Kanban is a visual tool that’s ideal for managing inventory flow. Taiichi Ohno, an industrial engineer at Toyota, developed it about three-quarters of a century ago. Kanban boards helped the car company restock its inventory only when it was needed, and it was the revolutionary approach that helped Toyota grow so quickly.
What Is Kanban Inventory Management?
Essentially, kanban inventory management is a way to have only the minimum amount of stock on hand that’s necessary at that time. This avoids purchasing more than you need and allocating space to warehouse that extra inventory. More than that, kanban helps avoid bottlenecks in your workflow.
Customers expect faster fulfillment than ever, especially with mobile access, yet supply chains are increasingly complex and often distributed across facilities. Having an efficient inventory management system is a competitive edge that few can afford to ignore, and a kanban inventory system can shave costs off your bottom line and give you that edge.
ProjectManager is award-winning project management software equipped with powerful online kanban boards that can help with inventory control and order management across industries. In addition, ProjectManager offers many other tools such as Gantt charts, project calendars, timesheets and real-time dashboards to help you manage projects and workflows, track costs, make timelines and monitor resource utilization. Get started with ProjectManager today for free.
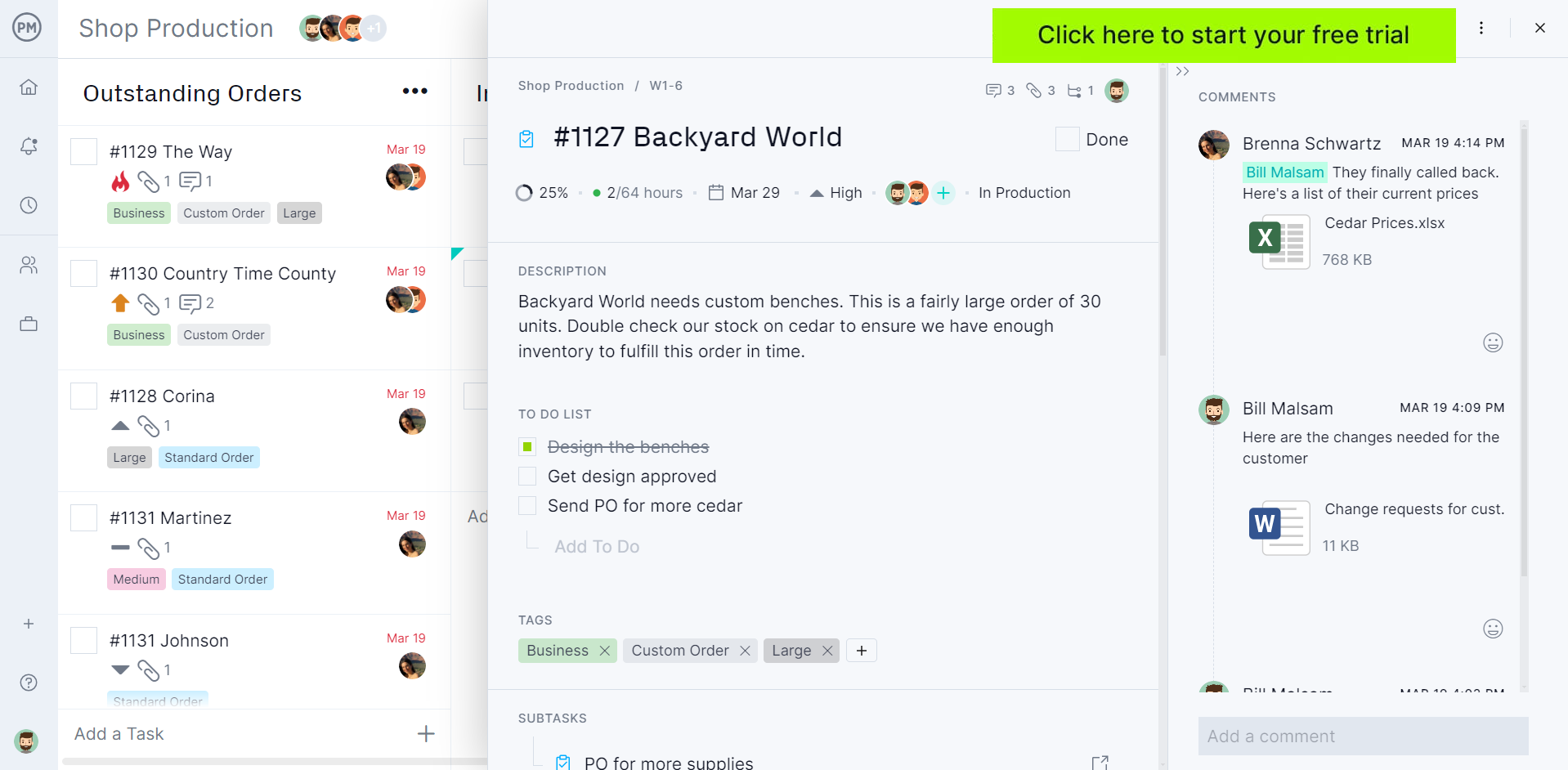
To truly understand how a kanban inventory management system works and make one for your organization, you’ll need to understand each element. Here’s a quick overview of the main components of a kanban inventory system.
