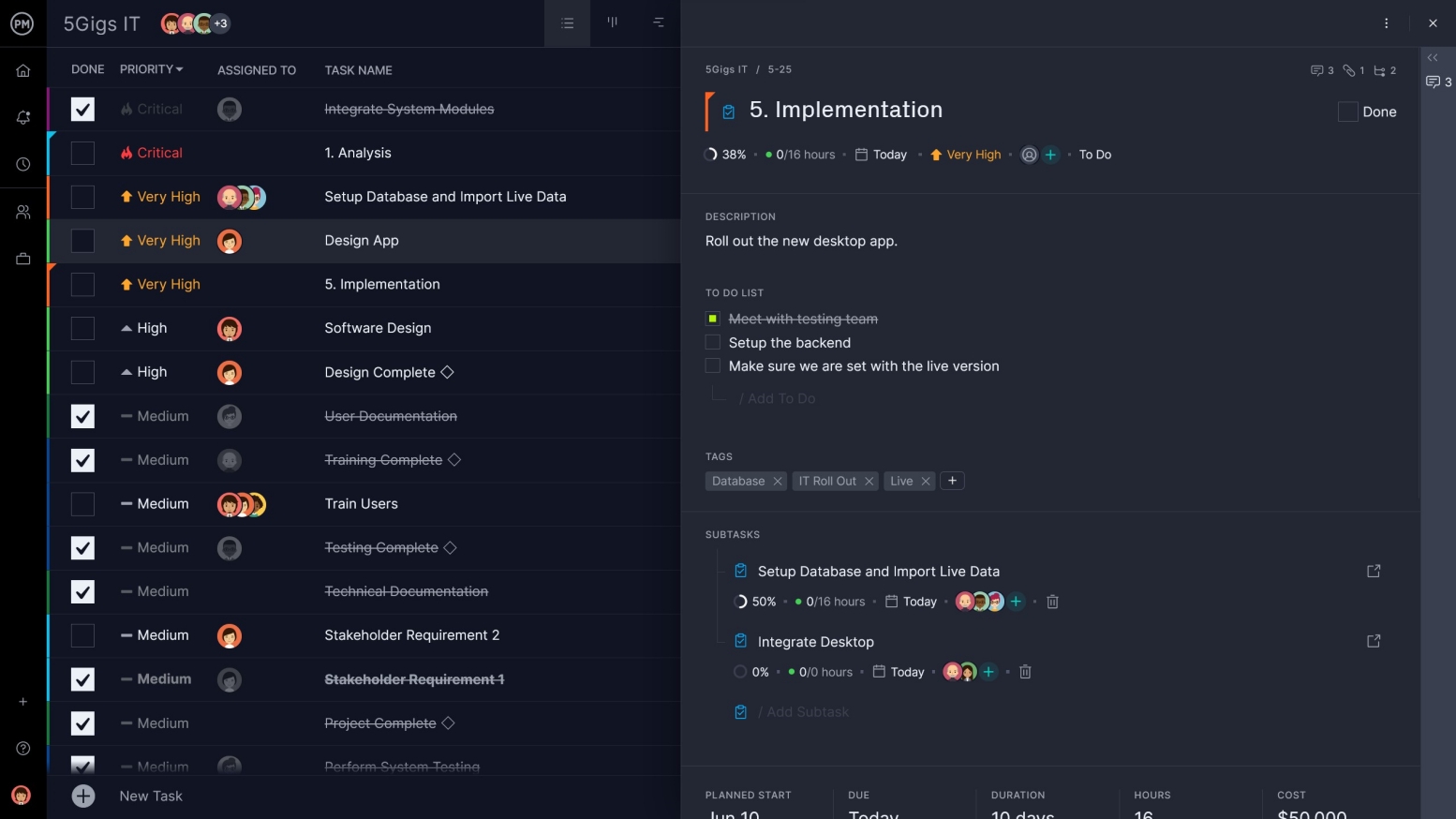
As more and more of these improvement tasks are recognized, they should be added to a formal plan. Use our online Gantt charts to create a long-term plan to implement positive, incremental changes across the organization. You can put each task in a phase, so you can focus on changing discrete chunks of the organization at a time. You can also assign these tasks to team members, creating a culture of accountability to ensure that change is being addressed.
