In industries like construction and manufacturing, equipment plays a critical role in delivering projects efficiently and safely. Managing that equipment requires detailed planning and coordination. That’s where an equipment schedule comes in. It helps track what’s needed, where and when, so nothing is missed and project timelines stay on course.
What Is an Equipment Schedule?
An equipment schedule is a detailed document used to organize and communicate key information about equipment required for a project. It typically includes specifications, quantities, locations and timing. By consolidating this data, the equipment schedule helps ensure equipment is available when needed, avoids conflicts and supports smooth execution during all phases of the project lifecycle.
Gantt charts can be used as an equipment schedule in both construction and manufacturing by visually mapping out when, where and for how long specific equipment is needed throughout a project. Each equipment item or type can be represented as a task or resource, with timelines indicating its scheduled use. This approach helps avoid conflicts, ensures availability and supports efficient utilization across job sites or production phases. By aligning equipment usage with project tasks, teams can minimize downtime, prevent overbooking and coordinate logistics more effectively.
ProjectManager’s Gantt chart excels at this process by allowing users to assign equipment as resources to tasks, set dependencies and adjust schedules with drag-and-drop ease. Set a baseline to get real-time updates to ensure that any changes in task timing or resource needs are instantly reflected across the schedule, helping teams adapt quickly. The chart integrates with workload and resource views, so managers can see how equipment is allocated across multiple projects, identify potential conflicts and optimize usage. This dynamic visibility makes our software a powerful tool for managing complex equipment schedules with precision and flexibility. Get started with ProjectManager today for free.
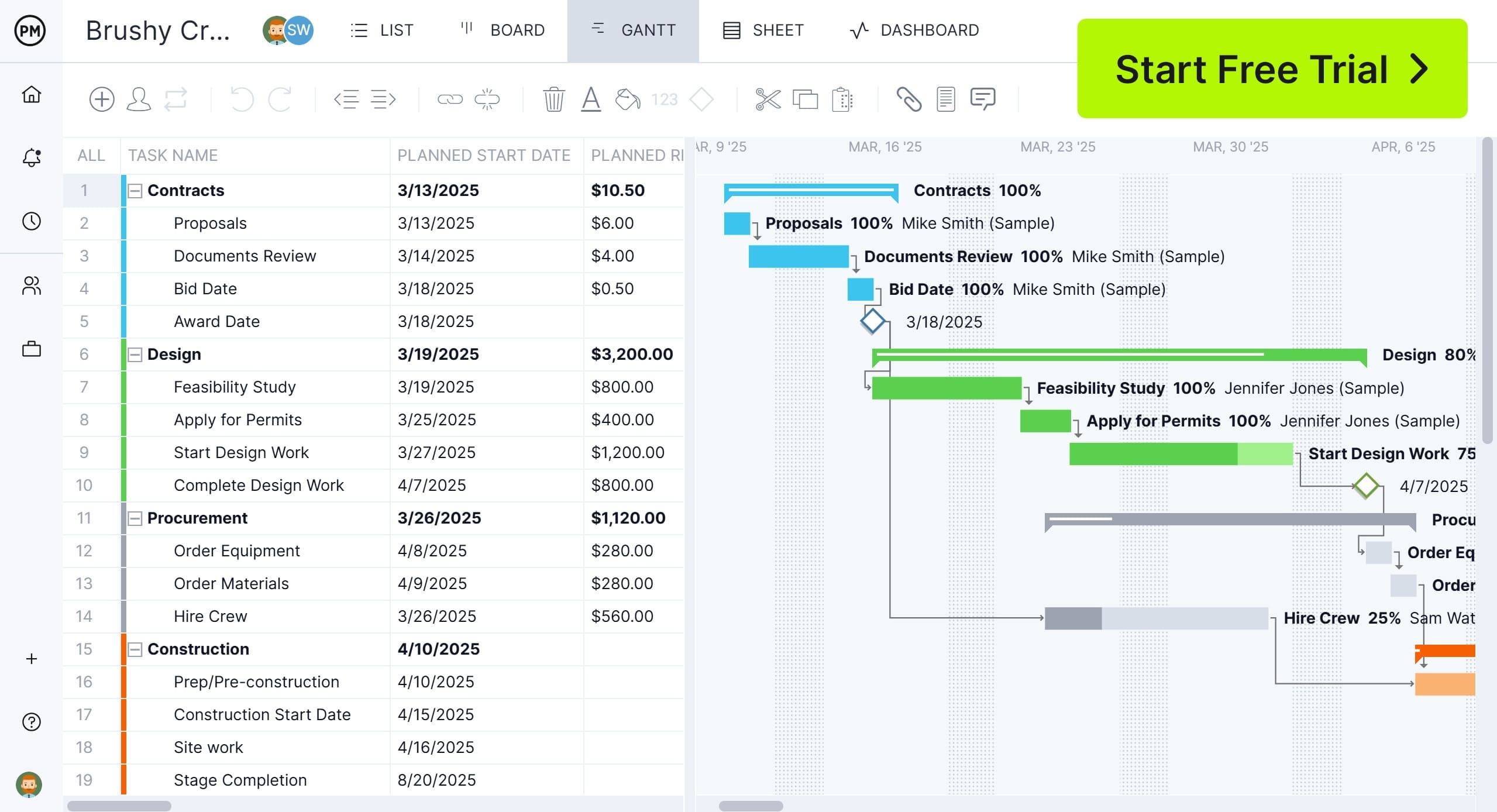
What Should Be Included in an Equipment Schedule?