Elements of a Kanban Inventory Management System
Kanban inventory control systems consist of a mix of physical elements such as shelves, storage bins, kanban inventory cards and kanban boards.
2-Bin Inventory Warehouse
While it might sound simple, one of the most important elements of a kanban inventory system is two plastic bins that hold the same quantity of inventory items and are stored beside each other at a specific location within the warehouse shelves along with their corresponding kanban card.
The objective of these bins is to control the inventory levels for these items and help employees easily notice whenever it’s time to reorder them. If an employee empties one of the two bins as he uses materials, he’ll need to take that empty bin along with its kanban card and place it on the kanban board, which indicates that the item needs to be ordered.
Kanban Inventory Cards
A kanban card is a physical or digital card that contains information about inventory items such as a description, an image, order quantity, supplier and many other details that will help employees distinguish from one item to another and locate them in the warehouse.
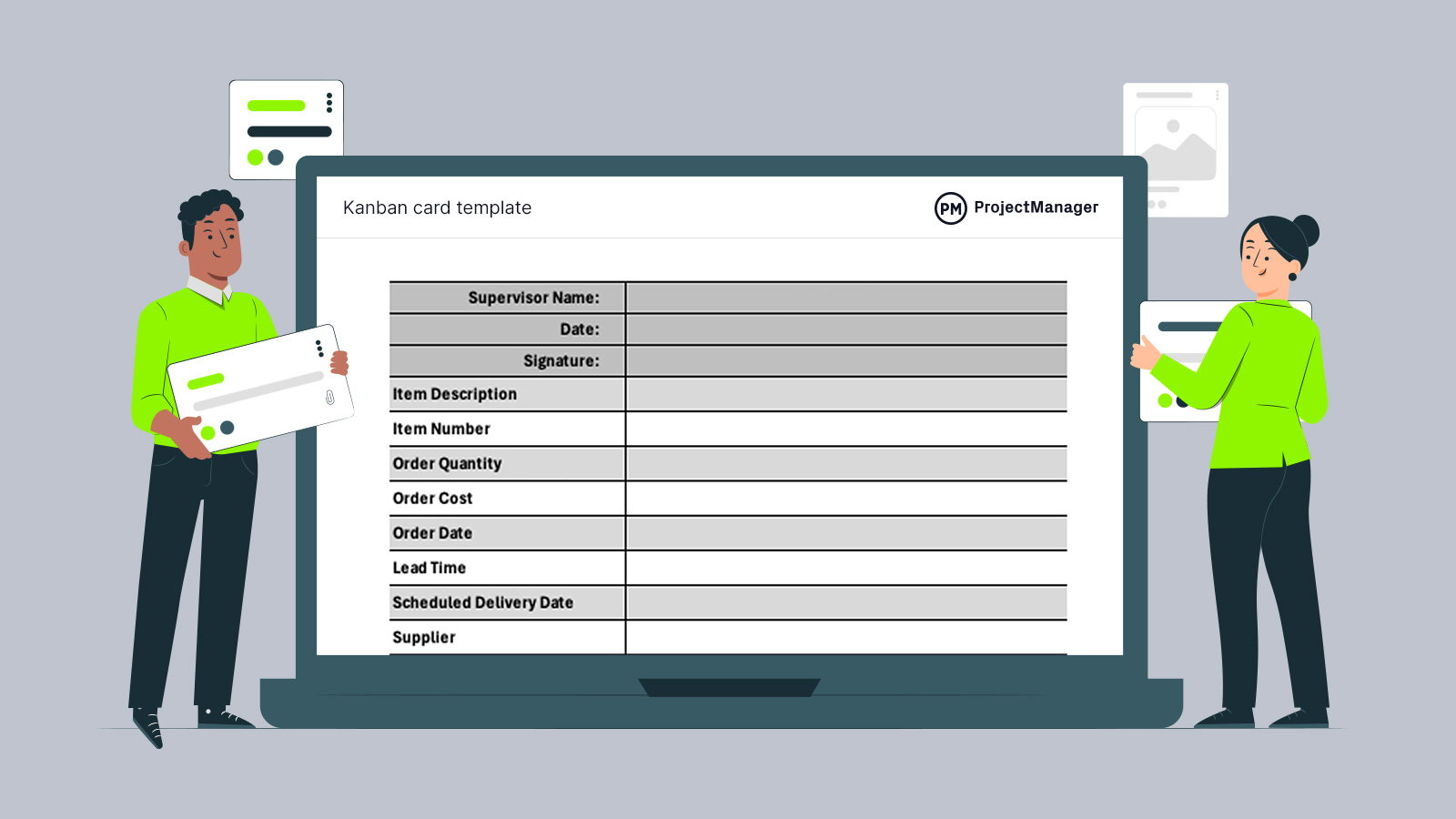
Get your free
Kanban Card Template
Use this free Kanban Card Template for Excel to manage your projects better.
Kanban Board
In inventory management, kanban boards are used to manage the different stages of the ordering process. At a basic level, you should have a physical kanban board with a column where you can place kanban cards to indicate that those inventory items need to be ordered.
