In resource-heavy industries like construction and manufacturing, managing project costs effectively is critical for profitability and long-term success. Without a structured costing method, it’s easy to lose track of how money is spent across labor, materials and equipment. Choosing the right costing method helps project managers allocate resources wisely, forecast expenses more accurately and stay on budget.
This article explores 12 proven costing methods that can be applied to construction and manufacturing projects to improve cost control and efficiency.
Definition of Costing Methods
Costing methods are systematic approaches used to estimate, allocate and track the costs of completing work. These methods define how expenses are assigned to products, tasks or services based on different factors such as resources consumed, project duration or production volume.
In construction and manufacturing, costing methods provide a framework for managing budgets, improving financial forecasting and making better decisions about resource use. Selecting the right costing method depends on the project type, complexity and accounting requirements of the organization.
Gantt charts in project management software can be helpful with costing methods. ProjectManager, award-winning project and portfolio management software, has Gantt charts that support various costing methods by visually aligning task schedules with associated resources and budgets, making it easy to track, forecast and control costs throughout a project.
Each task on the Gantt chart can be linked to labor rates, material costs and equipment expenses, allowing for accurate bottom-up or activity-based costing. As tasks progress or change, the Gantt chart updates in real time, reflecting the impact on total project costs.
This integration supports planned vs. actual cost comparisons, enables early identification of overruns and helps apply costing strategies like earned value management (EVM) directly within the schedule. By combining time, resources and cost data in one visual timeline, our Gantt chart offers a clear, actionable view of project finances. Get started with ProjectManager today for free.
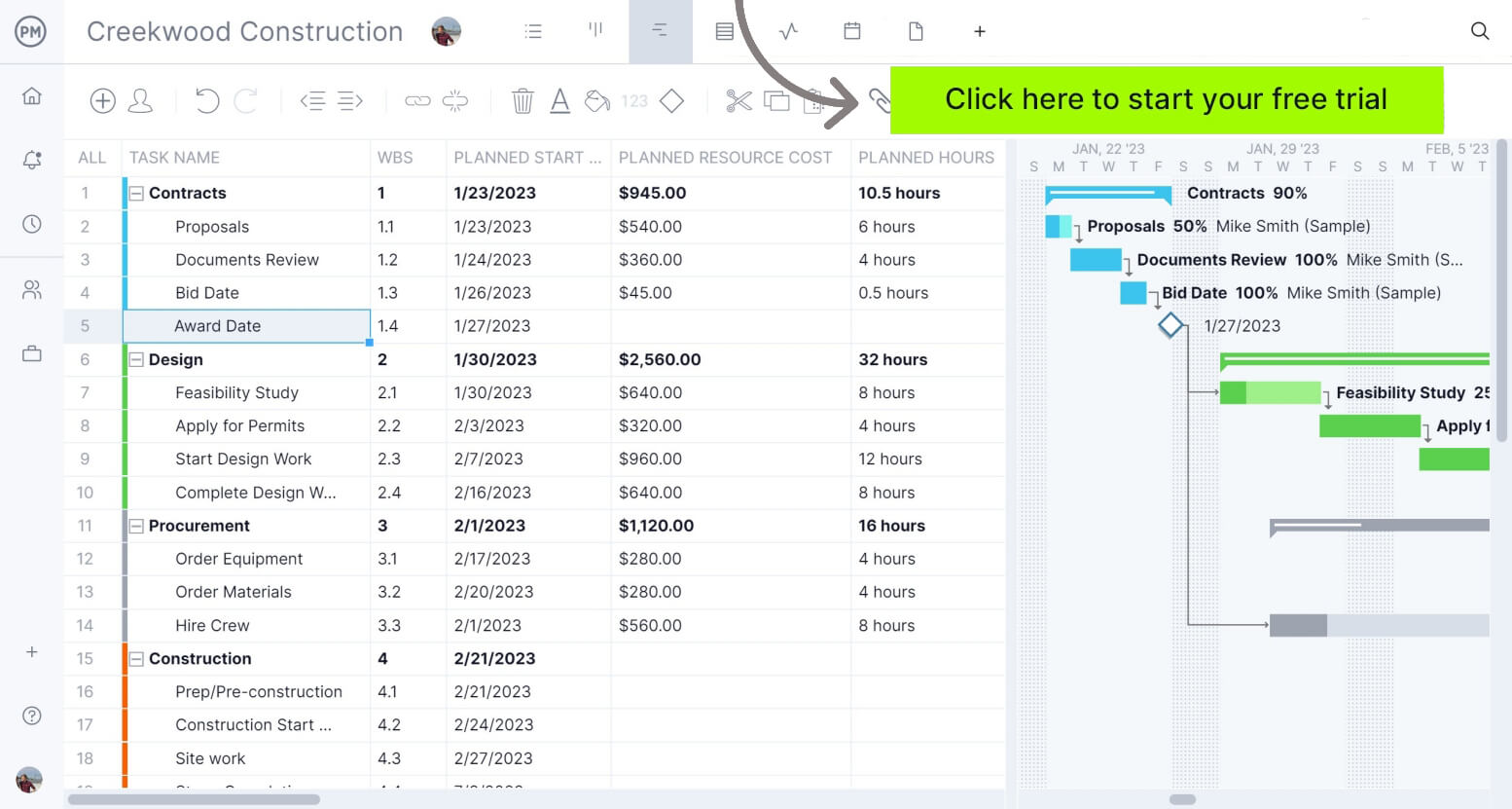
Top 12 Costing Methods for Construction and Manufacturing Projects
Different projects demand different approaches to cost control. Whether you’re managing a factory or a building site, understanding various costing methods helps ensure accurate budgeting and accountability. Below are 12 reliable costing methods commonly used in construction and manufacturing.
1. Standard Costing
Standard costing is a cost accounting method where predetermined costs are assigned to materials, labor and overhead before production begins. These standard costs serve as benchmarks for measuring actual performance. Variances between standard and actual costs are analyzed to identify inefficiencies, control spending and improve processes. This method is widely used in environments where production is repetitive and predictable, making it easier to set realistic standards and monitor deviations over time to maintain cost efficiency.
