Manufacturers, as in all businesses, are constantly seeking efficiencies that reduce costs while maintaining the production of quality goods. This is, of course, easier said than done. However, manufacturers have methods, such as production efficiency, to help achieve these goals.
What is production efficiency and how does an organization calculate it? Those are just two of the questions answered below. Once a manufacturer understands what production efficiency is and how to calculate it, then they need to try and improve it. We’ll go over some ways to improve production efficiency.
What Is Production Efficiency?
Production efficiency is used to identify the conditions in which goods can be manufactured at the lowest possible unit cost. Also known as productive efficiency, it works at using resources wisely and reducing waste. When done successfully, production efficiency creates higher revenues for the manufacturer.
Manufacturers will also seek production efficiency when they can’t produce more goods without sacrificing the production of another related product. Production efficiency doesn’t merely measure productivity levels, it also considers the amount of resources that are needed for production. This provides manufacturers with a balance between reducing costs and increasing resource efficiency without compromising on the quality of products.
Project management software can help with production efficiency. ProjectManager is award-winning project and portfolio management software that can help manufacturers achieve production efficiency with detailed production schedules. Robust Gantt charts can plot every stage of production, controlling costs and resources to get the most out of them without negatively impacting quality. Get started with ProjectManager today for free.
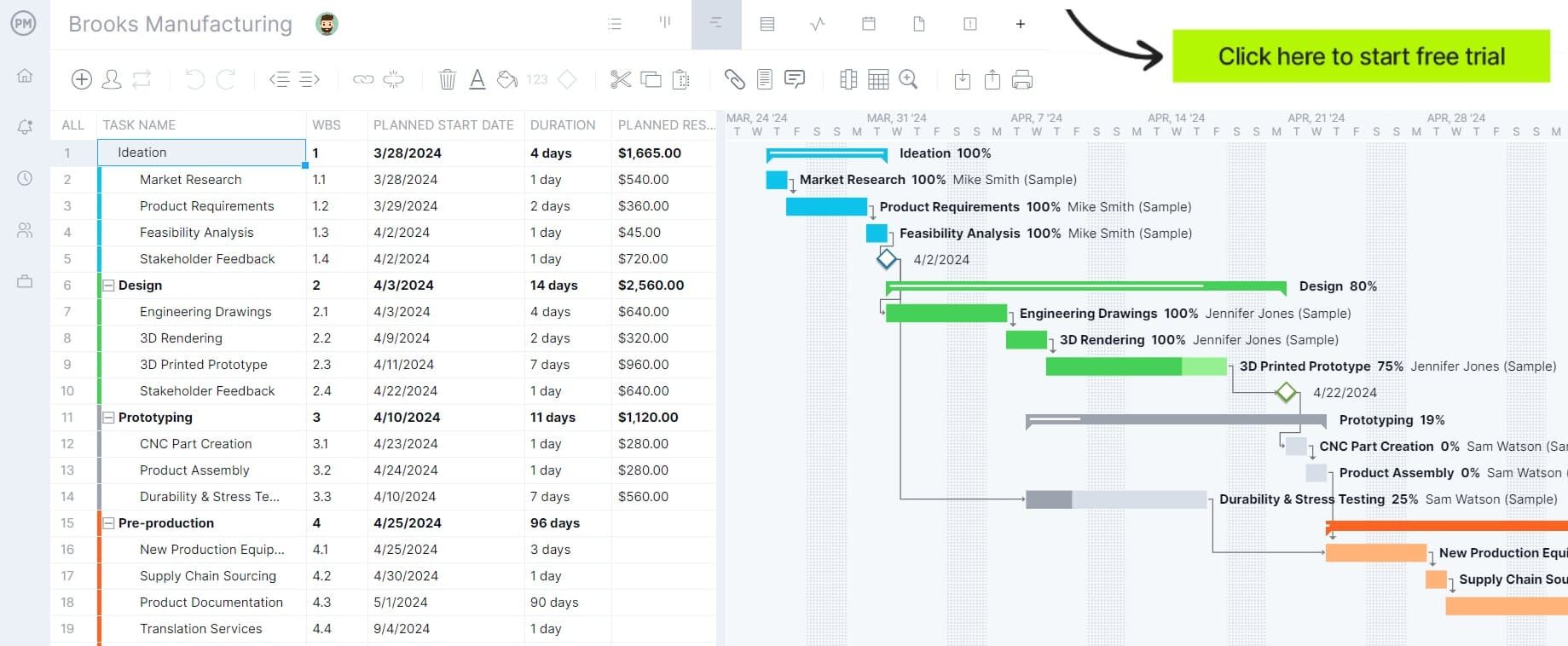
Calculating the Production Efficiency of an Organization
Production efficiency is the ratio between the current production rate of a manufacturing process and the standard output, which is the total units that can be made if an organization uses its production capacity to its fullest extent. Ideally, the production output should be equal to the standard output to reach maximum production efficiency. To achieve this, you can follow these four steps.