How to Use Online Kanban Boards for Inventory Management
While traditional kanban inventory management is done using physical kanban cards and boards, you can streamline this process using kanban software. This makes it easier for you and your staff to order inventory items and track the status of those orders.
Here’s a quick step-by-step guide on how to use ProjectManager’s online kanban boards to manage inventories.
1. Create a Column to List Your Inventory Items
First list all the inventory items that are fully stocked and name that column. As you can see in the image below, we’ve named it “Items in 2-bin inventory.”
Then, you’ll need to create a column for each stage in your order management process, assign orders to team members, track their costs, add their expected delivery dates and much more.
Here’s what a kanban board for inventory management looks like.
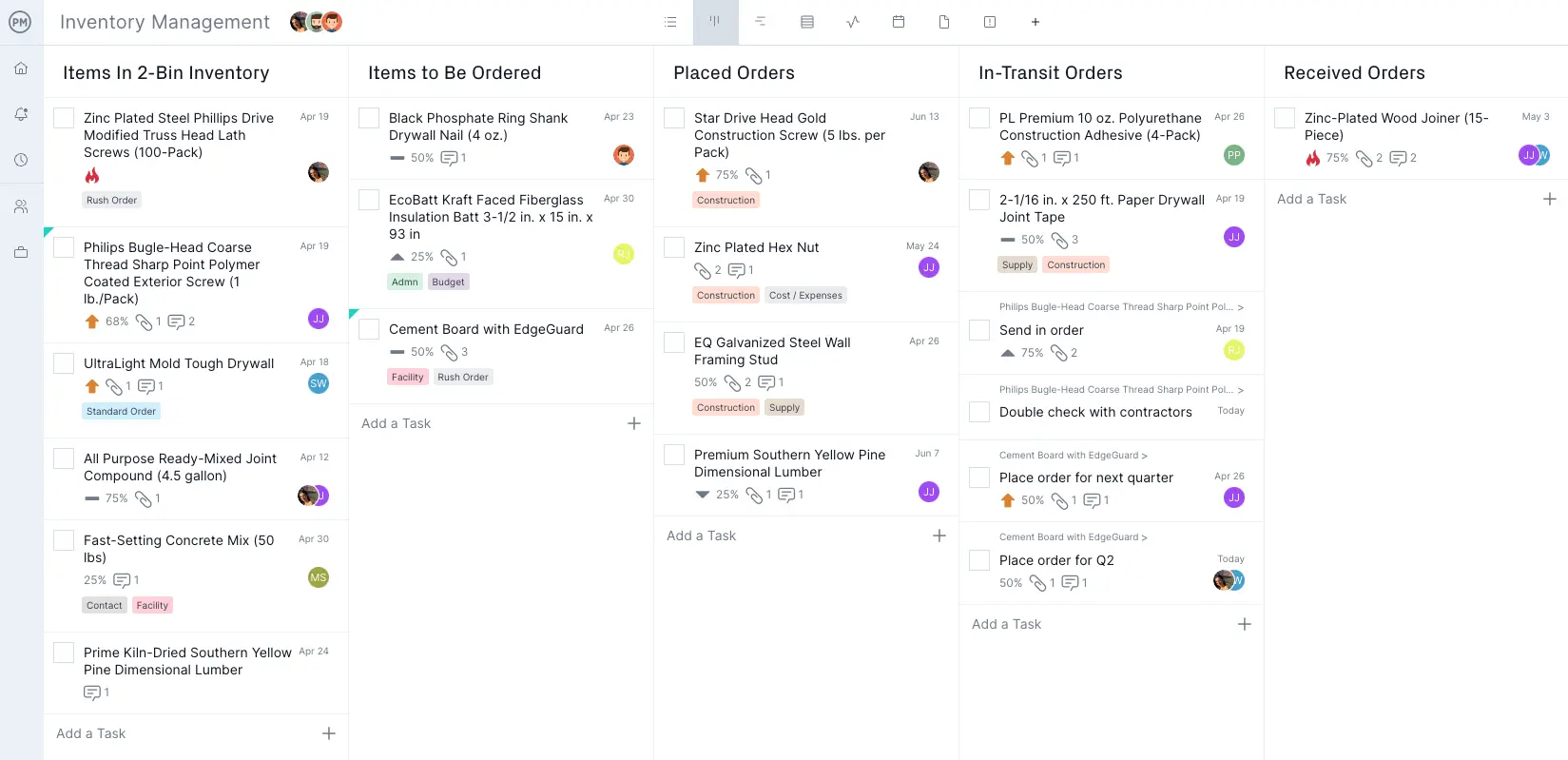
2. Create Columns for Each Stage of the Ordering Process
For this example we’ve created four columns: “Items to Be Ordered,” “Placed Orders,” “In-Transit Orders” and “Received Orders,” but you can further customize your kanban boards as needed to adjust to your inventory management needs.
- Items to Be Ordered: Whenever an employee uses an inventory item and empties a bin, this person needs to move the kanban card for this item from the inventory column to this column to indicate that it should be ordered immediately.
- Placed Orders: Once the inventory items in the “Items to be ordered” column are ordered, their corresponding cards should be moved into the “placed orders” column.
- In-Transit Orders: Once your supplier informs you that the order has been shipped, you can move the kanban card for that inventory item into the “in-transit” column.
- Received Orders: This column is meant to be used whenever an order has just arrived in but hasn’t still been sorted and stored in the 2-bin inventory shelves. Once that’s been done, you can move the kanban card back to the inventory list column to indicate the item is fully stocked.
Common Challenges in Inventory Management and Supply
Many stress points can cause a supply chain to slow down. For example, if you’re being supplied from multiple warehouses or, worse, multiple countries. However, kanban cards can represent these various links in your supply chain and make it easier to know where everything is so you can coordinate delivery.
Inventory management can also suffer from inaccurately identifying and evaluating your business needs. It’s important to know the gaps in your system, so you can prioritize filling them. A kanban inventory system offers a clear visual map of what you need, when you need it and where. You can then align that with your business plan to ensure both sides are realistic.
That said, if your inventory system isn’t optimized, you don’t know what you need or when you need it, which makes forecasting future inventory needs impossible. The cards on a kanban board capture your inventory and identify where it is in the pipeline. This makes it easier to see opportunities, so you can act and add more efficiencies to the supply chain.