Standard Costing in Manufacturing
Standard costing is a costing method that’s most relevant in manufacturing, where identical products are produced regularly. By assigning standard costs to each unit, manufacturers can streamline budgeting, pricing and inventory valuation. It simplifies variance analysis, enabling managers to quickly identify areas where costs deviate from expectations. This is particularly useful in large-scale operations, where even small inefficiencies can accumulate into significant losses.
Standard Costing in Construction
Standard costing can also be applied in construction by setting baseline costs for recurring materials, labor tasks or equipment usage. These standards help project managers track deviations across multiple sites, especially in firms managing similar project types. It enables better forecasting, improves accountability and supports cost control by highlighting where performance falls short of planned productivity or resource efficiency targets.
2. Activity-Based Costing or ABC Costing
Activity-based costing (ABC) is a costing method that assigns costs to products or projects based on the specific activities required to produce them. It identifies cost drivers—factors that consume resources—and allocates expenses accordingly. ABC provides a more accurate view of cost distribution than traditional methods by linking overhead and indirect costs to actual resource consumption. This approach is especially helpful in organizations with diverse products or services, where indirect costs represent a significant portion of total expenditures.
ABC Costing in Manufacturing
ABC costing is especially valuable in manufacturing, where understanding the true cost of each product line is crucial. It helps companies trace indirect costs like machine maintenance, quality control and logistics to the specific products or processes that generate them. This allows manufacturers to identify unprofitable lines, optimize operations and refine pricing strategies.
ABC Costing in Construction
In construction, ABC costing helps allocate indirect costs—like site supervision, equipment maintenance and permitting—based on the specific activities that generate them. This improves cost accuracy on complex projects with varied scopes. By identifying high-cost activities, contractors can streamline operations, negotiate better subcontractor rates and optimize resource deployment across multiple job sites.
3. Job Costing
Job costing is a method used to track costs associated with a specific project, order or job. Each job is treated as a separate cost unit, and expenses for materials, labor and overhead are recorded individually. This method allows for detailed cost tracking and analysis, making it ideal for work that varies in scope or requirements. Job costing provides visibility into the financial performance of each project, helping companies control spending, improve estimates and increase profitability over time.