1. Set up a System to Track Production Output
The first step before any monitoring of production output can begin is defining what output means for the business. Once that has been determined, then a system needs to be in place to track the production output. The data collection system should be accurate, reliable and consistent.
2. Establish the Standard Output Rate
The standard output rate is the rate of maximum performance or the maximum volume of work produced per unit of time. This value can be measured using historical data or through a time study process. Choose the timeframe to measure, such as hours, days, weeks or any relevant unit. The formula to establish the standard output rate is:
Production Rate = Total Output / Time
3. Measure the Actual Output Rate
The actual output is the current rather than the potential level of production. To measure the actual output rate, divide actual production costs by actual output.
4. Use the Production Efficiency Formula
With this information now at hand, the production efficiency can be calculated. The formula for production efficiency is:
Production Efficiency = (actual output rate / standard output rate) x 100
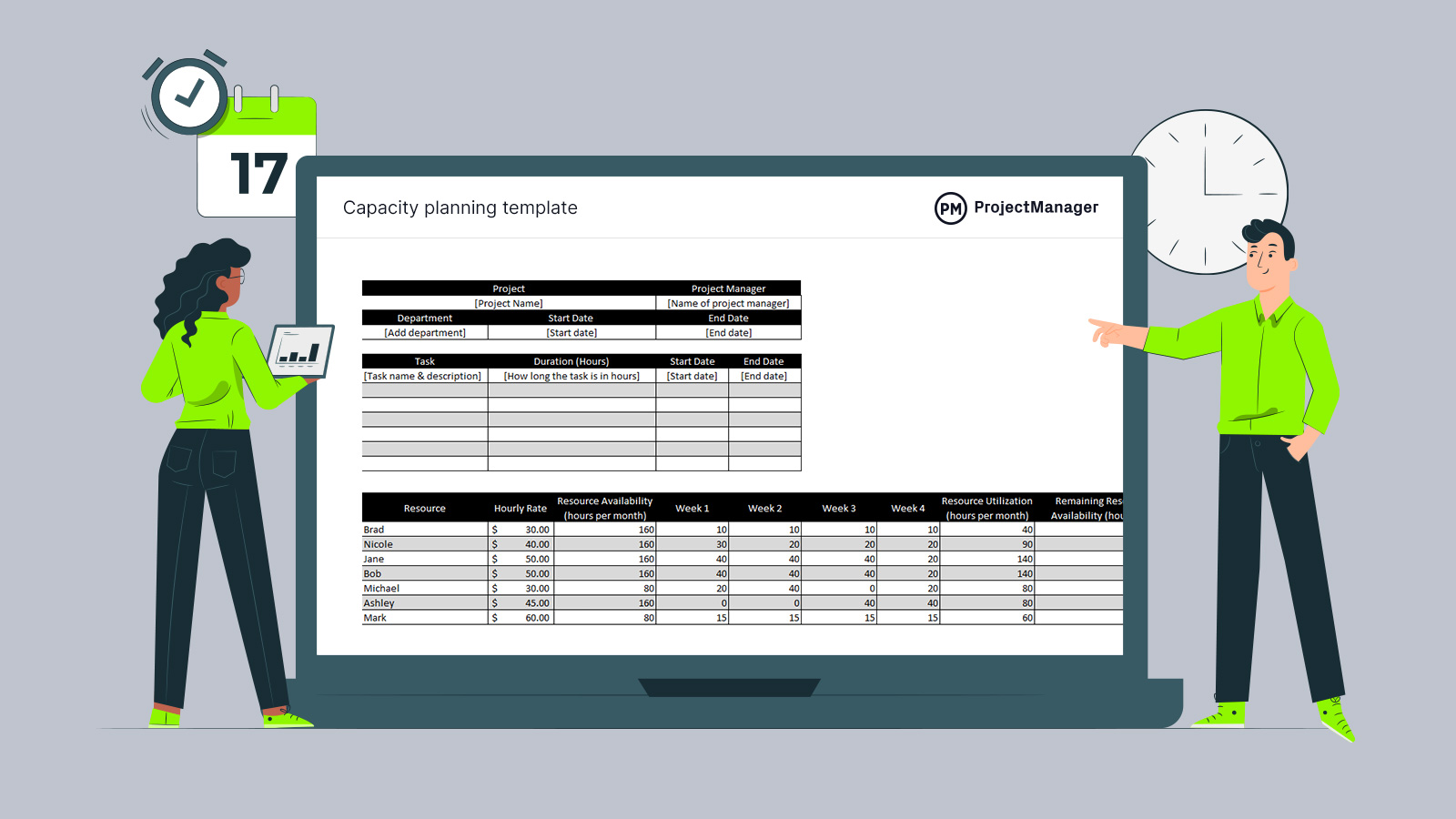
Get your free
Capacity Planning Template
Use this free Capacity Planning Template for Excel to manage your projects better.