Kanban Inventory Guidelines
According to how it was implemented in the Toyota factory, there are six rules guiding a kanban system:
- Never pass defective products: Upstream processes must meet the level of quality and standards that are expected of them. Remove all defective products; they’re dealt with outside the production line.
- Take only what’s needed: Downstream processes only take what’s needed to prevent overproduction. This also lowers costs and makes operations reflect market demands.
- Produce exact quantity: Avoid overproduction, which leads to excess inventory and more costs.
- Level the production: Keep production to capacity to achieve a steady flow of work.
- Fine-tune and optimize process: After implementing kanban, continue to explore ways to add efficiencies.
- Stabilize the process: Maintain quality, level production and optimize processes to gain stability so you can standardize.
Kanban Card Template for Excel
This kanban card template for Excel can help you implement a kanban inventory system for your organization, which is ideal for managing various types of inventories. You can print this kanban card template and then use it to fill out important order management information every time you need to order an inventory item.
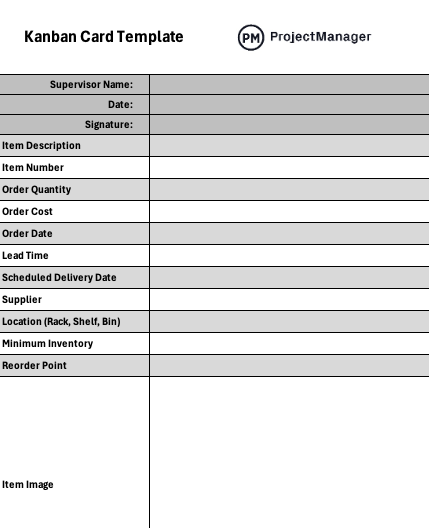
Kanban Board Template
This free kanban board template for Excel allows you to create a free kanban board you can use for kanban inventory management. Create as many columns and kanban cards as you need, simply follow the instructions on our template page.
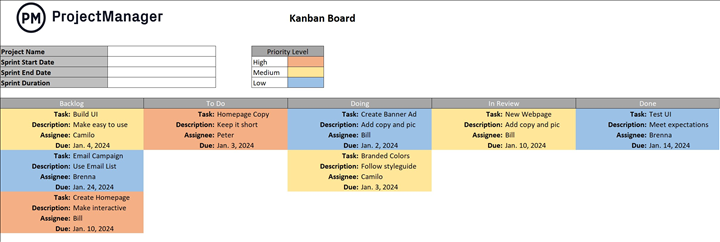
Why Use Kanban Inventory Management?
Monitoring and optimizing your inventory levels, while meeting customer needs, is an equation for a successful business venture. For one thing, this reduces the level and cost of your inventory. You can avoid unnecessary storage fees by only stocking what is needed, when it’s needed, and resupplying the stock in a timely fashion.
It’s like the old cartoon of the steam engine moving across a virgin landscape, with a workman tearing up an old track behind the train and laying it down before the train as it moves forward. It’s a joke, but it also makes sense: use what you need, when you need it. That track miles ahead or behind isn’t doing anything for you right now. Imagine if you needed to pay for storing those materials.
Meet Customer Demands
But kanban does more than maintain minimum inventory levels, it also responds to customer demands. By identifying what products are selling and therefore must be restocked before depleted, you have on hand only what is needed. The customer is the one driving inventory, which is as it should be, for the customer is the one who is going to purchase that inventory.
Quick Status Reports
There is also the added benefit for managers of having easy access to progress reports. They can see what’s been started, where it is in the production cycle and when it’s been completed. This is all laid out simply and visually on the kanban board. Plus with ProjectManager, your kanban board can be uploaded into the real-time dashboard, which creates easy-to-read and share charts and graphs of various project metrics.
For more information about our kanban board software, watch the short video below. It shows how our kanban boards tie in with our other project views, like Gantt charts and task lists, as well as our advanced reporting features. Take a look:
Cleaner Warehouse
Kanban also keeps the production area clean of unnecessary storage. It makes sure you’re only delivering the parts to the production line when needed. This makes the production space focused on what it should be focused on: production, not storage. This all dovetails nicely into lean manufacturing, which is a philosophy of continuous flow of products through the manufacturing process.