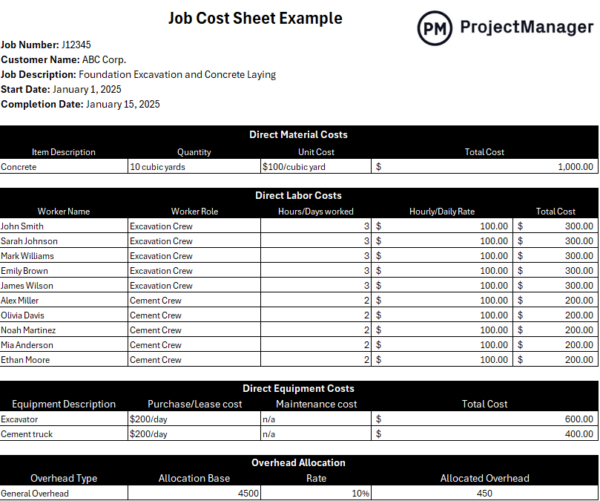
Job Costing in Construction
Job costing is one of the most important costing methods in the construction industry, where every project is unique. It allows contractors to assign costs to specific tasks, phases or locations within a project. This level of detail helps project managers monitor budgets in real time and make adjustments when needed. Job costing also supports more accurate bidding and forecasting for future projects. By understanding where money is spent, construction firms can reduce waste, control labor costs and improve project profitability across multiple job sites.
Job Costing in Manufacturing
In manufacturing, job costing is useful for custom or small-batch production runs, such as made-to-order products or prototypes. It allows manufacturers to track labor, materials and overhead per job, ensuring accurate pricing and profitability. This method is especially effective in industries like aerospace, tooling or specialty machinery, where each unit or order has unique specifications and resource requirements.
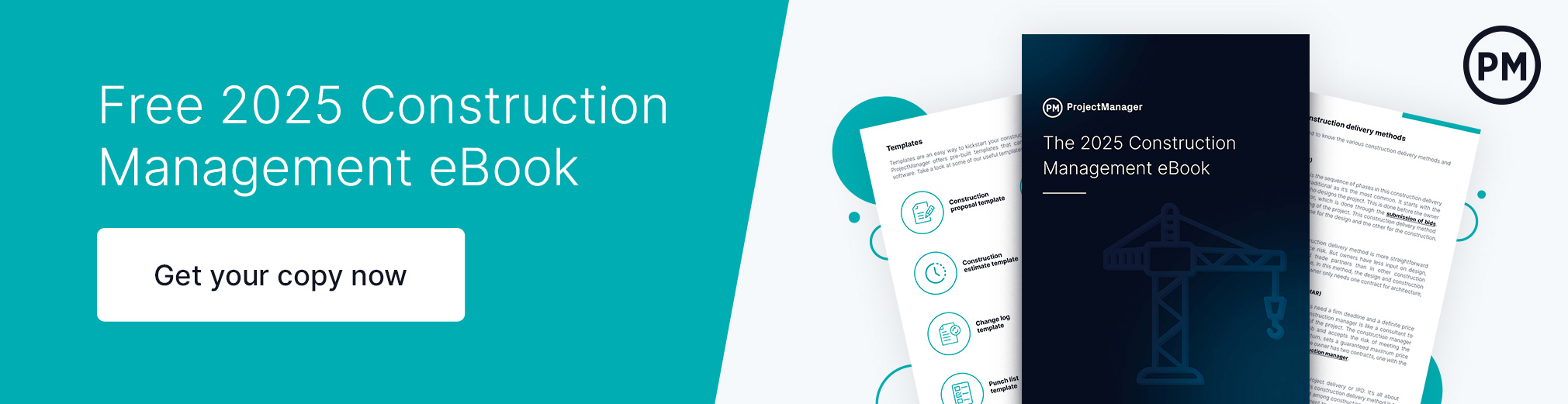
4. Process Costing
Process costing is a costing method used to assign production costs to large volumes of identical products. Rather than tracking costs per individual unit, expenses are averaged across all units produced during a specific period. This method simplifies cost tracking in continuous production environments, such as chemical plants or food processing facilities. It’s well-suited for operations where products pass through multiple stages and it’s difficult or unnecessary to separate costs for individual units during each step of production.
Process Costing in Manufacturing
Process costing is most applicable to manufacturing industries that produce goods in a continuous, standardized flow. In this environment, tracking costs per unit is impractical due to the sheer volume of production. Instead, manufacturers use process costing to allocate costs to each stage—mixing, molding, packaging and so on—then average those costs across all output. Such costing methods ensure consistent unit cost calculations and help with inventory valuation, pricing and performance analysis in high-volume production settings.