Creating an effective equipment schedule means capturing all the relevant details to avoid delays and confusion during execution. Each field serves a purpose in helping teams coordinate equipment needs across tasks and timelines. Below is a list of the most common elements to include when building an equipment schedule for any construction or manufacturing project.
- Equipment ID/Tag Number: Unique identifier for tracking and reference
- Equipment Name/Description: Clear name and short explanation of what the equipment is
- Manufacturer/Model: Brand name and specific model number
- Capacity/Rating: Technical specs (e.g., BTU, kW, load capacity)
- Quantity Required: Number of units needed
- Location: Where the equipment will be installed or used
- Task/Phase Association: Related task or project phase based on WBS or schedule
- Power Requirements: Voltage, amperage or fuel needs
- Size/Dimensions: Physical size, footprint or clearance needed
- Delivery Date/Lead Time: Expected arrival date or procurement timeline
- Installation Date: Scheduled install date or deadline
- Maintenance Notes: Special handling, servicing or access considerations
- Status: Current state (e.g., Planned, Ordered, Installed, Delayed)
- Remarks/Notes: Additional details, exceptions or substitutions
When to Use an Equipment Schedule
Equipment schedules are especially helpful when managing complex projects with multiple moving parts. They bring clarity to what equipment is needed, when it’s needed and where it should be used. While they’re most commonly used in construction and manufacturing, they also play a valuable role in other areas like facility operations and long-term asset planning.
Construction Projects
In construction project management, equipment schedules help ensure the right tools, machinery and systems are available exactly when and where they’re needed. This reduces delays, avoids conflicts between trades and keeps crews working efficiently. Whether it’s cranes, generators or HVAC units, a detailed schedule aligns equipment delivery and use with the overall project timeline, helping maintain productivity and avoid costly downtime on site.
Related: 18 Best Construction Scheduling Software of 2025
Manufacturing Projects
For manufacturing projects, equipment schedules help manage the installation, relocation or upgrade of machinery and production systems. By tracking delivery dates, power needs and space requirements, teams can coordinate installations without disrupting existing workflows. This planning reduces operational risk, prevents production bottlenecks and supports continuous improvement efforts across the production floor. It’s essential for successful plant expansions, equipment rollouts and process upgrades.
Facility Management
Facility managers use equipment schedules to monitor building systems like HVAC, lighting and backup power. These schedules support preventive maintenance, help track service dates and ensure all systems remain operational. Keeping this information organized allows managers to extend equipment life, avoid unexpected failures and maintain compliance with safety or regulatory standards. It’s a key tool for ensuring long-term efficiency and reliability in facility operations.
How to Make an Equipment Schedule for a Project
Creating an equipment schedule takes more than just listing machines. It’s a structured process that ensures every task has the right equipment at the right time. By following a clear step-by-step approach, teams can reduce delays, avoid equipment shortages and improve overall project execution from planning through completion.
1. Define the Scope of Work of the Project
The first step in making an equipment schedule is to define the overall scope of work. This means understanding what the project aims to achieve, what’s included and what’s not. Once the boundaries are clear, it becomes easier to determine which tasks require equipment and what types of tools or machinery will be involved.
2. Use a Work Breakdown Structure to Identify Individual Tasks
Once the scope is defined, the next step is to use a work breakdown structure (WBS) to break the project into smaller, more manageable components. Each level of the WBS reveals specific tasks that must be completed. This breakdown helps identify where equipment will be needed and how those needs align with project phases and deadlines.