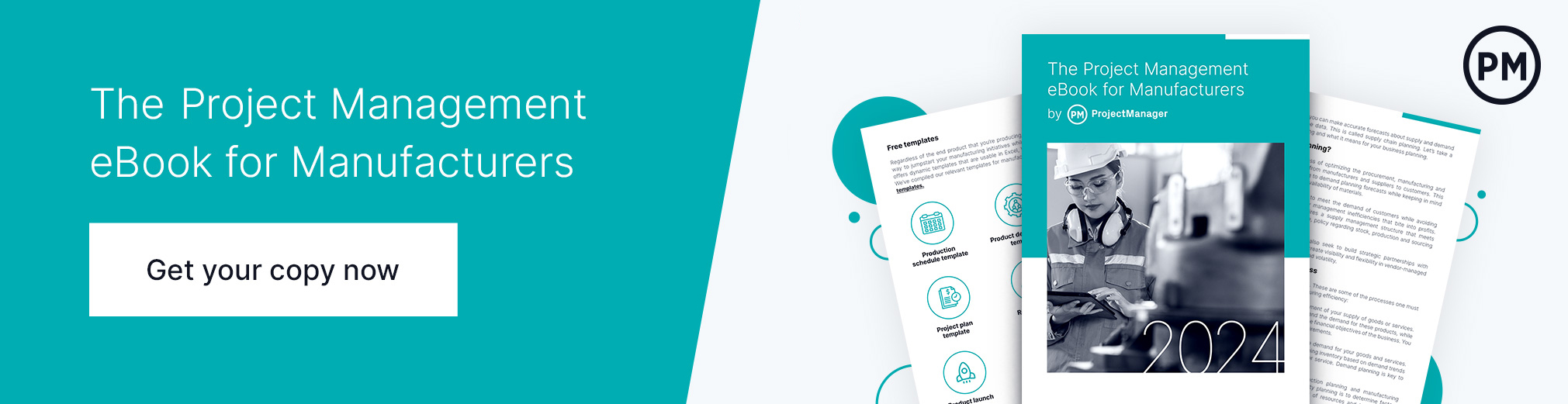
Using ProjectManager for Kanban Inventory Management
ProjectManager has all the kanban and tracking features you need to implement kanban inventory management at your business. In addition, ProjectManager’s kanban view can help manage tasks, track costs, allocate resources and more. Here’s how to set up a functioning kanban system with our tool.
Manage Customer Orders
ProjectManager’s kanban view can also help you to implement an order management system to accurately monitor the customer orders that you receive, assign them a priority level, track their status and monitor them as they go through the various stages of the order fulfillment process. This helps you monitor your production inventory and also facilitates the process of calculating your production budget and planning your production schedule.
