Work orders help organizations manage their maintenance work. They act as the paper trail that defines what needs to be done, by when and for what period of time within an organization. Work order management is critical in industries such as manufacturing, construction and others that rely on the use of heavy equipment and machinery.
What Is a Work Order?
A work order is a document that describes how maintenance work will be performed. A work order should include a description of the maintenance activities and information such as who requested and approved the work order, the maintenance technician responsible for executing the work and the associated due dates, costs and resources.
Work orders can be either executed by an internal maintenance team. If your organization doesn’t have one, you can hire a third-party maintenance contractor. Now that we’ve defined what a work order is, let’s compare work orders with other similar documents that are commonly used by organizations.

Get your free
Work Order Template
Use this free Work Order Template for Excel to manage your projects better.
Work Order vs. Work Request
Every work order starts with a work request. Your staff, customers or other non-maintenance personnel will submit a work request to make a change to an asset. Once work requests are reviewed and approved, work orders are created. Considerations that could come up when approving requests include existing maintenance plans, the current budget, the criticality or age of the asset and the severity of the issue being reported.
Work Order vs. Purchase Order
Work orders outline specific tasks or labor services that will be carried out. Purchase orders, on the other hand, outline the materials, items or products that are necessary from an outside vendor to complete a work order. A typical work order includes a purchase order with the new items or parts that’ll be used to complete the equipment repair.
Work Order vs. Service Order
The main difference between work orders and service orders is who they’re for. Typically, work orders are for in-house maintenance requests while service orders are for external parties such as a customer. Service orders outline the service that the client requests and outlines the deliverables that they require.
Work Order Template
You may be wondering what should be on a work order to yield the most effective outcome. To get a better general idea of work orders and what they entail, let’s look at a work order sample. ProjectManager has a number of free project management templates, and pictured below is a full version of our work order template. We’ll outline the different elements of the work order and how to use them later on.
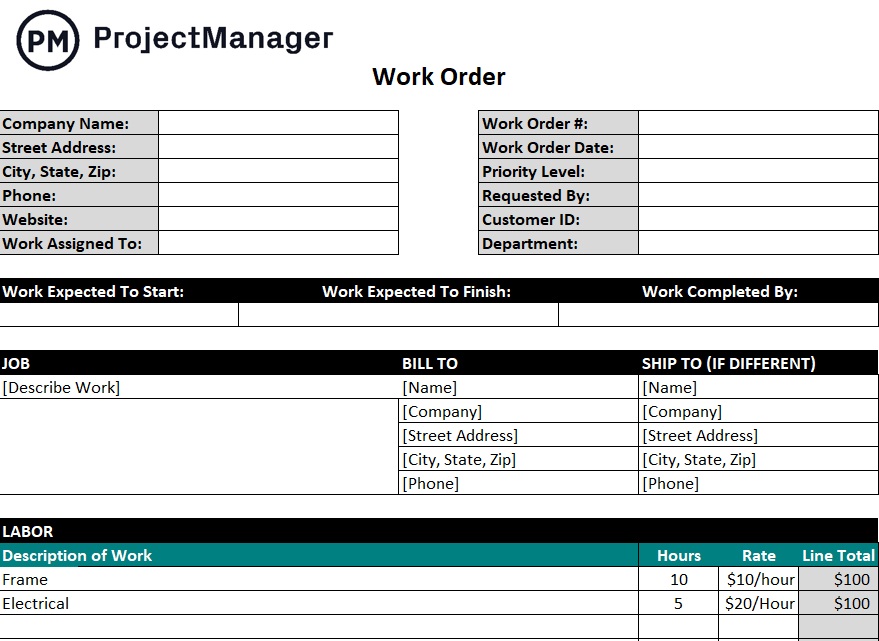
The Purpose of a Work Order and When to Use One
Work orders standardize workflow and create a simple and fast process for scheduling, assigning and tracking maintenance work while documenting resources and tracking performance.
Work orders are primarily used in the construction industry for service requests, but they can also be used for products, inspections and audits. Work orders may not always be referred to as such. For example, in manufacturing, a work order is often called a sales order when a build or engineering is to take place.
Regardless of what industry a work order is used in, it’s used to track and monitor the status of the job to ensure it’s finished on time and within budget. This is true when work orders are used in field service or within an industry that’s tasked with regular inspection. In that regard, they act almost like a project status report.
Why Is It Important to Use Work Orders?