5. Batch Costing
Batch costing is a method used to determine the cost of producing a batch of identical units, rather than costing each item individually. The total cost of the batch—including materials, labor and overhead—is divided by the number of units to find the cost per unit. This method is especially useful when production occurs in fixed lots or groups. It simplifies cost control, enables more efficient resource planning and provides consistent costing for repeated production runs of the same product type.
Batch Costing in Manufacturing
Batch costing is widely used in manufacturing environments that produce items in set quantities, such as pharmaceuticals, electronics or clothing. It allows manufacturers to calculate the cost per batch, helping to streamline pricing, procurement and production planning. This costing method also supports better inventory management by grouping items with similar characteristics. Manufacturers benefit from greater efficiency and more accurate cost assessments when products are made in predictable volumes rather than on a continuous or individual basis.
6. Target Costing
Target costing is a proactive cost management method that begins with a competitive market price and desired profit margin. Based on these inputs, a maximum allowable cost is set for the product. Design, production and operational processes are then engineered to meet that cost constraint. Target costing emphasizes early planning and collaboration across departments to achieve cost objectives without compromising quality. It is often used during product development to align profitability goals with customer expectations and market conditions.
Target Costing in Manufacturing
The target costing method is especially relevant in manufacturing, where companies must compete on both price and innovation. By working backward from a target price, manufacturers identify cost-saving opportunities early in the product design phase. Engineers, procurement teams and production planners collaborate to adjust specifications, materials or processes to meet cost limits. This approach helps manufacturers stay competitive, deliver value to customers and maintain healthy margins, particularly in industries like automotive, electronics and consumer goods.
Target Closing in Construction
In construction, target costing helps firms deliver projects within strict client budgets by defining the maximum allowable cost during the planning phase. Designers, engineers and contractors collaborate to adjust scope, materials and methods without compromising quality or compliance. This approach is especially useful in design-build projects, where staying competitive requires balancing affordability, performance and stakeholder expectations from the outset.
Related: 20 Free Excel Construction Templates
7. Absorption Costing
Absorption costing, also known as full costing, is a costing method that assigns all manufacturing costs to a product, including direct materials, direct labor and both variable and fixed overhead. This approach ensures that each unit produced reflects the full cost of production. Absorption costing is required under many accounting standards for external reporting. It provides a more comprehensive view of profitability, although it may sometimes obscure variable cost behavior and limit short-term decision-making accuracy in internal financial analysis.
Absorption Costing in Manufacturing
Absorption costing is primarily used in manufacturing to calculate product costs for financial reporting and inventory valuation. By incorporating fixed overhead into the cost of each unit, manufacturers can match expenses with revenues more accurately in accounting periods. This method also helps with pricing strategies, as it captures the full economic cost of production. While less helpful for marginal decision-making, absorption costing remains essential for compliance with accounting standards and for presenting a complete financial picture of operations.
Absorption Costing in Construction
In construction, absorption costing can be used to allocate both direct and indirect project costs, including fixed overhead like equipment depreciation or salaried site management. This method helps firms capture the full cost of each project for financial reporting. Costing methods that factor in overhead costs facilitate an accurate profitability analysis and align with accounting standards, particularly for large contractors managing multiple ongoing projects with shared overhead expenses.
Related: 18 Best Construction Scheduling Software of 2025
8. Direct Costing
Direct costing, also known as variable costing, is a costing method that includes only variable production costs—such as direct materials and direct labor—in product cost calculations. Fixed overhead costs are treated as period expenses and not assigned to individual units. This approach is useful for internal decision-making, as it focuses on the costs that change with production volume. Direct costing simplifies break-even analysis, helps identify contribution margins and supports more agile budgeting in dynamic production or project environments.
Direct Costing in Manufacturing
Direct costing is useful in manufacturing, especially when analyzing product profitability and making short-term decisions. Because it excludes fixed overhead from unit costs, it provides a clearer picture of how costs behave with changes in output. This helps managers determine which products contribute most to covering fixed expenses and generating profit. Direct costing is often used in managerial reports to guide decisions on production levels, pricing or discontinuing product lines, without being constrained by accounting compliance requirements.
Direct Costing in Construction
In construction, direct costing allows firms to focus on variable costs like labor hours, subcontractor fees and materials, without allocating fixed overhead to individual projects. This makes it easier to analyze short-term project profitability and adjust estimates or crew deployment accordingly. Costing methods that focus on variable costs are especially helpful for comparing projects with similar scopes but different durations or resource needs in dynamic environments.