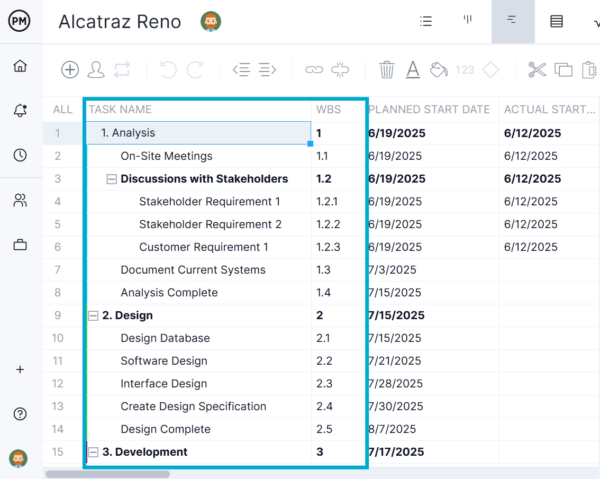
3. Assess Equipment Requirements for Each Task
After all tasks have been identified through the WBS, it becomes easier to assess the equipment needed for each one. Teams can look at each activity and determine what tools, machinery or systems are essential for successful execution. This step ensures nothing is overlooked and that equipment can be scheduled according to task timing and complexity.
4. Identify Task Dependencies
Dependencies between project tasks directly influence when specific equipment is needed. For example, some tasks cannot begin until others are completed. It’s critical to identify these task relationships and link them accordingly. Once dependencies are mapped out, teams can determine logical task sequences and assign appropriate dates for equipment usage based on the project flow.
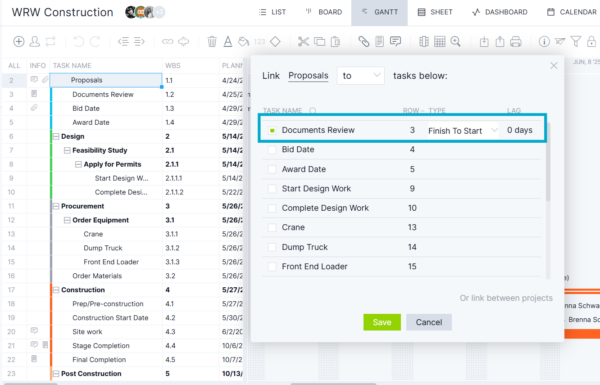
5. Create a Project Schedule
Before you can accurately plan equipment usage, you need a complete project schedule. This schedule outlines when each task is expected to start and finish. Once established, you can align the equipment schedule to ensure that resources are available precisely when they’re needed. This reduces waste, prevents delays and helps streamline execution across all project phases.
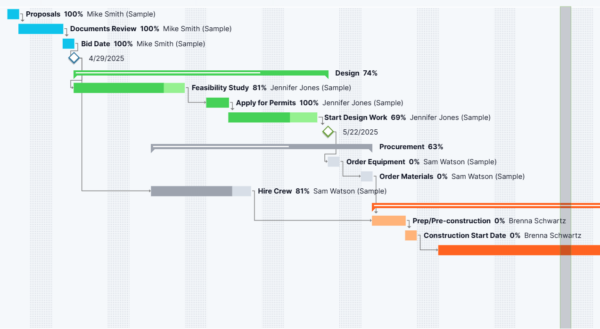
6. Find the Critical Path of the Project
The critical path is the longest sequence of dependent tasks that determines the minimum project duration. Any delay in a task on this path will directly delay the project’s completion. It includes tasks with zero float, meaning there’s no flexibility in their timing. Identifying the critical path is essential for maintaining control over time-sensitive project milestones.
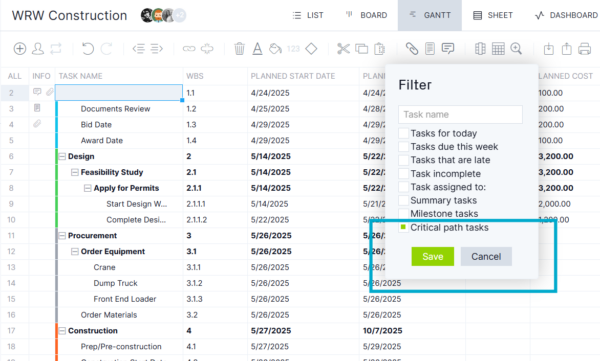
Because tasks on the critical path directly affect project completion, they must be prioritized when scheduling equipment. Delays in providing the required equipment for these tasks can cause bottlenecks and threaten on-time delivery. Ensuring that critical path tasks are supported with the right tools, machinery and systems helps keep the overall schedule intact and reduces risk.