Work orders are all about efficiency. They help your business operate in a more standardized way as they work to streamline maintenance planning workflows. Work orders highlight what jobs need to be done, when they should be completed and by whom. When you use a work order, you can achieve:
- Increased efficiency
- Customization and adaptability to keep up with company evolution
- Increased sales while reducing costs and inefficiencies
To simplify creating and managing work orders, you need the right tools. ProjectManager has planning tools such as Gantt charts, kanban boards and task lists to create online work orders and track their progress. Easily create tasks, assign work to team members, set due dates and control costs with online timesheets. Get started for free.
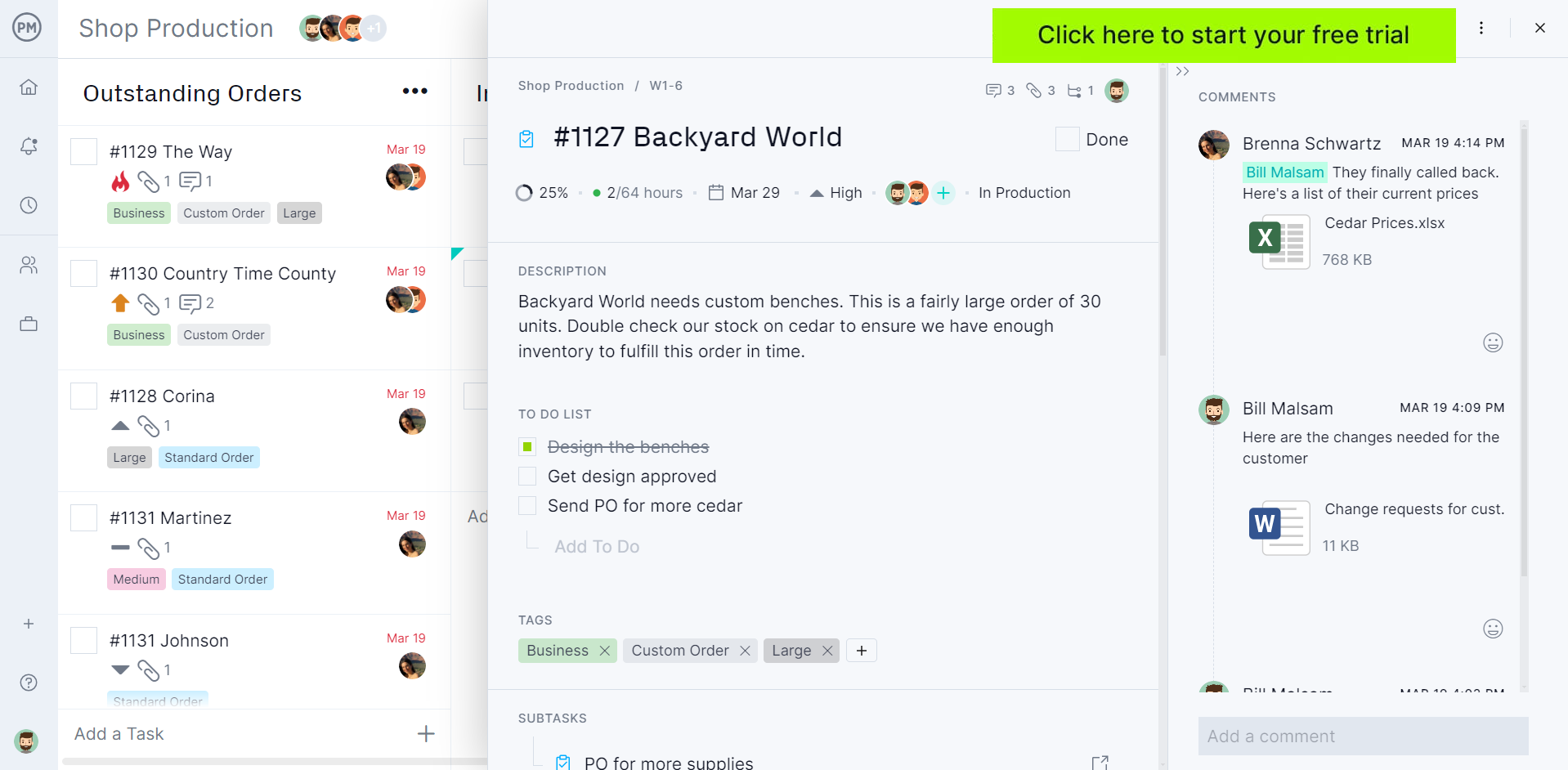
Work Order Example
You may be wondering what should be on a work order to yield the most effective outcome. To get a better general idea of work orders and what they entail, let’s look at a work order sample.