9. Lifecycle Costing
Lifecycle costing is a method that considers all costs associated with an asset or project over its entire lifespan—from planning and design to construction, operation, maintenance and disposal. This approach goes beyond initial acquisition costs to evaluate long-term value and total cost of ownership. It supports better investment decisions by helping stakeholders understand future financial commitments. Lifecycle costing is especially relevant in capital-intensive projects where operating and maintenance expenses significantly impact overall profitability and sustainability.
Lifecycle Costing in Construction
Lifecycle costing is highly applicable in construction, particularly for infrastructure and public works projects. By analyzing long-term costs—including energy use, repairs and eventual demolition—project owners can make informed choices about materials, systems and designs. This costing method supports sustainability goals and asset management planning, ensuring that upfront savings don’t lead to higher operational costs later. Construction firms also use lifecycle costing to improve bid proposals and demonstrate value to clients focused on long-term performance and cost efficiency.
Lifecycles Costing in Manufacturing
In manufacturing, lifecycle costing helps evaluate the total cost of equipment, tooling or product lines from acquisition through operation, maintenance and disposal. This method informs capital investment decisions, supports long-term budgeting and identifies opportunities to reduce energy use or downtime. It’s especially valuable for high-tech or automated systems, where maintenance and operational costs can exceed initial purchase costs over time.
10. Weighted Average Cost
Weighted average cost is a method used to calculate the average cost of inventory or materials by taking the total cost of goods available for sale and dividing it by the total units available. Each unit is assigned the same average cost, regardless of purchase date or price fluctuations. This method smooths out cost variations over time and is commonly used in environments where inventory items are indistinguishable or when tracking individual costs is not practical or necessary.
Weighted Average Cost in Manufacturing
Weighted average cost is most relevant in manufacturing settings with large inventories of interchangeable items. It simplifies inventory accounting and cost reporting by assigning a uniform cost to all units, making it easier to manage inventory records and calculate cost of goods sold. This method also supports financial consistency in environments where material prices fluctuate frequently. Although less precise than methods like FIFO or LIFO, it strikes a balance between simplicity and accuracy for ongoing production operations.
Weighted Average Cost in Construction
In construction, weighted average cost can be applied to manage bulk materials like concrete, lumber or piping when individual purchase prices vary. By averaging costs across all inventory, contractors simplify materials tracking and reduce accounting complexity. This costing method supports consistent budgeting and billing, especially on large projects where material deliveries occur frequently and exact price matching for each unit is impractical.
11. Unit Cost Estimating
Unit cost estimating is a method that calculates the cost of a project by multiplying the estimated quantity of work by a predefined unit rate. Each unit represents a measurable component, like square feet of flooring or cubic yards of concrete. This method is commonly used in budgeting, estimating and bidding processes, especially when dealing with repetitive elements. It provides transparency, simplifies planning and allows estimators to build a comprehensive cost model.
Unit Cost Estimating in Construction
Unit cost estimating is widely used in construction for both preliminary estimates and detailed bids. Contractors rely on standard unit prices from past projects, databases or cost books to calculate expected expenses. For example, estimating the cost to install 1,000 square feet of drywall involves multiplying the quantity by the cost per square foot. This method speeds up estimating, ensures consistency and helps compare subcontractor quotes. It’s particularly useful for public works and large infrastructure projects.
Unit Cost Estimating in Manufacturing
In manufacturing, unit cost estimating helps calculate costs for assembling or producing components in consistent quantities. It’s useful in repetitive production lines where standard times and material quantities are established per unit. Manufacturers use this costing method to estimate costs quickly, improve quote accuracy for custom orders and maintain consistent pricing strategies across similar product batches or assembly processes.
12. Resource-Based Costing
Resource-based costing is a method that assigns costs directly to the specific resources—such as labor, equipment and materials—used in a project or production process. It involves identifying the cost rates of each resource and multiplying them by the quantity or duration of usage. This approach gives a detailed breakdown of where money is spent and supports more accurate budgeting, forecasting and performance tracking. It’s particularly effective in environments with diverse resource types and variable usage rates across activities.