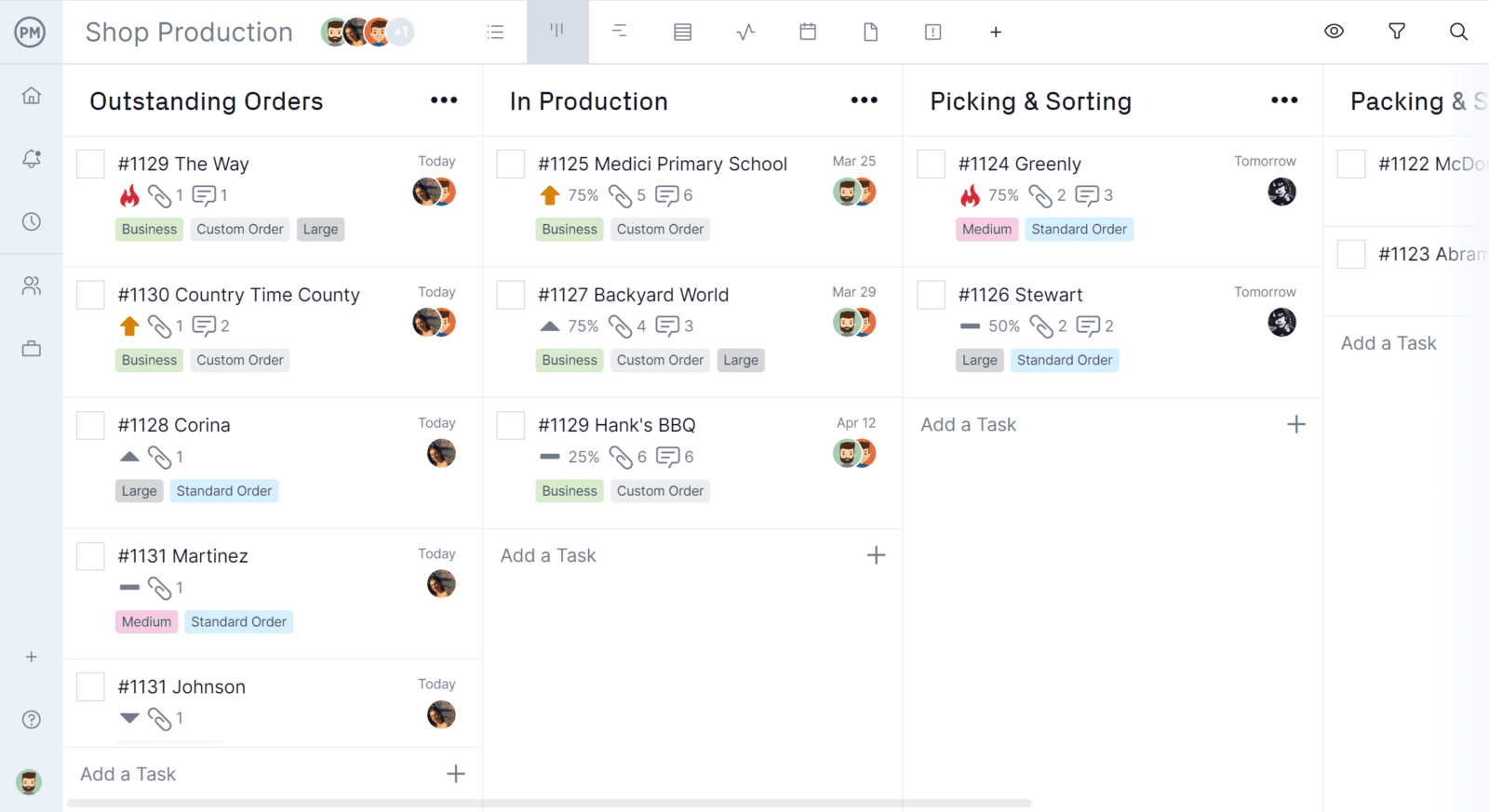
Create Kanban Cards for Specific Inventory Items
Create kanban cards that show detailed order management information for each item in your inventory such as order quantity, cost, location in the warehouse and more. These can be attached to the kanban card in ProjectManager in the form of comments, files and task descriptions.
If you need to order one of these items, simply drag and drop these cards across the kanban board to reflect the various stages of the order fulfillment process. From the moment you place an order to the moment the inventory item is successfully restocked, you’ll have the information you need.