For example, let’s say you work at a manufacturing company where you need to start producing a new type of table. The project stemmed from a submitted work request that was approved, resulting in the official creation of a work order.
In this work order, you’ll first need to input the data. In this case, that means including the type of wood that will be used, the measurements of each component and the steps of how to put the table together. You can also include details such as the due date, priority level, category, assignee, additional workers, team, location and asset.
Tracking progress is the second step in the work order. Be sure to list the start and finish times for each step and what party will be responsible for which aspects. Many people opt to use reports to share with stakeholders to keep them informed of work order progress.
The last step is to keep the information updated, and any changes need to be closely documented. For example, if you cannot source the initial type of wood that you were going to use or you need more time to perfect the table design than you originally anticipated, make sure to constantly note updates that can impact the project.
Once the work order has been completed and the table is finished, it can officially be closed so long as the project doesn’t need to be recurring.
Types of Work Orders
There are different types of work orders that are part of the maintenance schedule of an organization. Here are the most common types of maintenance work and the types of work orders that are created for maintenance teams.
- General work order: A general work order describes activities that can’t be classified as preventive, inspection, emergency or corrective maintenance work. An example of a general work order could be setting up new equipment in a production facility.
- Preventive maintenance work order: Preventive maintenance work orders are used to schedule routine maintenance work that needs to be done to keep equipment working at optimal conditions.
- Inspection work order: Inspection work orders, as the name suggests, are issued whenever an organization wants to inspect its assets. These are usually recurring maintenance tasks similar to preventive maintenance work orders, however, maintenance technicians are focused on identifying risks and problems.
- Emergency work order: Emergency work orders are issued whenever an asset breaks down, and this requires immediate action from the maintenance team. These are also known as reactive maintenance work orders and have a high priority level.
- Corrective maintenance work order: A corrective maintenance work is employed whenever a maintenance technician identifies a maintenance issue, problem or potential risk. Corrective maintenance differs from emergency maintenance because in this case, the problem or issue is diagnosed before it becomes an emergency that causes equipment to fail.
What Should a Work Order Include?
Now that we’ve learned the basics of work orders and work order management, let’s learn what a work order should include. Here are some steps you can follow to write a work order. Then, use our work order template to create your own work orders with ease.
Contact and Internal Information
Our free work order template can be customized to fit the perimeters of your business, but it’s fully loaded with the basics. At the top is where much of the pertinent information is captured, such as company name, address and contact.
There’s also a place to add the work order number, which is key to keeping track of the job and finding the work order quickly. Dates are included for when the work order is issued, when the work is expected to start, finish and when it’s completed.
A priority level can be set. The person who requested the work order is identified and a customer ID for internal use is given. For larger organizations, the department can be specified.
Job Description
The meat of the work order is the job and its related labor and materials. Here, the work is described, who is billed is identified, and, if necessary, where the work will be shipped is identified.
Following this is a detailed description of the work to be done and how many hours it will take to do each maintenance activity, as well as the rate of the worker tasked with the job. This is then totaled.
Required Materials
The next section in our work order sample lists the materials needed to complete the work order, how much of each, the cost and any applicable tax. This is added to the above total for a subtotal. Any additional charges are added to this subtotal to reach the total price of the work order.
Finally, there’s space to add additional information before the signature and dateline. Again, these are just 3 basic steps to create a work order, but with these steps and a few tweaks to our free work order template, you can create any type of work order.
The Work Order Process
To create a work order, organizations usually go through this basic 3-step work order process.
1. Create a Work Request
Work orders can’t be created without submitting a work request first. Work requests are created once a maintenance issue is identified. They can be submitted under a different number of cases such as a customer request, a safety inspection, a preventive maintenance audit or an internal request.
2. Evaluate the Work Request
Work requests are submitted to the maintenance manager, who evaluates them and turns them into a work order. To do so, he must first determine if it’s feasible to execute the requested maintenance work and then allocate resources such as materials, equipment and personnel in order to create a work order.
3. Create a Work Order
Once the maintenance manager has identified the necessary resources to execute a work request, he can turn that work request into a work order. As stated above, the work order includes all of the information about the maintenance activities to be performed such as the due dates, job description and requirements, among other details.
ProjectManager Helps With Work Order Management
ProjectManager is award-winning software that helps organize work and drive efficiency. Generating, tracking and paying for work orders is enhanced by our online tool that gives you real-time data to always know if you’re keeping on schedule.