Resource-Based Costing in Construction
Resource-based costing is most useful in construction, where multiple trades, crews and machines are scheduled across different phases of a project. By linking costs directly to the resources used for each task, project managers gain better control over budgets and schedules. For example, assigning hourly rates to excavators or electricians helps track actual spending in real time. This costing method supports earned value analysis, change order validation and cost accountability.
Resource-Based Costing in Manufacturing
In manufacturing, resource-based costing enables precise tracking of costs tied to labor hours, machine time and material usage for each production step. This method helps identify cost-heavy operations, optimize resource allocation and improve production planning. It’s especially beneficial in complex facilities where multiple products share equipment, allowing managers to assign actual resource usage to each product more accurately.
Free Related Cost Management Templates
There are other cost method tools for those who aren’t ready to upgrade to project management software. We offer over 100 free project management templates for Excel and Word that address all aspects of managing a project. Below are just a few that can be used in cost management.
Project Budget Template
Download this free project budget template to plan, estimate and track all the financial resources needed for a project. It typically includes line items for cost categories such as labor, materials, equipment and other costs. This template helps project managers allocate funds, monitor spending and ensure the project stays within budget. By providing a clear and organized financial roadmap, a project budget template supports better forecasting, informed decision-making and accountability throughout the project lifecycle.
Cost Breakdown Template
Use this cost breakdown template to itemize all the individual expenses involved in a project. It organizes costs into categories such as labor, materials and equipment, with sections for quantities, unit prices, and total costs. This granular structure helps project managers understand where money is being spent, identify high-cost areas and improve budgeting accuracy. By offering a clear view of how the overall budget is distributed, a cost breakdown template supports better cost forecasting, financial tracking and decision-making throughout the project.
Budget Dashboard Template
A budget dashboard template is a visual tool used to track and display key financial metrics of a project or organization in one centralized view. It typically includes real-time data on total budget, actual spending, remaining funds, cost variances, and financial performance indicators, often presented through charts, graphs, and summary tables. This template helps project managers and stakeholders quickly assess the health of a budget, identify trends or issues, and make informed decisions. By consolidating complex financial data into an easy-to-read format, a budget dashboard template improves visibility, accountability, and control over project finances.
ProjectManager Is Advanced Project Cost Tracking Software
ProjectManager goes far beyond static templates by providing a dynamic, real-time platform for advanced project cost tracking that adapts as work progresses. At the core are its resource management tools, which provide precise control over project costs by aligning team availability, assignments and workload in real time. The team page offers a centralized view of each team member’s capacity and role, making it easy to allocate resources efficiently.
With availability settings, managers can account for work schedules, time off or part-time commitments, ensuring accurate cost planning. The color-coded workload chart highlights overallocation or underuse, allowing for quick adjustments that keep labor costs optimized. Together, these tools help prevent budget overruns and ensure resources are used effectively throughout the project.
Watch our short video below to learn more about ProjectManager’s dynamic resource management tools that can improve construction and manufacturing processes.
Manage Costs on Multiple Project Views
ProjectManager’s multiple project views give teams flexible, real-time control over cost tracking and task management from different perspectives. The Gantt chart connects timelines with assigned resources and budget impacts, making it easy to forecast and adjust costs as schedules shift. The sheet view provides a detailed, spreadsheet-style layout for tracking estimated vs. actual costs line by line.
Meanwhile, the task list and kanban board support day-to-day execution and progress tracking, with updates instantly reflected across all views. This seamless integration ensures cost data stays accurate and visible, empowering teams to manage budgets proactively across the entire project lifecycle.