Production Efficiency Example
Formulas are abstract. To have a more concrete idea of production efficiency, a real-life example will help. Acme Manufacturing produces 24 widgets over an eight-hour day production schedule. That means its actual output rate is three widgets per hour.
Acme Manufacturing when producing at maximum capacity can up its production to 16 widgets over an eight-hour work day. Therefore, the standard output rate is two widgets per hour.
Applying the production efficiency formula to this scenario, the average output rate is three widgets per hour and the standard output rate is two widgets per hour, production efficiency for Acme Manufacturing is 150 percent. This is a high level of efficiency.
How to Improve Production Efficiency
Not every business will have such a high efficiency when calculating their production efficiency. Let’s look at some of the ways to improve production efficiency.
1. Track Key Performance Indicators (KPIs)
Tracking productivity manufacturing KPIs will provide valuable insights into how well production is performing and identify areas for improvement. Some of those KPIs are as follows.
- Cycle Time: The average amount of time it takes to process raw materials into a completed product.
- Throughput Rate: The amount of product that can be produced and delivered to a client within a specific time period.
- Production Capacity Rate: The maximum output of manufactured goods and materials that a business can produce.
- Machine Uptime Rate: Quantifies the duration during which a machine is actively operational in comparison to its scheduled operational time.
2. Streamline the Shop Floor Operations
The better the layout of the shop floor, the better a manufacturer’s production efficiency. Shop floor planning and control is the process of using methods and tools to track, schedule and report the status of work-in-progress (WIP) manufacturing from the floor level. Here are some more ways to take advantage of shop floor operations.
- Facility Layout: Also called plant layout, is the operational plan used to arrange workers, equipment and machines that increase efficiencies in the production process.
- Optimize Production Routing: The process of determining the most cost-efficient route when manufacturing a product.
- Assembly Line Balancing: The arrangement of the individual processing and assembly tasks at the workstations so that the total time required at each workstation is approximately the same.
- Standard Operating Procedures: A standard operating procedure is a document with step-by-step work instructions that guide operators through their tasks and standardize them to deliver greater efficiency.
3. Plan and Schedule Maintenance Activities
Another way to improve production efficiency is by ensuring that maintenance is executed regularly so it’s the least disruptive to the production process. This is done by careful planning that ensures machines are kept in top condition at all times. It also helps to avoid costly breakdowns and repairs by preventing problems before they interrupt production.
4. Manage the Organization’s Inventories
Another aspect of manufacturing to control in order to gain production efficiency is inventory. The greater control and insight over inventory movement, the shorter production and customer lead times. This also leads to more precise quotes and increased customer satisfaction. Here are some areas to manage inventory more efficiently.
- Production Inventory: The raw materials that are used in the manufacturing process.
- Work-In-Progress Inventory: The products that are currently at some phase of the manufacturing process in an unfinished state.
- Finished Goods Inventory: The final assembled products that are ready for sale.
Capacity Planning Template
Capacity planning is an essential part of improving production efficiency. The process of figuring out how much production capacity is needed to meet the demand that customers have for a product is difficult to determine as it’s always fluctuating.