Our kanban boards let you create digital work orders and manage them online. Simply use our kanban cards to enter the information about your work order, assign it to a team member, set due dates and track its progress across the kanban board. ProjectManager’s kanban boards also allow you to schedule recurring tasks, which are ideal to schedule preventive, inspection and corrective work orders.
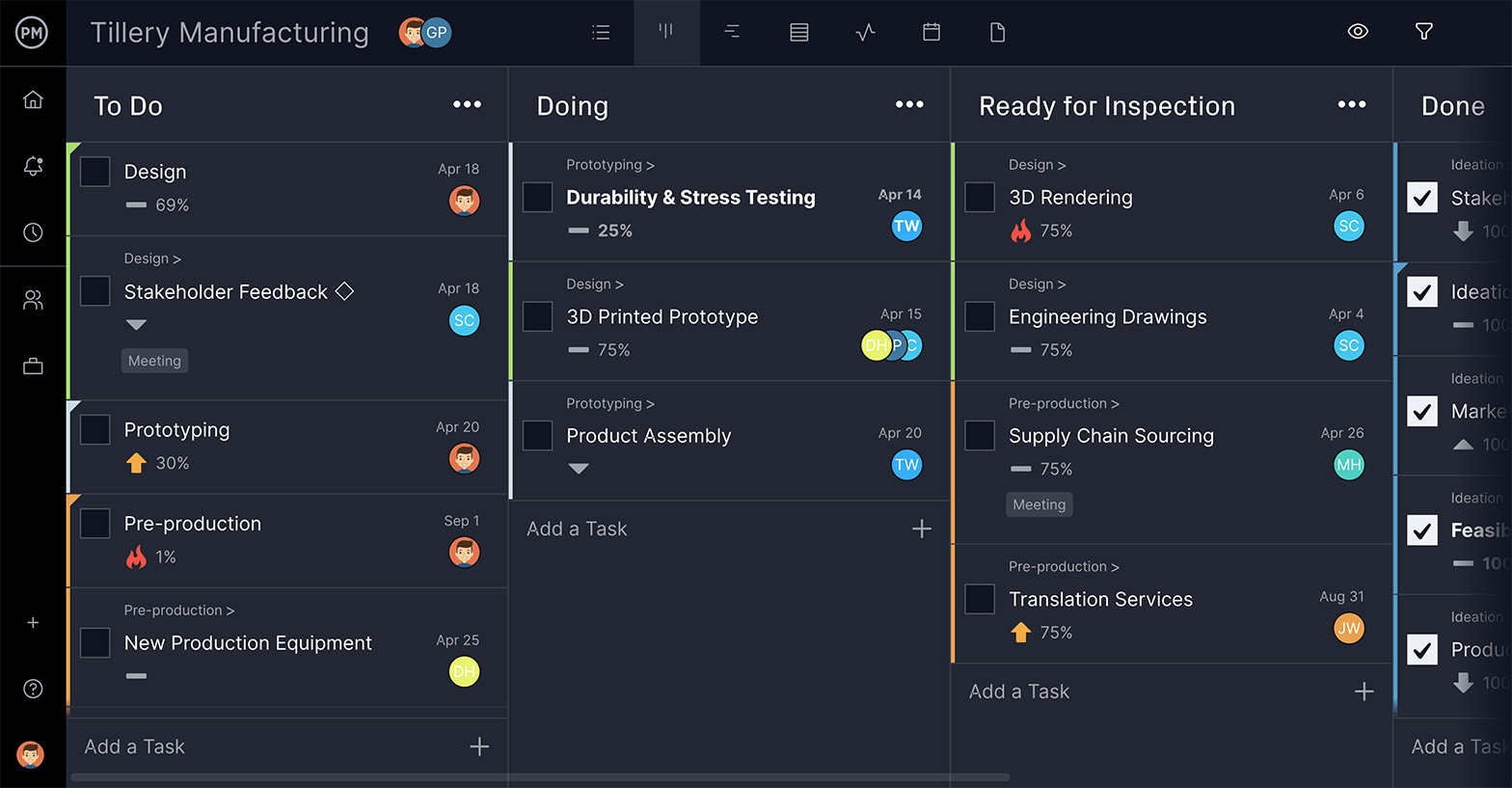
Track Work Orders With Online Dashboards
Keep track of the progress of your work orders on online dashboards that automatically reflect status updates and calculate metrics such as time, percent complete, costs and more. For example, if you’re putting together a mechanic work order and your maintenance crew is in the field, they can still collaborate online with the rest of the team.