7. Schedule Equipment Use
Once the project schedule is defined and the critical path identified, it’s time to create the actual equipment schedule. This document must align with both task durations and dependencies. You’ll now incorporate the details discussed above, such as ID numbers, locations, quantities and lead times. Doing so ensures that the right equipment will be available at the right place and time without conflicts or delays.
Benefits of Making an Equipment Schedule When Managing Projects
An equipment schedule provides multiple benefits for project managers. It enhances planning, improves communication and ensures resources are used efficiently across the project timeline. With the right equipment in the right place at the right time, teams can avoid delays, reduce waste and keep projects moving forward without unnecessary complications.
Facilitates Capacity Planning
An equipment schedule plays a critical role in capacity planning by helping managers understand how much equipment is available and how it will be used across various tasks. This visibility allows teams to assess whether current resources can meet project demands. It also helps identify shortages early, enabling proactive procurement or rental decisions before they impact execution.
Brings Clarity to Resource Utilization Tracking
Tracking equipment usage is much easier with a clear, structured equipment schedule. It allows teams to see which resources are in use, when and for what purpose. This level of detail supports informed decision-making and helps avoid overbooking or double allocation of critical equipment. It also helps in reviewing actual vs. planned equipment usage later on.
Helps Reduce Equipment Idle Time
Idle equipment represents lost money and wasted potential. An equipment schedule helps reduce this by aligning equipment availability with actual project needs. When the timeline is mapped out, equipment can be moved, shared or rotated efficiently between tasks. This minimizes downtime and ensures that every resource is contributing to progress throughout the project lifecycle.
Free Related Project Management Templates
There are other ways to manage equipment, though they pale in comparison to project management software. Still, for those who are not ready to upgrade, these free templates will prove helpful. They’re not as efficient as software, but they are free.
Equipment Inventory Template
Download this free equipment inventory template to record and track details about tools, machinery and other assets used in a project or organization. It includes fields for equipment ID, name or description, location, condition, assigned personnel, purchase date, maintenance history and more. This template helps ensure accurate recordkeeping, supports regular maintenance scheduling and prevents loss or misuse of equipment. In construction and manufacturing, it’s essential for optimizing resource allocation, managing costs and ensuring that the right equipment is available when and where it’s needed.
Gantt Chart Template
Use this free Gantt chart template to visually map tasks and durations along a timeline. It helps with equipment scheduling by allowing project managers to assign specific equipment to tasks, track usage periods and avoid overlaps or conflicts. By clearly showing when and where equipment is needed, the Gantt chart template ensures better coordination, minimizes downtime and supports efficient resource allocation across a project.
Critical Path Template
This free critical path template is a planning tool that outlines the sequence of dependent tasks that directly impact a project’s completion date. It helps with equipment scheduling by identifying which tasks are time-sensitive and must be completed without delay. By focusing on these critical activities, project managers can ensure that essential equipment is available precisely when needed, reducing idle time and preventing delays. This targeted allocation improves efficiency and keeps the project on schedule.
How ProjectManager Helps Create an Equipment Schedule for a Project
Unlike static templates that require manual updates and can’t adapt to changes, ProjectManager streamlines equipment scheduling with powerful resource management tools that work in real time. Managers can assign equipment as resources to specific tasks, track availability through the team and resource pages and spot conflicts using the color-coded workload chart. As schedules shift, updates automatically sync across the platform, ensuring that equipment is allocated efficiently, downtime is minimized and projects stay on track.
Use Multiple Project Scheduling Views
We have multiple project scheduling views that make equipment planning more flexible and precise by letting teams manage and visualize schedules in the format that suits their workflow. In the Gantt chart, managers can assign equipment to tasks and see how usage aligns with timelines and dependencies.
The calendar view offers a day-by-day snapshot of when and where equipment is needed, while the sheet view provides a detailed, editable breakdown of equipment assignments and availability. All views update in real time, so changes made in one are instantly reflected in the others, helping teams avoid scheduling conflicts, improve coordination and keep equipment usage aligned with the project timeline.