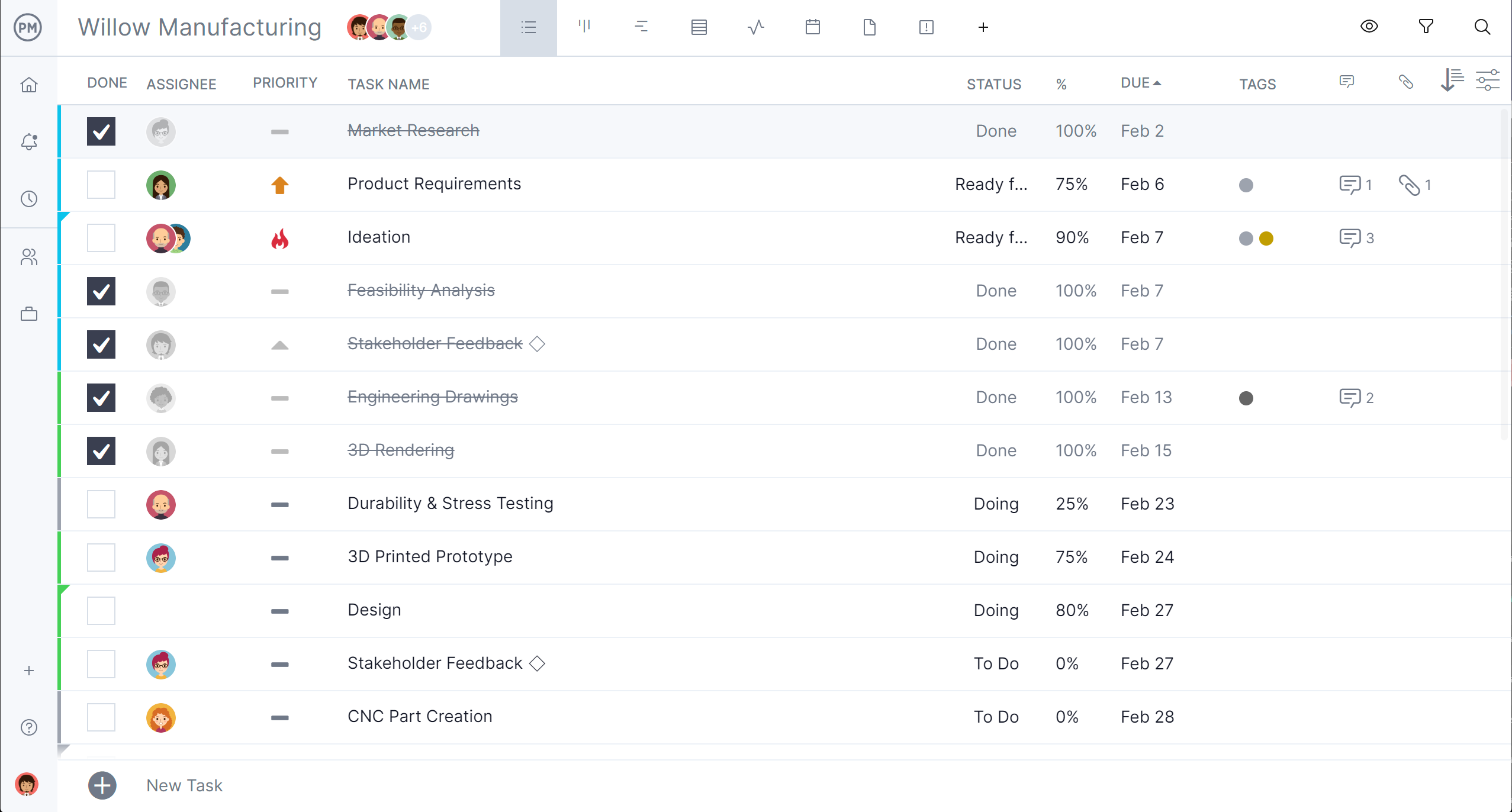
Track Costs With Real-Time Dashboards, Reports and Timesheets
ProjectManager’s tracking tools provide real-time visibility into project costs, progress and performance, helping teams stay on budget and on schedule. Live dashboards display key financial metrics such as planned vs. actual costs, resource usage and task completion in one centralized view.
Customizable reports allow deeper analysis of cost trends, variances and earned value, tailored to specific stakeholders or phases of the project. Secure timesheets ensure accurate tracking of labor hours, which automatically update budget and resource data. These tools enable proactive decision-making, early identification of overruns and continuous alignment between project execution and financial goals.

Related Cost Management Content
Costing methods are but a small part of the larger cost management process. For readers who care to continue to explore this topic, check out the handful of links below. They cover everything from basics to cost control and more.
- Project Cost Management Basics
- Cost Control in Project and Business Management
- Project Cost Estimation: How to Estimate Project Cost
- Cost Overrun in Project Management: Main Causes & How to Avoid Them
- 15 Best Cost Control Techniques
ProjectManager is online project and portfolio management software that connects teams whether they’re in the office or out in the field. They can share files, comment at the task level and stay up to date with email and in-app notifications. Join teams at Avis, Nestle and Siemens who are using our software to deliver successful projects. Get started with ProjectManager today for free.