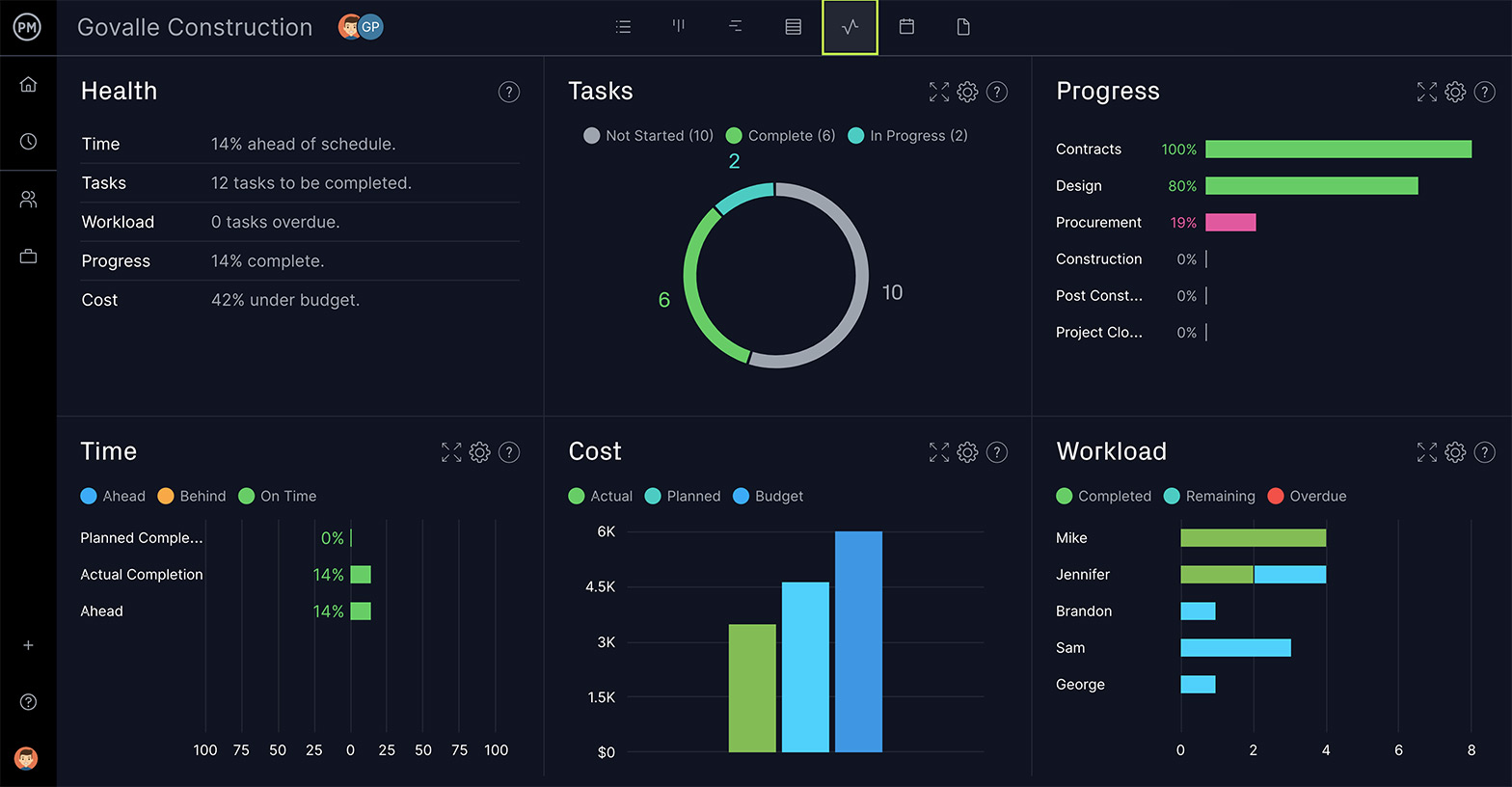
Control Costs With Cloud-Based Timesheets
Time logged on work can also be tracked with timesheets that streamline payroll as well. They’re secure and easy to use. Our unlimited file storage means you can use the tool as a centralized hub to manage all your work orders.
ProjectManager is an online tool that organizes work and workers for greater productivity. Manage your work orders and keep your team working wherever they are or whenever they’re working. Try ProjectManager today by taking this free 30-day trial.