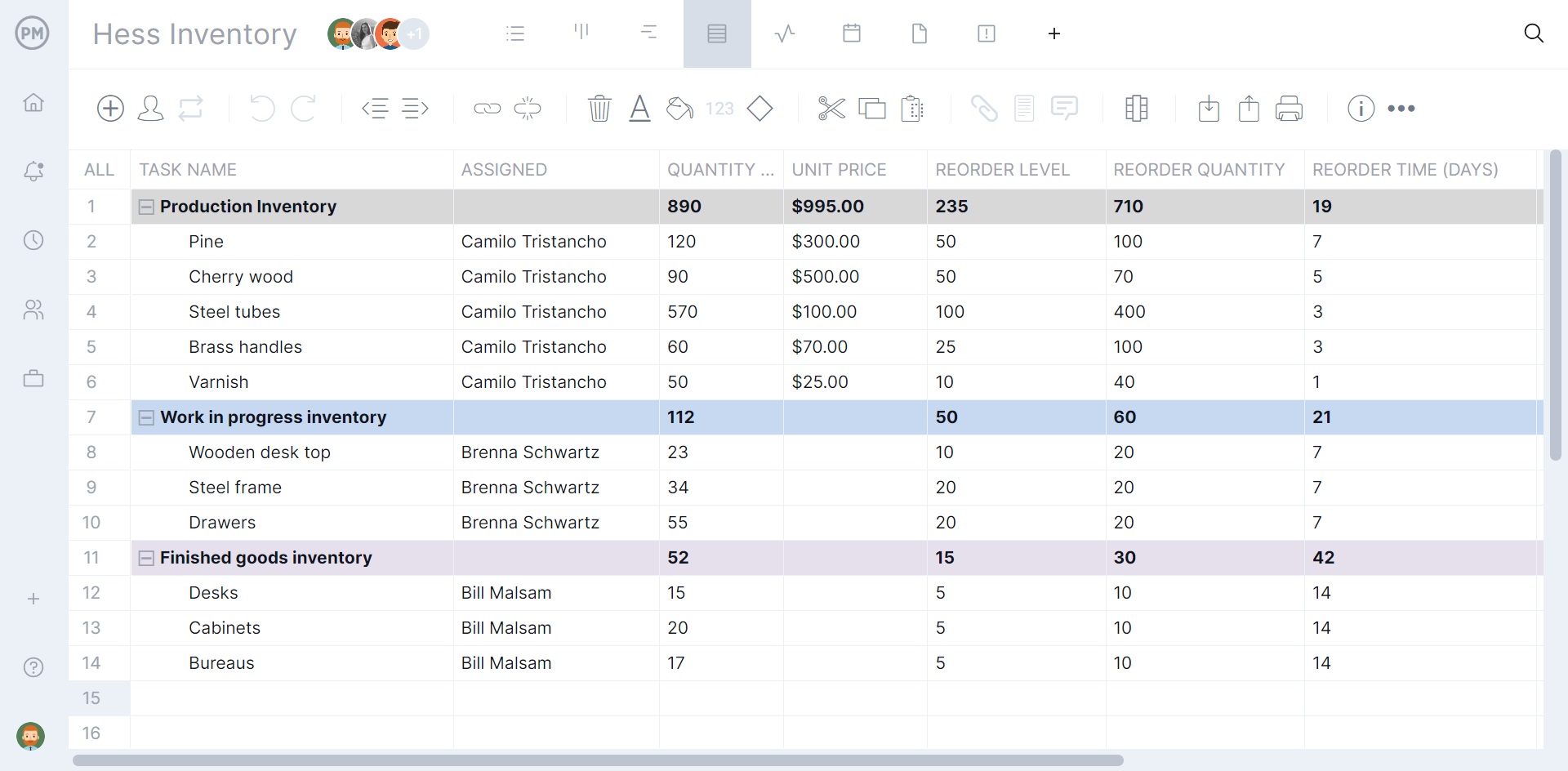
Real-time Project Management Dashboards and Reports
Our tracking tools—including real-time dashboards, customizable reports and secure timesheets—provide complete visibility into equipment usage and performance. The dashboard offers an instant overview of scheduled vs. actual equipment utilization, helping teams spot delays or overuse early. Customizable reports can break down equipment assignments, availability and maintenance needs, offering data-driven insights to support better planning and cost control.
With secure timesheets, teams can log time spent using specific equipment, feeding accurate data back into the schedule and budget. Together, these tools ensure that equipment is tracked efficiently, supporting smoother operations and keeping projects on time and within budget.

Related Equipment Schedule Content
An equipment schedule is part of the larger scheduling process in project management. For those looking to learn more about this topic, follow the links below. They cover equipment inventory, project scheduling and much more.
- Equipment Inventory: A Quick Guide
- How to Make a Project Schedule: The Ultimate Guide
- Schedule Management: Process, Tools and Templates
- Resource Scheduling in Project Management
ProjectManager is online project and portfolio management software that connects teams whether they’re in the office or out in the field. They can share files, comment at the task level and stay up to date with email and in-app notifications. Join teams at Avis, Nestle and Siemens who are using our software to deliver successful projects. Get started with ProjectManager today for free.