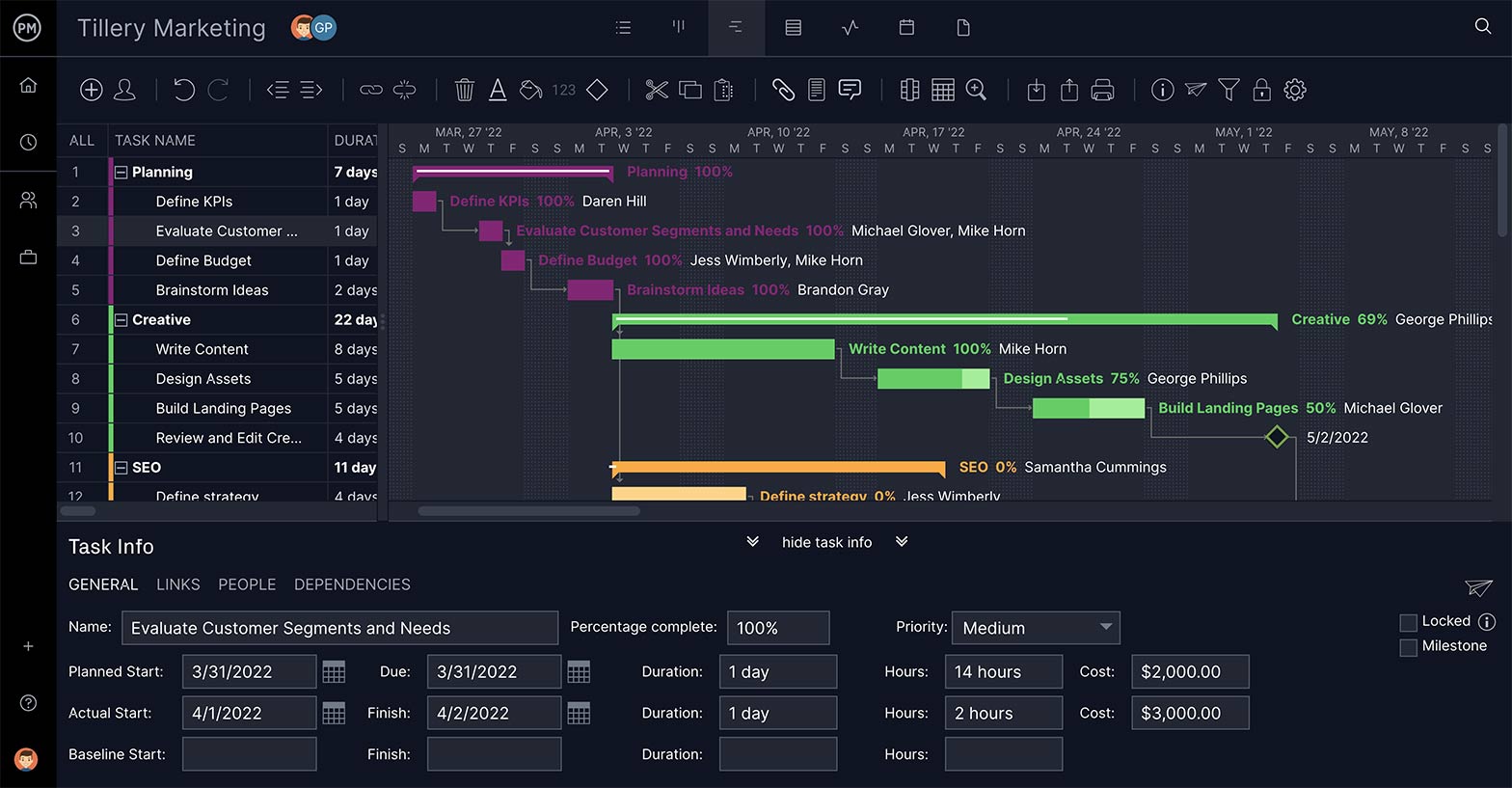
If you’re thinking of working with a strategy of continuous improvement, then you’ll want a tool that can facilitate that process. ProjectManager is online software that offers a real-time platform for teams to collaborate. Plus, there are tools to monitor and report on the progress of the changes you apply to your processes. Try it today and see with this free 30-day trial.