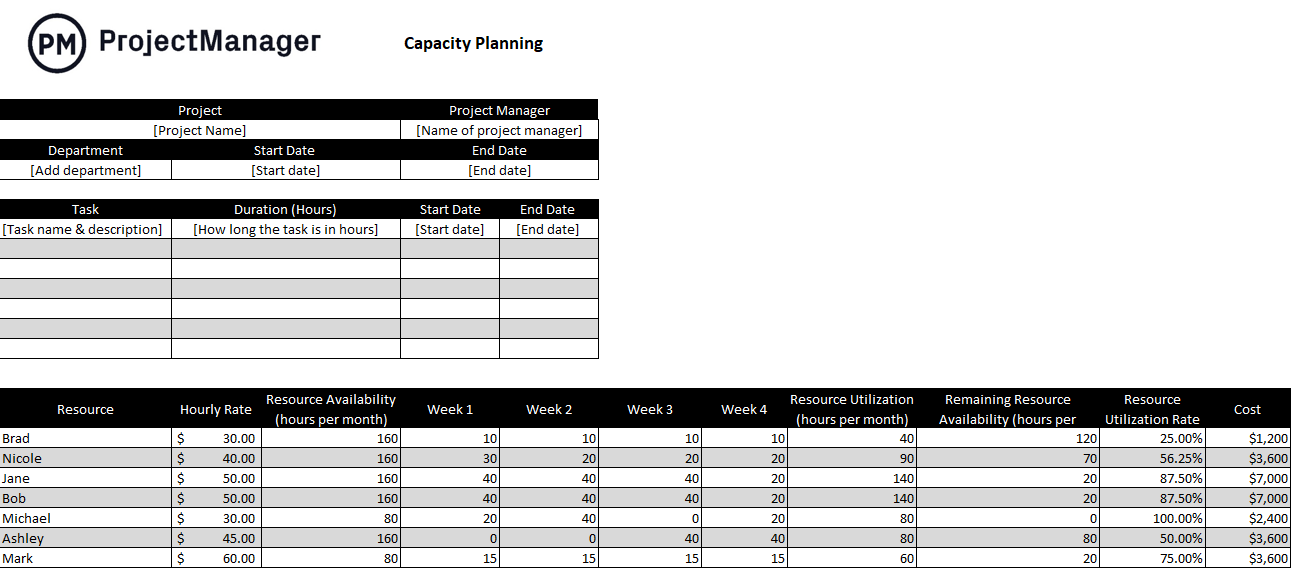
Download this free capacity planning template for Excel and get visibility into the utilization, time and effort used for each team member to do their task. This will help to reduce stock-outs, identify inefficiencies in the manufacturing processes and increase delivery capacity.
Production Management Templates
Many more free templates can assist manufacturers as they seek to improve their production efficiency. Below are a few free templates out of the over 100 downloadable project management templates for Excel and Word to help various industries with every phase of their projects.
Production Schedule Template
A production schedule helps to balance supply and demand. Download this free production schedule template for Excel to track production over time and have the flexibility to respond quickly to fluctuations in demand and set up inventory to avoid stock-outs.
Resource Plan Template
Use this free resource plan template for Excel to identify, list and organize the resources needed to run the production schedule. Determine the number of workers needed, their costs and when they’ll be needed by mapping out resources across a weekly calendar.
Inventory Template
Managing inventory is also critical to improving production efficiency. With this free inventory template for Excel it’s easy to record the inventory level and track its turnover. Managers can quickly see the volume and price and know when to reorder to ensure materials stay in stock.
ProjectManager Helps Improve Production Efficiency
Templates are a step in the right direction but ultimately lead to a dead end. That’s because templates are static documents that must be updated manually and aren’t ideal for collaboration. Project management software is far superior if manufacturers want to improve production efficiency. ProjectManager is award-winning project and portfolio management software that can automate workflows to add greater efficiency as well as manage resources and track costs and more all in real time.
Automate and Customize Workflows
Small and routine tasks can slow down production. Many of these activities can be streamlined by custom and automated workflows. Users can set up strict rules regarding the path a task follows by applying triggers that automate specific actions. For example, when a task’s status changes, it can be automatically assigned to a new team member. This frees up teams to focus on more complex and important tasks. Quality control is maintained through task approval settings that ensure that an authorized person oversees the work and makes sure it’s up to expectations. There’s also a recurring task function so nothing falls through the cracks.

Manage Resources and Track Costs
Keeping track of resources is another way to improve production efficiency. When onboarding teams, their availability can be set, whether it’s PTO, vacation or even global holidays. This makes assigning tasks easier. However, managers will want to check their team’s workload. If some are over overallocated that can reduce productivity and even erode morale. Toggle over to the workload chart, which is color-coded to make it easy to see who has too many or too few tasks, or the team page, which shows everyone’s allocation.
Then balance the team’s workload from those pages and keep everyone working at capacity and productive. For costs, secure timesheets streamline payroll and provide visibility into labor costs to ensure that budgets are kept and real-time dashboards offer a high-level overview of costs, time and more.

Related Production Management Content
Production efficiency is one piece of the larger story about production. Our site is an online hub for all things project management-related, with weekly blogs, video tutorials, free templates and more. Below are some articles on production scheduling software, production management, project planning and more.
- Best Production Scheduling Software for Manufacturing
- Production Management: Importance, Scope & Functions
- Production Planning 101: Making a Production Plan (Example Included)
- Production Scheduling Basics: Creating a Production Schedule
- Production Control: Process, Types and Best Practices
ProjectManager is online project and portfolio management software that connects teams whether they’re in the office, on the factory floor or anywhere else. They can share files, comment at the task level and stay updated with email and in-app notifications. Join teams at Avis, Nestle and Siemens who use our software to deliver successful projects. Get started with ProjectManager today for free.