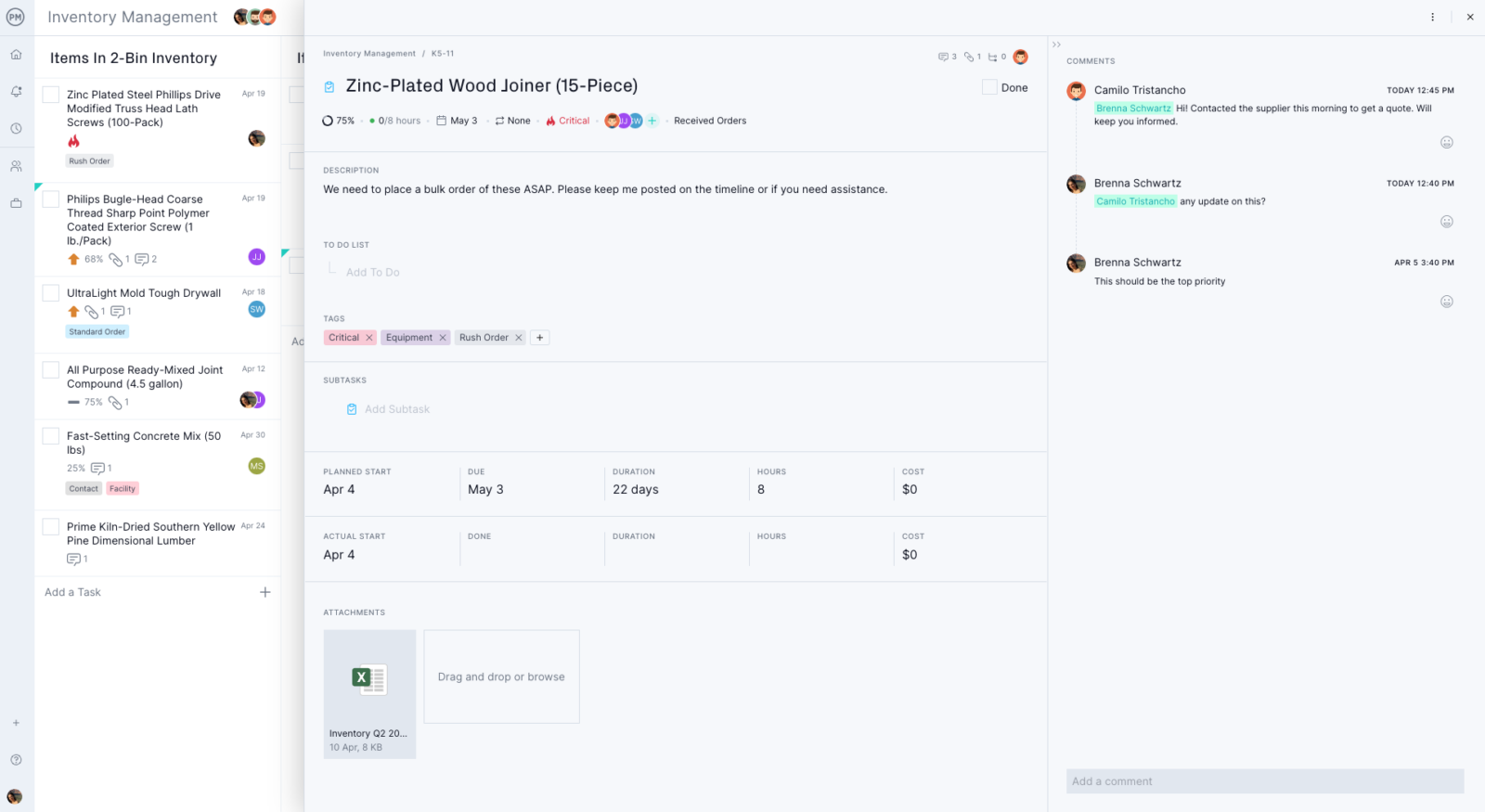
Make Specific Kanban Boards by Inventory Type
One way to start with kanban inventory is to use our project management software to create projects for each inventory type. That way, you can quickly see how much inbound and outbound inventory you have for a specific product type. Let’s say you’re stocking shoes for your company. Make a new project in the software, and then set up your kanban board to start tracking your shoe inventory.
As stated, a traditional kanban board is divided into three columns (though you can edit their names to suit your business needs). There’s a “To-Do” column, which is where identified tasks are collected. There’s a “Doing” column for those tasks that are being worked on currently. And, finally, there’s a “Done” column to place tasks that have been completed. These tasks move across the column boards as they’re being worked on, which provides an easy way to track your work.
Of course, the more complex your production and inventory, the more detailed your kanban can be to accurately reflect the process. Fortunately, ProjectManager gives you the means to make your projects as complex or as simple as you want. As you’re working to develop a kanban system to meet your needs, don’t forget to go back to the six rules above to guide you.
Kanban inventory management is an elegant solution for managing and tracking workflow. ProjectManager is a cloud-based project management software that helps you visualize your workflow with simple-to-use kanban boards, which feed into a real-time dashboard or online Gantt chart to help with reporting and scheduling. See how ProjectManager can help you manage inventory more effectively by taking this free 30-day trial.